226 | Power Distribution Module Configuration
Summary
Power distribution modules are rapidly becoming a viable alternative to conventional fuses and relays when it comes to wiring the power distribution circuits in performance applications. In this webinar we’ll take a look at the ECU Master PMU 16 (Power Management Unit) and how we’ve integrated it and programmed it to work in our Toyota 86. In particular we’ll focus on the communication between the PMU16 and the rest of the MoTeC electronics fitted to the vehicle using CAN messaging.
00:00 | - Hey guys, Andre from High Performance Academy here, welcome along to another one of our webinars. |
00:06 | Today we're going to be talking about power distribution modules or power management units, basically the same, two different terms for exactly the same thing. |
00:15 | We're going to find out what they are, we're going to find out why we may want one and then we're going to have a practical look at the inside workings of a power management unit, see how the software works and how we can actually use one in our road cars or our racecars. |
00:31 | So for a start, let's get stuck in with what exactly is a power distribution module or power management unit? And essentially it is a way of allowing us to get rid of all of the relays and fuses that we need when we are wiring up any automotive electrical system. |
00:50 | Now those fuses and relays, those are what we have relied on for decades in order to control the power distribution to different circuits in the car. |
01:00 | Let's say for example you want to power up a fuel pump, you've got an ECU perhaps there to switch that fuel pump on but the fuel pump may pull maybe eight to 15 amps when it's switched on and the transistors or basically electronic switches inside of the ECU can't handle that current flow. |
01:19 | So instead of directly switching that fuel pump on or off, what the ECU does is it switches through an intermediary which is a relay. |
01:27 | So the relay is a high current switching device, allows the low current output from the ECU to switch that relay on and off, supplying current or power through to our fuel pump. |
01:38 | Now at the same time, we also need to protect our circuits because let's be honest, sometimes things go wrong and if we don't limit the current flow and something does go wrong, we can end up melting our wiring or in worse case scenario we could end up with a fire so this is where fuses come in and conventionally in most instances the fuses are non reusable. |
01:58 | Essentially when a fuse, the fusing capability of the fuse is exceeded, so the current flow exceeds what the fuse is rated at, what's going to happen is that the fuse will blow and basically interrupts the current flow. |
02:11 | Now that's good for protecting the circuit but the problem is that if we want to get that circuit up and running again, it requires us to actually remove that fuse physically and replace it so this is time consuming. |
02:24 | Particularly in a racecar because it's going to be pretty hard to do that while you're out on the racetrack trying to drive the car. |
02:30 | Now of course there are other options such as circuit breakers which can be reset but essentially this still requires a operation from the driver or someone in the car in order to actually reset that particular circuit. |
02:44 | So power management units or power distribution modules really aren't anything particularly new, they have been used in professional level motorsport for decades. |
02:53 | The problem is that when they first came in, as with a lot of new technologies they were prohibitively expensive for us at the grass roots or enthusiast level. |
03:03 | Fortunately, as technology has improved and more manufacturers have jumped on producing these units, we've seen the cost drop substantially and they really are now a viable alternative, even if you're building a club level car or just a street car and you want to take your power managed in the vehicle to the next level and we'll talk about the cost as well as those advantages as we go through this. |
03:27 | Of course I should mention, as with all of our webinars, if you do have any questions, please ask those questions in the chat and we'll get through to those at the end of the webinar. |
03:36 | So the power management unit is essentially a box of electronics. |
03:40 | You can think of it as solid state relays that allow the different circuits to the car to be electronically switched on and off. |
03:50 | Now there's some big advantages here, first of all it really dramatically simplifies your wiring installation. |
03:56 | But the biggest advantage really is it gives a lot more control over how the individual circuits in the car are switched on and off and we don't need mechanical fuses for this sort of system. |
04:09 | Instead the current limit for each of the circuits being controlled can be set within the software. |
04:16 | So now that we've got a broad idea of what we're actually talking about, let's just jump across to my laptop screen for a moment. |
04:22 | This is an Ecumaster PMU 16 power management unit, 16 channel. |
04:27 | Just to give you an idea of what it actually looks like. |
04:30 | This is probably about half the size of an old VHS cassette just to put it into some kind of perspective as well. |
04:37 | So obviously every different model from different manufacturers is going to look a little bit different but the same premise really continues across the board. |
04:46 | So here we've got a central stud which is the power supply to the PMU. |
04:50 | So we run this straight from the battery essentially to the PMU and there's a nut that goes on top of that to tighten all of that down. |
04:57 | We've got some status indicators here on the PMU showing the status of each of the outputs and of course there is a connector on the end there. |
05:07 | So that's the entire unit, it's really really tiny, really easy to mount in our car in a convenient location and really easy to run all of our wiring to. |
05:18 | This is a good point to start talking about the cost of these units because as I mentioned, originally they were prohibitively expensive and we still have some of the more premiere ECU manufacturers offering options that are pretty pricey. |
05:32 | I know that this puts a lot of people off. |
05:34 | We've actually used the Ecumaster unit in this Toyota 86 that I'm sitting in right now which is why we are presenting this webinar and I can't remember off the top of my head, I think these are a touch over $1000 USD so in my opinion a pretty powerful device for that sort of price point. |
05:53 | Again sort of gets to a point where it is cost effective for the average club level enthusiast but what we need to understand is where that price point sits with the total scheme of wiring up your car. |
06:05 | A lot of people look at that, maybe it's $1000 USD, maybe they're looking at a more expensive unit that's $2000 USD, they look at that on its own and decide that it's not cost effective for them, it's too expensive. |
06:17 | What you need to understand though is that there are some cost savings that come with using a power management like this. |
06:24 | As I mentioned, it greatly simplifies your wiring and for any of you who have wired up your own cars, the process of wiring up multiple relays, multiple switches and multiple fuses, that can actually be one of the more time consuming aspects of the wiring harness construction. |
06:44 | You could be spending easily somewhere in the region of eight to 10 hours doing just that aspect of it. |
06:51 | Now of course if you are working on your own car and you're not charging your time out, that's one aspect to consider but if you are taking your car along to a professional to have your wiring harness constructed, you really do need to factor in that yes you'll be spending x amount of dollars on a power management unit but that saves you a huge chunk of time. |
07:10 | Eight hours at $100 an hour for example is going to be $800 that you're saving in terms of labour. |
07:19 | So you really need to weight up the entire cost of actually getting your car wired before you consider just the sole cost of the PMU. |
07:26 | Not to mention obviously then there's all of the other advantages that come along with having the power management unit in your car which we're going to get into during this webinar. |
07:36 | Obviously the ability to control the fusing as well as some of the more smart ways that we can control the switching of the outputs. |
07:44 | Alright so in terms of switching the outputs that the power management unit controls, we've got a variety of options available, particularly with the PMU 16 that we're kind of focusing today's webinar on. |
08:00 | We can bring in analog inputs so these are wired directly into the power management unit so I'm talking here about switches that we may have up on the dashboard that the driver can control. |
08:12 | We can also wire in rotary position sensors so you may want to have a control which is multiple position and you can control outputs based on the position of that input that the driver can switch. |
08:26 | Then you can directly wire in analog voltage sensors into the PMU. |
08:31 | Let's say for example, we're going to have a look at a demonstration as we go through this, where we're wired a fuel pressure sensor directly into the power management unit, we've calibrated that and then we've used that to control one of our outputs. |
08:43 | On top of the analog inputs we can also bring in some of our controls via CAN. |
08:50 | And I think in my opinion, this is probably where things get a little bit smarter with the power management unit. |
08:57 | We're seeing most of our late model aftermarket standalone ECUs now as well as dash logging units communicating via CAN. |
09:05 | So again this is a way we can greatly simplify the installation of all of our modules. |
09:11 | We don't need to run multiple switches and wires between our different units but we can for example run a simple two wire CAN bus between the ECU and the power management unit and then we can send messages between the ECU and the PMU to bring in controls for the likes of switching on and off our fuel pumps, switching on and off our radiator cooling fans and that sort of thing. |
09:36 | So again, just really really simplifies down the controls and wiring that we need. |
09:42 | Then we also move into some of the more advanced functionality which we see with these power management units which is the integration of CAN based switchpads or keypads like this one here. |
09:54 | So this is designed to work with the Ecumaster PMU so it makes it really really simple. |
10:00 | It is just a four wire connection on the back of it, if I bring it out, we've got a four pin DTM connector. |
10:06 | This simply has 12 volts in ground and then it has CAN high and CAN low. |
10:10 | Because this particular switchpad is designed to work with the PMU, it's as simple as selecting the keypad from the software and then you can assign each of these buttons to do basically whatever tasks you want. |
10:22 | So again if you just simply consider what it would take conventionally to wire up eight switches and these aren't just eight switches either. |
10:31 | These can have multiple positions when they're powered up as you switch them, you can have different colours for the backlighting to indicate, let's say you want a boost switch so you could have a high and low boost switch and the colour of the backlight will change depending on which boost mode you're in. |
10:49 | So a lot smarter again than just a conventional switch. |
10:54 | So the other aspect which we are using here on our Toyota 86 is, if I just grab it down here, we've got our steering wheel which was on a hook behind me and as is pretty normal these days with a lot of racecars, we're got a range of switches that are set up on this steering wheel. |
11:12 | Some of these are for ECU control functions, so for example we've got traction control and launch control, nothing to do with the PMU, however we've also got a radio switch and we've got a switch for our rain light. |
11:26 | So these all work with a, actually I'll show you on the back of it, a switch pad, Ecumaster switch pad so it's a CAN based switchpad, so basically all of the analog and switch inputs get wired directly onto the switchpad on the back of the steering wheel. |
11:42 | From here again we only need power, earth, CAN high and CAN low and straight away all of the outputs from that switchpad are converted from analog or switched inputs to a CAN message and then they're sent out on the CAN bus so basically anything on the CAN bus can communicate or can get those messages. |
11:59 | Obviously we're got our power management unit, we've also got our MoTeC C125 dash. |
12:04 | That's receiving the information like the launch control and traction control positions, sending that through to the M1 ECU, the stuff that only needs to go to the PMU, the likes of our radio control and our light switches, those go straight through to the PMU. |
12:22 | So let's have a quick look and see what that looks like, so we'll jump across to my laptop screen here and this is the PMU client software that we use for configuring everything. |
12:35 | There's a lot to take in here but what we'll do is we'll just go through it step by step. |
12:39 | So for a start, what I want to show you and this is again one of the nice features of using a power management unit, I'll just switch everything on here and this will come live and we'll just let this cycle through and I'm going to switch that back off just so my battery doesn't go flat for the moment. |
12:54 | So on the right hand side here we've got the ability to log what's going on and we can see the current and the loads in real time. |
13:02 | So this is a time graph, at the top here we've got our total current, so this is the total current being used by the PMU so through this section here, which is where I just keyed the car on, the fuel pumps went through their prime cycle, we can see that our total current flow or total current out of the PMU was around about 21 amps. |
13:22 | We can also break that down, obviously I'm not logging every channel on this graph here, I'm just logging a few key ones that I was interested in. |
13:29 | We've got the ability to look at our fuel pumps here so this car actually has four fuel pumps, it's got two lift pumps and two pressure pumps. |
13:38 | So the two lift pumps here which are in the tank, labelled left and right because they're on the left and the right hand side of the saddle, we can see that those are both running there, both drawing 5.5, seven amps depending on which side you're looking at. |
13:52 | And then we've got our main fuel pump which is located in the surge tank. |
13:56 | So we've got two of those, you can see at the moment we've only got pump one operating, pump two down here is essentially a reserve pump so we can see that our main fuel pump's drawing around about 8.5 amps. |
14:09 | So it's really good to be able to get a glimpse at exactly what is going on with the current in each of the circuits. |
14:17 | So there's a huge number of advantages with this because first of all we know at a glance exactly what is going on, which is really difficult for us to know with a conventional fuse and relay setup. |
14:29 | While it's obviously not impossible to use a digital voltmeter to measure current in a particular circuit, it's definitely not as easy as what we've just looked at here. |
14:37 | The other aspect with this is we can log the current and load on each of the outputs while the engine's running. |
14:45 | The PMU actually has its own internal logging memory. |
14:48 | However for simplicity, what we're doing is we're sending all of the current data for the channels we're interested in through to our C125 dash and we're logging it there. |
14:58 | So the other advantages, if we just jump across to our MoTeC i2 Pro and we have a quick look, here I've got a worksheet set up for our power management unit. |
15:08 | So this actually allows us to view via telemetry, what's going on with various channels in our power management unit. |
15:16 | So this one here specifically we're looking at our diff pump current and our gearbox pump current while the engine's out on track, while the car's out on track and we've got our surge tank pump current there sitting at 11 amps. |
15:29 | So why this is important is that allowing you to monitor this, even if it's on a dash without telemetry we know not everyone's going to have telemetry, what it allows you to do is have a look at historic data and particularly you can start to get an idea from the current flow over time through a particular device, if there is maybe a blockage, particularly let's say fuel pump, as the filter starts to block up, the fuel pump has to work harder so the current will start to increase. |
15:59 | So this can, if you're really careful in monitoring it can give you an idea of where problems lie and you can hopefully preempt that and make sure that you don't have a failure with a component, basically fix it before it fails completely. |
16:13 | Alright we'll head back to our PMU client software though. |
16:17 | One of the really key and obvious advantages with the way these power management units work is the way we control the current flow to the various devices. |
16:30 | So for example, if we have a look at, let's say, our gearbox pump will be fine, we'll double click on our gearbox pump output. |
16:41 | So this is where we can name the device. |
16:43 | So obviously we want to give it a name so we know what that particular channel is, something sensible there. |
16:50 | We've got the ability here to select an output that will suit the current draw from that particular unit. |
16:58 | So here we can see that we're using output 15, 015 and this is a 25 amp rated output. |
17:04 | So that's absolutely fine for this particular output. |
17:08 | However in some devices we can choose to use a double or even a triple pin. |
17:13 | So basically double up or triple up on the outputs and obviously that gives us the ability to handle more current flow on that particular output so we can see here we've got the ability to choose between 25 amp outputs and 15 amp outputs. |
17:27 | So we're basically just choosing an output suited to the particular device we're trying to drive. |
17:34 | The next aspect here is where we can control the current flow. |
17:38 | So here we've got three aspects, we've got our in rush current, our maximum current and our minimum current so let's just go through those. |
17:47 | We'll actually start with our maximum current. |
17:49 | So this, as it's name implies is the maximum current that that particular circuit will handle or will support where it's deemed to be safe. |
17:58 | So essentially if we get to 15 amps of operation or 15 amps of current draw on that particular circuit, the PMU's going to decide, no something's not right and it's essentially going to break that electronic fuse and turn that particular circuit off. |
18:12 | Now where this gets a little bit cleverer or a little bit smarter than a conventional fuse though is that it may pan out that the fuse, we're running right on that fusing current and maybe, yes something isn't quite right but we don't necessarily have to have a complete failure, maybe we could limp the car back to the pits. |
18:33 | So this is where this ability to retry that output comes in. |
18:38 | So you can see here, we've got this set up for this particular output, our gearbox pump, if we do hit that maximum current, 15 amps, and it shuts down, what it's going to do is it's going to wait, in this case one second, that's our retry every number of seconds and then it's going to retry or basically reconnect that circuit and try again up to a limit of eight times. |
19:01 | So it gives us the ability to just let something cool down, maybe we want to actually set that retry timeout to something a little bit longer, may 15 or even 30 seconds, just to allow that circuit to cool down a little bit and then we can retry. |
19:15 | Now of course it's not going to be a solution for a completely failed device, maybe something's gone completely short circuit, in that case, yeah that's not going to fix it but if we're just getting to a point where we're operating right on the current limit, it can be enough to get us through. |
19:31 | And again with a conventional system, you'd need to actually stop and replace the fuse mechanically in order to get that result. |
19:38 | Now the other aspect here is we've got our in rush current and we're got our in rush time so particularly if we look at a device like a fan or a fuel pump, what we're going to find is that when we initially switch that pump on or the fan on, we're going to get a much higher initial current draw and then that's going to step down once the fan's actually up and running. |
20:00 | So this is the in rush current. |
20:02 | And it's going to depend on the particular device, you can of course log it and see what the device is doing under normal conditions but it wouldn't be uncommon for the in rush current to be perhaps as great as twice as much as the normal maximum operating current. |
20:18 | And as you can see here, I've got this set up to allow up to 30 amps for one second and then after that the in rush current is deemed to be over and then it will fuse at 15 amps. |
20:29 | So that's our output there and I just want to sort of go through the workflow for this. |
20:36 | So we'll shut that down, I just wanted to show you the outputs themselves and we can also monitor all of our outputs over here while the engine is operating. |
20:46 | So what we can see from this particular list is we can see the status of each of the outputs, so we can see whether they're off, whether they're active or whether they're in fault. |
20:59 | You can see at a glance here on the left hand side there's a little lightbulb showing which of those are currently active. |
21:05 | You've also got the load, so basically this is a percentage of the available current on that particular pin so basically how hard you're driving or how close to the limit of that particular output you're driving it. |
21:18 | You can see the instantaneous current flow, the peak current flow and the voltage. |
21:23 | So a really nice way of monitoring exactly what's going on with all of the outputs. |
21:29 | Then we've got our analog monitoring, our analog input monitoring so we can monitor all of the analog inputs to the PMU and see what those are doing, again making it really easy for us to see exactly what is being triggered and what is triggering it. |
21:48 | So the workflow that we go through here is that we're going to use either an analog input or maybe a CAN based input to switch our outputs on. |
22:00 | So we need to set up those inputs. |
22:03 | And if we have a look up here in our project tree we've got all of our analog inputs set up here. |
22:10 | So I just want to go through some of these, let's have a look here at our fuel pump signal. |
22:15 | So if we double click on this, so this is a really simple direct wired trigger from the ECU to the PMU. |
22:24 | This could easily be done probably more easily be done via CAN however in this particular installation it is being switched via a direct wired link between the ECU and the PMU. |
22:35 | So again we can give the input a sensible name, obviously fuel pump signal is what we've gone with here. |
22:42 | We can select the pin that is going to be used there, we can select the type of input, in this case it is a switch and it's going to be active when it's switched low. |
22:52 | Then for this particular input we also need to activate a pull up resistor and then we can set basically the threshold for when that switch will be open or closed. |
23:03 | So that's as simple as it is to set up a switched input there. |
23:07 | So that's our fuel pump signal and if we have a look here in our outputs, we've got our two lift pumps, we've got output 13 and 14, lift pump left and lift pump right. |
23:19 | So if we double click on one of these we can see how we've got that set up. |
23:23 | So again, name and the output that we're going to be using, single pin up to 25 amps, no real problem there. |
23:31 | We've got a maximum current in rush of 25 amps and a maximum operating current of 15 amps. |
23:37 | We've got a retry count of 10 and you can see this time, the retry is set for every four seconds, now that's quite likely going to end up with a fuel pressure drop in an EFI car but again just allowing enough time potentially for the pump to cool down for something to allow that circuit to retry. |
23:58 | Then we've got, I'll come back to our PWM configuration, in this case we're just switching this directly. |
24:05 | So you can set a variety of ways to activate the output. |
24:09 | First of all, you can set it to be default, by default be on or off so basically if you want an output that's going to be live every time the car is powered up, you can just default the output to be on, that's relatively simple. |
24:21 | You can also control it via a channel so basically if there's a channel that becomes true, the output could switch. |
24:31 | Or alternatively, this is where it starts to get a little bit trickier, you can use a formula. |
24:35 | So this uses the normal logic operations here to decide on how that output's going to be switched. |
24:44 | In this case, we can see we've got the value for our analog input, MSEL input which is our killswitch. |
24:51 | So basically the killswitch has to say to the PMU that the car is live, that's a given, and on top of that the fuel pump signal also has to be live. |
25:00 | So those are the two conditions there, it has to have both of those or the fuel pump will not run. |
25:06 | Now I'll just come back up to that PWM configuration and this is something that I've found is not actually that common in a lot of the power distribution modules that are on the market here. |
25:17 | Most of them just switch the output either on or off but in some instances, particularly for the likes of a fan or a fuel pump, you may actually choose to pulse width modulate the control here. |
25:30 | You can use duty control, you can set the frequency that the output's going to operate at. |
25:35 | And this can be used essentially for speed control of the device. |
25:38 | So for a fan for example, you may want the fan to come on at half speed up to maybe 100°C engine coolant temperature, above 100°C you might want to go to full speed or something of that nature so you can get a little bit more tricky with the way that operates. |
25:54 | I will mention here that when you are using pulse width modulated control here, this does create more heat in the device and there is some warning here in the power management unit manual if you're going to use that feature, you want to take note of that, basically of load balancing where you've got the outputs that are basically running the most current draw or pulse width modulation so that you don't end up overheating the unit and having it shut down when you don't want it to be. |
26:23 | Alright so that's essentially a look there at our analog input for controlling the fuel pump and how that controls that output. |
26:30 | Now that's a pretty simple device there, pretty simple way of controlling things. |
26:35 | What we can do is start to get a little bit more advanced here. |
26:39 | So I'll show you a couple of ways that we can do this so if we come back down to our fuel pump main. |
26:45 | So these are the two pumps that are in our surge tank here. |
26:48 | So If we click on our first one which is output 12, so this is our fuel pump main one. |
26:52 | So this is our normal output that should be running and we've got the same outputs there. |
26:58 | So the killswitch has to be live and our fuel pump signal needs to be active in order to run it. |
27:03 | However if we come across to our fuel pump main two, what we've got here is the control is a little bit different. |
27:11 | This time we've got our killswitch has to be active and our fuel pump signal needs to be active, same exact conditions. |
27:19 | However this time we've got another condition here that the output for fuel pump main one has been in fault for 1.5 seconds. |
27:27 | So essentially this is an automated redundancy system. |
27:31 | So essentially we're always going to be operating primarily on our main fuel pump one. |
27:37 | However if the PMU detects that the fuel pump one is going to fault, maybe it's gone over current and it's shut down then the system will automatically bring in pump two, so you don't have to do anything from the driver's seat, you may not even be aware that that's happened. |
27:52 | It's a quick and easy way of setting up some redundancy there and this is where we start to get into the true value of these power management units. |
27:59 | Now that system I've set up there is incredibly simple, it's nothing complex to that, your ability to set up complex situations and formulas there is really just down to what you're trying to achieve and how clever you want to be with it. |
28:15 | I'll show you one other way we can do essentially the same thing here. |
28:18 | So what I've got here is an analog input for fuel pressure. |
28:22 | So normally we would run this into the ECU, our fuel pressure sensor into the ECU and maybe bring in fuel pressure via a CAN based message but with this particular unit you can directly wire sensors up. |
28:37 | So obviously, most of it's self explanatory, we've got the name there, we've called it fuel pressure, we've got the pin that that's going into, we've got the type, it's an analog sensor. |
28:48 | Then we've got our configuration there. |
28:50 | So basically at zero we're going to have zero kPa at 0.5 volts, 500kPa at 4.5 volts so a pretty typical 500kPa sensor configuration. |
29:00 | So once that's configured it should then read fuel pressure directly into the PMU. |
29:04 | Once we've got that we can also set up a function. |
29:09 | So we've got that here, function for our switch pump, let's double click on that and see how our function is set up. |
29:15 | With our function, again we give it a name so you see that they're all labelled with A for analog input, O for output in this case, F for function, so pretty self explanatory there. |
29:28 | So we've called it switch pump. |
29:31 | So in this case what we're going to do is look at one of two scenarios. |
29:35 | The first of all is that switch pump, the function is going to be true. |
29:38 | If the output for fuel pump main one is deemed to be at fault. |
29:43 | So essentially exactly the same as what we looked at already. |
29:45 | If it goes over current and it pops the electronic fuse, that's going to go into fault mode so that's the first situation that would make that function true. |
29:55 | In this case though we've got the slightly more advanced one here where we've decided, or the fuel pressure input, our analog input for fuel pressure is less than or equal to 400kPa for one second, if either of those situations is true then the function switch pump is going to become true. |
30:16 | Then we can use that function in our fuel pump control algorithm and basically get a little bit smarter with how that exactly works. |
30:26 | Right the last aspect I'm going to look at here is, no actually not last aspect, the next aspect I'm going to look at here is our CAN based setup. |
30:36 | So this is our CAN messaging setup here so let's have a quick look at that. |
30:43 | So if we double, no if we click on the right thing it will definitely help. |
30:47 | If we click on our CAN message object here, it hasn't got a very inventive name here, it's called message for M and then message object so that's MOB1. |
31:01 | The PMU has two CAN buses so in this case, this is on CAN bus two and the base identifier for this particular message is going to be hexadecimal 702. |
31:12 | So then we can see exactly what's coming through, I'll just power everthing up again and let's just double click on that again. |
31:22 | So now we've actually got all of our data coming through. |
31:25 | So basically you can see what is actually on that particular CAN message and what I'll do is I'll just turn the steering wheel around, one of the CAN messages that we are using here is for our radio so if I click on the radio button on the steering wheel, we'll just watch this particular part of our message here, you can see that that changes. |
31:46 | So that's the base address there, that's all set up. |
31:48 | Now we come down to the actual specific message inputs so in this case this is our radio control. |
31:56 | So we can see that that is under that CAN message that we just looked at on base address 702. |
32:02 | There's some basic functionality for how that is all set up. |
32:06 | We've got our multiplier, divider et cetera, this is obviously just a status bit though. |
32:10 | This is actually really quite smart, basically gives us a CAN sniffer built in. |
32:17 | So you can set all of this up and what we're looking at here is to basically prove that we've got the right CAN message. |
32:23 | So we can see at the moment the result is zero. |
32:25 | As I press our radio button, we can see that our result goes to one. |
32:29 | Again we can see the exact bit changing status so we know that that is all set up. |
32:38 | So once we've got that in we can use this exactly the same way as we can use one of our analog messages and if I can find our radio here, I'll double click on our radio. |
32:50 | And we can see that this, in this case we don't need a formula, this is just controlled via that channel so basically any time our radio button is depressed, that will go live and while it definitely doesn't draw any current because the radio isn't currently in the car, if I click on that we can see that it goes active, it's drawing a massive 0.1 amps, 2% load right now but again we actually haven't got the radio in the car so that's simply just pulling in a relay at that particular point. |
33:19 | Alright we are going to move into some questions really shortly so good place to just stop and say if you have got any questions about anything that I've talked about so far, please feel free to ask them. |
33:31 | Now there are a couple of other functions that I just want to go over in the PMU as well before we move on though. |
33:40 | One of those, this isn't really specific to the PMU, this is really something that's incorporated in any power management unit, is the control for wipers. |
33:50 | So if you are going to be hooking wipers up to a power distribution module, what you're going to need to know is that most wiper motors will have what's referred to as a park position. |
34:02 | So this is some feedback from the wiper motor back to the PMU to essentially tell the PMU that the wiper is in the home position. |
34:10 | So this just makes sure that when you actually turn your wipers off, you don't end up with the wipers stuck half way up the windscreen. |
34:15 | And it's not essential to use it but it is a nice feature. |
34:19 | Most wiper motors will also have a high speed and a low speed. |
34:22 | So you'll generally find that there will be some specific information in the manual showing you exactly how to hook up windscreen wipers. |
34:29 | This is important because in the likes of the PMU here, the PMU 16, you have to use a specific output for the low speed wiper if you want to incorporate the home position analog input to the PMU. |
34:45 | What else did I want to mention? The other aspect that is quite useful as I mentioned is the ability to log directly into the PMU. |
34:55 | However just because I like to try and keep all of my logging in one place, it's also just as easy to end up outputting all of that information via a CAN bus message. |
35:07 | So once you've got that, and we'll just have a quick look at how I've got that set up. |
35:10 | If we head across to our MoTeC C125, I'll just go back one step. |
35:14 | If we go into connections and communications and on CAN bus one here I've got a Ecumaster PMU CAN bus receive message, this is pretty basic but just some of the channels that I'm interested in logging so that will then log into the C125 and of course as I mentioned, you can send that out over telemetry if you're so equipped. |
35:39 | Other aspect that I really like with the PMU is that it does have a built in gyro. |
35:45 | So this is a three axis gyrometer, G sensor, so you can log all of that information and where that really comes into its own though as well is that you have the ability to configure an interia switch. |
35:57 | So I've double clicked on that and I'll show you how that works. |
36:00 | I'll just drag that up so it's a bit more visible. |
36:02 | So at the moment it's disabled but if you click enable here, you can essentially set an acceleration or G force threshold above which you've essentially said, hey, I've had a crash, something's not right. |
36:13 | So in this case if you exceed 6G, basically the PMU will shut off all power so it's just another safety aspect there to make sure that you're not going to end up with any of the systems running in the car, less chance of having something short out electrically and also of course you don't want your fuel pumps running if you have had a crash. |
36:34 | So quite a nice feature that's added in there. |
36:37 | The other thing I will talk about here is our CAN keypad. |
36:41 | I haven't really touched on that, so I've touched on it briefly I should say, so we'll just have a quick look there. |
36:47 | So really easy to incorporate those CAN keypads into the PMU. |
36:51 | So in this case you can choose the type of keypad you're using as well as where it is connected and then you can obviously select what each of those buttons is going to do and the functionality of those buttons. |
37:06 | You can also export the state of those buttons onto the CAN bus as well so you can log those elsewhere if you want. |
37:14 | So the one that I've got at the moment that I've just showed you is actually not being used at the moment so we don't actually have that fitted to the car which is why it is so basic. |
37:24 | But you can purchase these with a variety of different little inserts that you can put in based on the function of the particular button. |
37:32 | Alright so I think we'll get into some questions now, probably enough talking from me. |
37:35 | So if you do have any more questions, please fire them through and we'll see how many of those we can get through, so let's have a look. |
37:51 | Plohl has asked, overall how have I found mixing and matching the PMU 16 with the MoTeC? Pretty seamless really. |
37:59 | These days, I'm not really sort of in a situation where I think you have to use all of the same brand of product. |
38:07 | These days with CAN bus integration, yeah it really does open another pathway to using multiple products from different manufacturers so you don't have to stick to the same brands. |
38:18 | What I would say though is that if you want to use some of the more advanced functionality then you do need to have a little bit of knowledge with CAN bus programming and how to set up a send and receive template. |
38:29 | We do have other webinars that do cover this in some detail so for our members if you are interested in learning about that, check out, search for CAN bus in our webinar archive and there's a couple of webinars in there that cover that. |
38:42 | So what I'm talking about here is that in the MoTeC C125 dash, there is no default configuration for receiving information from the power management unit so I had to set that up myself. |
38:54 | It's really not rocket science here, all of the information on the CAN template that the PMU sends is available in the manual so it's really just a case of making sure that you follow that through. |
39:05 | The fact that the PMU essentially has that built in CAN sniffer, really really powerful because it makes it so easy to see exactly what messages are changing on the CAN bus and make sure you've got everything correct. |
39:19 | Greg has asked exactly the same question with the Link. |
39:23 | And my answer is exactly the same. |
39:27 | Link is probably one of the ECUs that actually has the most powerful user adjustable CAN bus for both receiving and transmitting. |
39:38 | So not really a lot that you can't do. |
39:40 | Just to link that back to that last question there, with the MoTeC actually the M1 in stock form is quite restrictive on the CAN bus, it has to be seeing messages on a particular format which means that if I was trying to send and receive just between the M1 and the PMU, that actually could get a little bit tricky. |
40:01 | But because I've got a MoTeC C125 dash, that again just like the Link, very very powerful in terms of the ability for the end user to manipulate the CAN bus so I kind of use it as a CAN gateway. |
40:14 | So kind of off topic but with the CAN keypad on our steering wheel, that communicates to the MoTeC C125 dash where I can receive the messages in the format that the Ecumaster switchpad is sending out. |
40:27 | I can then reconfigure what I need for the likes of launch control and traction control and send them back out to the ECU in the format that the M1 ECU is expecting to receive. |
40:38 | Probably a little bit off topic but it is a slightly complex question so I thought I'd be a bit more thorough with my answer. |
40:45 | Mike has asked, is it possible to use the CAN switchboard with any ECU that can receive CAN messages. |
40:51 | So the answer to this is yes and no. |
40:54 | CAN is just a generic way of sending and receiving messages, the key here is that while yes the CAN switchpad will work with any ECU, you do need an ECU that has enough user configurability in the CAN bus to allow you to actually receive those messages and then do something useful with them and definitely not every ECU falls into that boat. |
41:19 | Spirit R Garage has asked, can the PMU be tied to the engine protection features on an ECU for example for fuel pump failure? Just trying to think how I would word an answer to that. |
41:33 | The reality is there's really nothing you can't do. |
41:37 | I would probably be separating those. |
41:40 | So what I'm getting at with this is we're using the PMU more as a redundancy system so something that's going to allow us to get the car going, it might not be perfect but hopefully to get us back to the pits or somewhere where we can actually affect some more permanent repairs. |
41:56 | The engine protection functionality in the ECU I feel is more around the lines of something that we need to instantly stop the engine in terms of protecting it. |
42:05 | So example there would be maybe protecting the engine against a low oil pressure situation. |
42:13 | Probably wouldn't be tieing that into the PMU, or maybe a lean air/fuel ratio situation so yeah I think the two are quite different in what their intention is and how I would set them up. |
42:25 | Barry has asked, I mentioned that we were running two lift pumps on the left and right for the fuel tank so I assume you're using a saddle type fuel tank, yes correct. |
42:34 | I notice you didn't have the lift pumps configured to have a minimum current setting, how are you handling a situation where one side of the tank runs dry for whatever reason, or are your lift pumps capable of running dry for some time? Barry you don't miss much, that is a very very subtle aspect that you've picked up on and you're 100% correct. |
42:52 | So let me go into that because unfortunately, the PMU doesn't quite operate exactly how I'd like it to. |
43:00 | Just like you, this is a problem that I had picked up on and was a little bit worried about so when I saw the configuration of the PMU, I looked at it and thought OK well we've got a maximum current and a minimum current, this is going to be perfect. |
43:12 | Obviously if one side of the saddle tank is dry, the pump's going to be sucking air and what we end up with is the current for that pump dropping low. |
43:23 | So let's say for example under normal conditions, should be drawing maybe four to five amps, if it's sucking a lot of air we might see that that drops to one, 1.5 amps so I thought, great, I'm going to use that minimum current and if my current drops below two amps, we're going to put the pump in default and shut it down. |
43:38 | Unfortunately that doesn't work, I guess it's because it's deemed that low current isn't dangerous so it actually still drives the pump however it does bring up a fault condition under current. |
43:50 | Now while I'm talking about this, this is how we've got it set up at the moment, I did this last minute, basically we were about to load up and head to our race meeting. |
44:00 | So I didn't get a chance to really get too far into detail, what I am considering doing is looking at whether we can use that fault message in a different way to then shut down the pump. |
44:10 | So haven't quite given up on that. |
44:12 | However in our situation because it is a racecar, we're always going around corners, while yes it's definitely not ideal to have a pump running dry, you're going to end up overheating it and burning it out, what we're going to end up doing is when we're really low on fuel, always having fuel slosh side to side, so not a permanent solution but that's where we got to with it. |
44:31 | Hopefully that explains everything. |
44:36 | 98Mystique has asked, is there any soft start or voltage foldback for outputs? So yeah I didn't actually touch on that so if you are using the pulse width modulated output option, then you can also integrate or choose to use a soft start. |
44:50 | So again for some of those outputs that have a high in rush current, maybe a really large electric fan or fuel pump, you can basically set the PMU up to basically bring the current flow into them, slowly rather than instantaneously turning them on to limit the in rush current. |
45:09 | Dave has asked, have you ever used any other PDMs or software or are they mostly similar? Also maybe a silly question but can you use PDMs with different software, meaning can you use an Ecumaster PDM with Haltech's PDM software? OK so first of all, have I used other PDMs? Yep up until this point I've been dealing mainly with the MoTeC PDMs. |
45:29 | Excellent PDM as you'd probably expect with anything with the MoTeC label on it. |
45:34 | Also have dealt off and on with the race, race, no what is it called, Smartwire, Racepak, Racepak Smartwire. |
45:45 | Hopefully we've got no one from Racepak watching but definitely not a product that I was in love with. |
45:50 | And the reason for that was that while physically the system works, I mean it is just solid state switching of outputs, where I really struggled with the Smartwire was that the software just didn't have the flexibility that we see with the likes of MoTeC and PMU with our Ecumaster unit there. |
46:10 | So yeah no my favourite but those are the only other two that I have worked with. |
46:14 | No you cannot use another manufacturer's software with the PDM, it's essentially the same as an ECU, you couldn't tune an Ecumaster with MoTeC software, same goes for their PDMs. |
46:29 | Mikael has asked, since you mentioned open source at the beginning, is this interface compatible with Linux? Probably a little bit off topic in terms of the tuning versus PMU but no, you're going to be using the PMU software there. |
46:48 | Greg has asked, would you wire any outputs from the ECU to PDU inputs or would you send it all via CAN? So in a perfect world, I would always choose to send everything via CAN. |
47:00 | It's just easy, it's quick, it's neat and tidy and you've got a lot more control over everything so if I don't need to make my life any harder and make more work for wiring, I won't. |
47:12 | In this instance, as you saw, despite the fact that we've actually got ability to do this, right now we have got the fuel pump controlled by an analog input. |
47:20 | The reason for this was simplicity, we already had an output from the M1 ECU which sits literally three inches away from the PMU to run the fuel pump. |
47:30 | We changed the fuel pumps around so it was as simple as just reterminating that into the PMU header. |
47:37 | Jack has asked, on an older car what do you think of keeping a portion of the stock fuse relay system and feed the main fuse box from the PMU and then feed the upgraded or added option directly from the PMU. |
47:47 | Look there is no right or wrong way of doing this. |
47:50 | There really is the flexibility up to how you see fit to do things. |
47:54 | What I would see is a lot of times, let's say you've got an older car where you're performing an engine swap, then you may choose to use the existing, or retain I should say, the existing vehicle electronics, so I'm talking here about brake lights, headlights, gauge cluster et cetera. |
48:12 | And then add in a PMU for your engine related operations. |
48:17 | Obviously in the perfect world you would probably want to run everything through the PMU but if you've got an existing wired car that's all operating and up and running then that actually ends up making quite a big job so PMU integration, perfect if you literally have a bare shell and you don't have a single wire in the car already, obviously under those situations we'd want to use the PMU or more likely multiple PMUs to control every circuit in the car. |
48:44 | Definitely not the only way of doing it. |
48:49 | Darius has asked, how do you connect to the PMU, is it via USB to CAN module, and can you do it through the ECU via USB connection? So yeah with the PMU it is a USB to CAN adaptor, wires into one of the two CAN buses. |
49:05 | So no you can't do it through the ECU, through the ECU software. |
49:11 | Two different applications, however with the Ecumaster ECUs, these are also tuned, programmed, controlled via their USB to CAN so it's essentially the same adaptor just a different application you're talking to. |
49:26 | Evocdn has asked, what is the maximum number of circuits you could run on this PDM, both analog and CAN based and the maximum amperage per circuit? OK you're probably going to be best to spend a little bit of time on Google, have a look at the PMU 16. |
49:43 | As it's name implies, it's a 16 channel output, not all of the channels are rated at the same current so it really depends what you're trying to do, there's a number of 15 amp ouputs and a number of 25 amp outputs. |
49:54 | These can also be doubled up or even tripled up if you need more current capability. |
50:00 | So really it depends on what you're wiring it up to because if you're doing a lot of, you're controlling a lot of circuits with high current draw and you're doubling up a lot of the outputs then obviously that's going to reduce the number of outputs that you've got available. |
50:13 | Also again off the top of my head, can't remember exactly how many analog inputs there are. |
50:18 | CAN based essentially there's no limit there, it's just down to defining another CAN message. |
50:27 | Darius has asked, why not use the accelerometer in the PMU to switch between left and right fuel pumps? Well Darius this is the exact scenario where the limitations of the PMU really come down to your thought process and how smart you want to be. |
50:42 | Not 100% sure off the top of my head if that's something I want to do but there's absolutely no reason why you couldn't do it and there you could then test and see if it's effective so yeah a lot of flexibility just down to the end user and your own preferences in what you're trying to achieve. |
50:59 | Alright team that's got us to the end there, some great questions in there so thanks to everyone who has joined us. |
51:05 | Hopefully you've got a more rounded idea on what exactly a power management unit is. |
51:10 | Hopefully not you've got a better idea of where that would fit in with potentially one of your own project cars and a better understanding of how they fit in in terms of overall cost and the advantages that they can offer. |
51:23 | As usual, if you've got any other questions about this webinar after it's aired, please feel free to ask in the forum and I'll be happy to answer them there. |
51:31 | Thanks for joining us and hopefully we'll see you all again next time, cheers. |
Timestamps
0:00 - Introduction
0:30 - What is a PMU and why do we want one?
5:15 - Cost
7:45 - Analogue inputs
8:40 - CAN bus inputs
9:00 - CAN based switchpads
12:20 - PMU software overview
14:35 - Logging
16:15 - Controlling current flow to devices
20:30 - Output monitoring
21:30 - Analog input monitoring
21:50 - Workflow
30:30 - CAN setup
33:30 - Wiper control
34:45 - Logging setup
35:35 - Built in gyrometer - automatic power shut off
36:35 - CAN keypad
37:50 - Questions
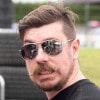