296 | Traction Control Strategies
Summary
Traction control can be a valuable addition to any vehicle that produces more power than it can reliably put to the ground, particularly if it happens to be raining. In this webinar we’ll discuss traction control options and see how these can be applied using the MoTeC M150 ECU.
00:00 | - Hey team, Andre from High Performance Academy, welcome to another one of our webinars and in this lesson we're going to be diving into the world of traction control, specifically on the MoTeC M1 platform. |
00:11 | Today I am in our SR86 which runs the MoTeC M150 ECU. |
00:17 | This runs their Toyota 86 engine swap paddle shift package. |
00:22 | Bit of a mouthful but essentially it doesn't really matter specifically what car we have this ECU in because the traction control strategy used in that package essentially mirrors the GPR package and what you'll find in a lot of the other targeted packages for particular vehicles. |
00:41 | We have been running traction control in our two 86s on the M1 platform for years. |
00:48 | Our original Toyota 86 was one of the very first shipments here to New Zealand, 2012 model and I think it had the MoTeC M1 platform in that from about 6 months of age so we were pretty quick on the mark to get that ECU in and I've had plenty of experience with that car more so than this car in the dry, the rain and everything in between on a variety of different tyres and I can say that the traction control strategy that MoTeC use is exceptionally powerful and it works really well but like anything, it's only going to work as well as the way you've got it set up. |
01:24 | Just to give you a quick look into how this works, let's just jump across to my laptop screen. |
01:30 | This is actually pretty old now but this is a screenshot that I took which kind of shows you what's going on here. |
01:38 | So this from my memory, this is a while back, this is a acceleration run on a completely soaking wet road in second gear. |
01:46 | And what we've got here, a couple of parameters that are of interest. |
01:50 | We've got our engine speed which is in light blue and then in darker blue we've got our engine speed limit ignition, in green, we've got our traction engine speed limit. |
02:00 | So traction engine speed limit's really what we're looking at here and what we can see in this particular set of data here, we've got our throttle position. |
02:09 | So basically at this point here we've gone to full throttle on a wet track and what we can see, if we look at the light blue RPM trace, we can see, I'll just highlight that, it's sort of bouncing all over the place and that's because the car is wheel spinning, it's hitting that traction engine speed limit, the ECU's coming into play, it's using ignition cut in this particular case to limit the wheel spin, the car's gripping up again and it's repeating that whole process. |
02:36 | So this is overkill, this is an exaggeration because you can see I'm basically at 100% throttle the whole way through here. |
02:44 | Obviously you wouldn't necessarily do that, it does show how powerful the traction control can be. |
02:50 | We can see how that's panning out down here, we've got our ignition output cut count. |
02:54 | So this is the ignition cut that is being used to control the RPM limit and we can see that basically from where I go to full throttle, that's kind of stepping up, it's a little bit more aggressive once the RPM climbs up and we get onto boost. |
03:09 | So that's how it all can work out. |
03:13 | And I do recall basically when we were first testing this ECU in our other 86 development car, we were at a racetrack on a completely pouring with rain day and we were on a very basic street tyre, nothing particularly flash, not a race designed wet weather tyre and I basically set the traction control up. |
03:37 | Come through a hairpin which was a second gear corner and essentially got to the apex and basically went straight to full throttle and what happened was that the car stepped out exactly as you'd expect but rather than looping me out to the outside of the track in a big spin, basically once the traction control took over, it just required a little bit of opposite lock and I could basically drive out of that corner at full throttle and the ECU was doing a lot of the hard work so again really can be quite powerful. |
04:07 | So how, I guess why we would want it should go without saying really. |
04:13 | If you've got a powerful 2WD car, then most instances, particularly in the lower gears, you may have the ability to exceed the available grip from your tyres. |
04:24 | Now that's on a dry road perhaps but obviously things get worse when it's wet so you've got the ability to easily exceed the available traction and that traction control there sort of, a design is a bit of a safety backstop to limit the amount of wheel spin you can generate. |
04:40 | Obviously there's the argument as to whether or not it's cheating, whether it takes away from driver skill and I mean there's no real argument here, it obviously does take away from the driver's requirement to control wheel spin using the right foot. |
04:55 | Whether you want that or not, that's totally a personal preference but generally here at HPA we like to embrace technology so if we've got the ability to let the ECU take some of the stress and strain away from the driver, well my personal opinion is why not do that. |
05:10 | So the general premise on how it works is essentially monitoring the wheel slip in some way shape or form, we'll get deeper into this as we go and there'll be some target slip ratio between the driven and the undriven wheels. |
05:24 | And when the slip exceeds that target, then the ECU is going to use some type of cut, be it fuel or ignition cutting in order to maintain the slip ratio or the slip target that we're aiming for. |
05:38 | And reduce excessive wheel spin. |
05:40 | There are some potential downsides though to reducing the engine torque using cuts, there's some potential downsides to reducing the engine torque through the traction control strategy anyway so we do want to dive into that, we'll talk about those in more detail as we go through today's lesson and we want to do our best realistically to minimise the amount of traction control we need. |
06:06 | And that's something that I think a lot of people overlook so we'll dive into that too. |
06:11 | Now it's also worth mentioning here that there's traction control and then there's traction control and what I mean by this is not all traction control strategies are born equal. |
06:22 | So if we compare on our 86 platform, the factory ECU has a traction control strategy as do most late model factory cars and I can assure you it is complete garbage. |
06:34 | It has a traction control strategy by default and then if you want, you can enable sport mode which sounds pretty great for those who attend track days. |
06:45 | The reality of it is when you actually start using the factory traction control, is that it's completely overbearing and yes it will prevent wheel spin but you're certainly not going to get around a racetrack very fast using it because it's overly aggressive with its torque reduction strategy so it's essentially almost like a case of you get a little bit of wheel spin and someone turns the ignition off on you and it takes an eternity to really get back to full power so not something that's designed really for performance, it's really designed around keeping the car on the road and that can be great, particularly for a novice driver who isn't very experienced but again it's not something that's going to work well on the racetrack. |
07:27 | Compared to my story previously of the M150 in our 86, obviously chalk and cheese, the difference between them. |
07:35 | I've also had experience with our Nissan 350Z which had the ability to switch between multiple ECUs and we've used that car on the racetrack, it's been retired for the time being and again, not all strategies are equal, we've got some where the traction control strategy would work in so much as it reduces wheel spin but it physically did make the car slower because again it's overbearing in the amount of control it has and the amount of torque reduction. |
08:03 | Now also we want to talk about what we're actually trying to achieve with our traction control strategy, while I'm talking about this, I'll just see if I can find another picture. |
08:13 | Which might be a bit of a struggle here. |
08:17 | No I'm not going to be able to. |
08:20 | That's OK though, what we need to understand is the way a racing tyre or actually for that matter, any tyre that generates grip. |
08:30 | So you might think that generating maximum grip we would have absolutely no slip, the tyre would be completely hooked up on the racetrack or the street or whatever surface we're driving it on. |
08:40 | The reality is that we actually get a slight improvement in the amount of grip that the tyre can provide with a very small amount of wheel spin or wheel slip. |
08:51 | It's going to depend on a lot of factors, it's going to depend on your particular tyre that you're running, it's going to depend probably on your car and your suspension setup but generally somewhere in the region of about 5-6% slip or wheel spin actually provides an improvement in our straight line acceleration, we'll get maximum longitudinal acceleration with a little bit of wheel spin. |
09:14 | So that's important to understand because this sort of feeds into our traction control calibration and tuning, we don't want to aim for 0% slip because that will be actually reducing our performance. |
09:27 | The other reality is that we're always going to see, if we're monitoring a wheel slip channel in the ECU, we're always going to be seeing some amount of wheel slip, particularly out of slower corners, even if as the driver you're not necessarily noticing or picking up on any wheel spin. |
09:44 | So if we were setting our wheel slip target to 0 or 1 or 2%, we're essentially going to have that traction control strategy kicking in and becoming overbearing pretty much all of the time, particularly out of our slower corners so we don't want that. |
10:00 | The other thing and this is probably, this is my personal take on it, I do feel quite strongly about this, is that the traction control strategy, we want to have that in there as a bit of a safety backstop. |
10:16 | Now a lot of tuners would think or a lot of drivers would think that we can just rely on the traction control and feed the engine as much power as it can produce straight from first gear and then just let the traction control pick up the pieces. |
10:31 | Now yes technically that is correct, technically we could do that and the traction control strategy very well probably would do a reasonable job of doing that but it gets back to that situation what I was talking about just before if we had a very low slip target. |
10:46 | What that would result in is the traction control strategy working very very hard and almost any time we are at full power or wide open throttle or anywhere close to. |
10:56 | Now there can be some implications to the way the engine operates with that as well. |
11:02 | We're going to be relying on very very high levels of fuel and ignition cut, depending which one of those we are choosing and that's not necessarily good for the engine. |
11:12 | Particularly ignition cuts can be quite dangerous on a lot of engine designs but essentially if you've got a highly stressed engine making very high specific power levels, we don't really want to be using a lot of cutting, this can cause some problems with engine reliability as well. |
11:32 | So while I don't want to scare you off using traction control, what I'm talking about there really is more along the lines of very high powered drag engines which are producing very high specific power levels. |
11:45 | We don't really want to be using any more cutting than we absolutely need. |
11:50 | What we want to do is essentially try and manage our torque delivery in the first instance so that we're matching the amount of torque the engine produces with what it can actually put to the track. |
12:05 | And then if we've done a good job of that we shouldn't be relying too heavily on our traction control and that should be there just in the background to pick up the pieces if things do go wrong. |
12:15 | So again, just to reiterate, this is my personal take on things. |
12:18 | I know there's probably people out there who will disagree but for me, I think of traction control a little bit like knock control. |
12:26 | It's not there as a bandaid for tuning the ignition table properly, we still need to tune the ignition table properly and the knock control strategy should be there just to pick up the pieces and retard the ignition timing if knock does occur for some odd reason. |
12:44 | The other aspect, how that relates to traction control, just like knock control, it is reactive, it's not predictive. |
12:50 | So if you've got a large amount of wheel spin, that actually can allow potentially, particularly if you've got a lot of lateral acceleration at the time, it can actually allow the car to get quite out of shape before the ECU can actually bring in any cutting as well so it's not a guaranteed save all feature, we do need to recognise that so just wanted to mention that. |
13:14 | Now I'll just quickly cover off what I mean by torque management, I'm not going to go into too much detail because we recently did run a complete webinar on that. |
13:23 | If you want to check that out, it's in the archive, webinar number 290 which was on torque management. |
13:29 | So what is it? Basically what we're trying to do is manage the amount of torque the engine delivers. |
13:34 | As I mentioned, so that we're matching what we can put to the racetrack. |
13:38 | And there's a few different ways we can do that and just to make this a little bit more interesting, I will just go through this with you. |
13:45 | So let's dive into my laptop screen for a moment here. |
13:48 | And what we'll do is we'll just come back over to our tuning tab. |
13:51 | So boost control is one of the most obvious ways if we do have a turbocharged engine because we can step the boost up dependent on the gear or wheel speed or whatever we want so if we come down through here, we've got our boost limits and gear, boost limit is what we want to look at. |
14:12 | So here we've got the gear that the vehicle's obviously in and we've got our boost limit. |
14:17 | So this works, you can see the numbers here basically 0-100% and basically it's a percentage of our boost target or boost aim main. |
14:28 | Some other subtleties there, I don't want to get too deep into it, we're not a webinar here on boost control but essentially for all intents and purposes, that's exactly what it is so we can see in this setup here, we're targeting our full boost by 3rd gear, in first gear obviously we are quite traction limited, we're 70% and then we step it up to 80% so that's the first one, under wide open throttle acceleration, we're trying to match our engine power and torque to what the track can take. |
14:56 | Another way we can do this is with boost versus throttle position as well. |
15:02 | That's more of a driver control aspect but I do like to step up the boost targets as the throttle is open. |
15:10 | A good aspect or a problem I should say with turbocharged vehicles is they are very good at producing boost and what this does, if we have all of our boost, our main boost target right the way from closed throttle to 100% throttle is that the ECU can probably maintain maximum boost, our target boost down to maybe 40 or maybe 50% throttle and this gives a very non linear relationship between our throttle position and our engine torque so by manipulating our boost target versus throttle position, that can help the driver because the torque reduction will be a little bit more linear in relation to our throttle opening. |
15:47 | Another one I wanted to mention here if we come through to our initial setup 2 and our throttle pedal table here, throttle pedal worksheet. |
15:56 | So a variety of ways of doing this, I'll just full screen this here. |
15:59 | So we've actually got the throttle pedal mapping on a rotary switch on the steering wheel and that allows me to adjust a couple of things together. |
16:10 | It'll adjust the boost target and the throttle position target. |
16:14 | So let's just make this, so at the moment we're on boost position, sorry that rotary switch position 4 which is the maximum, we've only got 0 through to 4 on that switch. |
16:24 | And we can see on the left hand side here is our throttle pedal sensor so that's the accelerator pedal, that's the driver's foot pedal position and the numbers in this table are our actual throttle position as applied to the throttle body so if we come back across though and we go to 0. |
16:46 | So this is my wet weather map if you like and what we can see here is that down where we are off boost, I'm still targeting 100% throttle opening up to 4000 RPM and then essentially as we go 5000 and above and the turbo does reach the ability to make full boost, I'm dropping that throttle position quite dramatically and that allows me to really tailor the amount of torque really really accurately with a lot of control to what the track can take. |
17:15 | Another little trick that we are running in this particular vehicle is that in first gear we have reduced the maximum throttle opening that the drive by wire throttle body can go to, I think we're about 78% or something like that. |
17:28 | Again just because even with the reduced boost target, the vehicle just makes more power and torque than we can put to the track. |
17:36 | So those are a few of the aspects that are within our control and it does make a big difference and again if you want to learn more, webinar 290. |
17:46 | Alright what we'll do is we'll get a little bit more involved in the specifics of the traction control in the M1 ECU and how it works. |
17:53 | And every ECU has a slightly different way of doing this. |
17:58 | In my experience so far, most ECUs with traction control tend to give the tuner a slip target, so a wheel slip percentage and from there they'll do some kind of PID based closed loop control of fuel, ignition, cut, depending how you've got that set up in order to try and maintain that slip target. |
18:22 | This can work and there's nothing necessarily wrong with that but it can be confusing for the tuner to set up. |
18:31 | It requires a lot of testing to get it right and it's in my opinion probably a little bit sophisticated and a little bit clunky to actually get it working really nicely. |
18:41 | A good tip if you are in that situation and you don't really know what numbers to start with with your PID gains, would be to talk to the ECU manufacturer and ask them if they can give you some ballpark numbers to at least get up and started. |
18:54 | The reason for this, if you've gone through any of our courses that cover the PID tuning algorithm and how you set your proportional, integral and derivative gains is that it's pretty tricky because we actually need to produce a step change and see how the ECU responds, how the control responds. |
19:13 | So a good example of this would be closed loop variable cam control. |
19:17 | When we're setting up proportional, integral and derivative gains what we'll do is target let's say 10° cam angle and then we'll step it to 30° and we want to see how the system responds. |
19:28 | It's very difficult to do that when we're trying to target a specific slip target. |
19:33 | There's a lot of stuff going on out there and it can take a lot of testing to actually go and gather data so you can see how the different gain values work so the MoTeC does this in a different way which I actually think is pretty smart. |
19:48 | Talking to MoTeC just a week or so ago it looks like or sounds like they are potentially going through some slight changes in how that strategy works. |
19:57 | But for now at least, the way this works is that the M1 does give us a target slip percentage, so nothing particularly new there, we'll have a look at that as we go through. |
20:08 | Actually let's just jump into it right now, no point not. |
20:11 | Come over to our race functions and we are on our traction control tab, worksheet here. |
20:18 | And the first place we start here is our traction aim main. |
20:22 | So again we've got the ability, if you do have a rotary switch to change the slip target based on the position of that switch which is nice, I'm going to talk about why that's really valuable as we go through this so we can adjust our slip target there. |
20:38 | How this works in the MoTeC though is that then the ECU converts that slip into what is referred to as the traction engine speed limit. |
20:47 | So how it does this is it is a little bit complex, actually let's start with why it does it that way. |
20:54 | This is because as far as the functions in an ECU, the engine speed limiting, rev limiting in general is something that's pretty well developed, just about every ECU manufacturer for obvious reasons has a really good handle on getting the engine speed limiting to work really accurately and really well and ultimately that's kind of what we're trying to do, we're trying to control the engine speed limit. |
21:19 | So what the MoTeC M1 ECU does is it takes the slip target and it works that back, basically it knows what the wheel speed is and it needs those inputs in order for traction control to work which should be relatively straightforward to understand as well and then it knows for a given wheel speed, we've asked for a slip target of, let's say 10% for example so it can calculate then what the increase in wheel speed would be that correlates with that 10% slip so let's say we're at 100 km/h rear wheel speed and we've got 10% slip. |
21:54 | Obviously that 10% would be 10 km/h, 10% of 100 so 110 km/h for our driven wheel speed, that if our undriven wheels, our front wheels remained at 100 km/h, that would be our 10% slip. |
22:07 | So what it then does is it converts that based on the wheel circumference, wheel diameter, the final drive ratio and then the current gear ratio and it calculates what that would look like in terms of an engine RPM. |
22:25 | So once it knows that, it can then apply that as our traction engine speed limit. |
22:30 | So hopefully not too complicated to understand, it is reasonably simple ultimately but it's just kind of reverse engineering that slip and turning it into an actual engine speed limit and once it knows that engine speed limit it can then apply that. |
22:46 | So if we come back across to my laptop screen, that is what we were looking at here. |
22:51 | You can see the blue line, that is our traction engine speed limit and you can see at the start before I go to full throttle, it's sitting right up here basically off the screen and then as we come into our traction control and it becomes inactive which we can see down here, engine speed limit state, at this point as traction control, that is what is doing the engine speed limiting. |
23:13 | And we can see that that normally will just sit just marginally above the actual engine RPM when no wheel spin is occurring and of course when wheel spin does occur our engine RPM will flare up, it'll hit that engine speed limit and then the ECU can take some precautionary preventive measures. |
23:30 | So that's how the M1 actually deals with the traction control strategy. |
23:37 | However there are some intricacies with this. |
23:41 | First of all which we're going to go over very shortly, it does require you to have a good understanding of how the M1 engine speed limiting works and not too complex once you understand it but you do need to know how that works. |
23:56 | You also do require all of the inputs for things such as your wheel speed, your diff ratio and your gear ratios to be 100% correct. |
24:06 | Otherwise this calculation isn't going to work and it can get you into trouble. |
24:11 | An example of that is that recently on this particular car we have a set of dry weather tyres which are a full slick and we also have a set of Michelin wets which we run when the track is wet. |
24:26 | There is a small but definitely measurable difference in the circumference of the wet tyre versus the dry tyre and the MoTeC M1 ECU gives you the ability to change the circumference there and at one point we ended up somehow with the wet weather circumference on one end of the car and the dry weather circumference at the other end so obviously then the wheel speeds are basically off and this will result in slip being measured even when there is actually no wheel spin occurring so these are sort of subtle little things that are important to make sure that you've got all of your I's dotted and your T's crossed. |
25:04 | It should go without saying with any ECU setup but it is really a case of garbage in garbage out so it's important to take the time, go through, tick all the boxes and make sure that you have got all of that information accurately programmed into the ECU in the first place. |
25:22 | Right so what we'll do is we'll go over our main control, what we've actually got control over and this actually starts with the system being enabled which again should go without saying. |
25:36 | We've got our traction mode here so probably when you're first getting started with a base package, that will be disabled so we're going to need to enable that otherwise you're not going to see all of the other settings that are available. |
25:48 | So I'm using a multi position switch and we'll just jump across and have a look at that. |
25:54 | So we've got 2 of those on our steering wheel here. |
25:59 | On the left is our traction control 0 through to 4 and on the right hand side is our boost. |
26:06 | The boost one also conttrols the drive by wire throttle target which we already looked at. |
26:12 | So I am a big fan of having the ability to manipulate the traction control on the fly. |
26:19 | The reason for this is track conditions change, driver preferences change and you might start a race which is dry and it starts pouring down with rain. |
26:29 | In this particular car I don't use traction control at all in the dry, car's really well hooked up and I have no problem with it when it is dry. |
26:39 | However in the wet, very different deal and traction control can be quite beneficial. |
26:44 | So being able to adjust that on the fly is really important. |
26:46 | Even once you've got the traction control set up, however for actual calibration and testing of the traction control strategy, getting some settings in there that work well and you're comfortable with, the ability to adjust the likes of your aim slip or your traction range which I'll talk about in a second, while you're actually out on the track without having to come back into the pits and jump on the laptop is really really powerful, it's going to get your setup done a lot quicker and a lot more efficiently. |
27:15 | Alright let's head back into our software again. |
27:18 | So driver traction switch index, bit of a mouthful. |
27:23 | We've got that on driver rotary switch one which is that switch on the left that I just showed you. |
27:28 | And then we can set up our mapping. |
27:30 | So this is important to understand as well. |
27:32 | So this defines whether the traction control strategy is on or off dependent on the position of that switch. |
27:40 | So default, so this is what happens if the switch maybe becomes faulty or goes outside of its range, it will go to default so in default, the traction control by default will be on. |
27:52 | Then in map position 0 we've got the traction control turned off and then we've got 1, 2, 3 and 4 so essentially we've got 5 positions for that switch. |
28:01 | And I've got it on in positions 1 through to 4. |
28:04 | You can, as you see here have up to 9 positions or actually 10 positions and 0 through to 9 is 10 and this is another area where my personal preference is, I think some of these multi position switches, 10 positions for the likes of traction control, I'm not a professional driver so I certainly don't need that fine level of adjustment and I think what we can get ourselves into a situation with as well when you're fine tuning something like this is you need to actually make a big enough step change so you can actually notice the difference. |
28:42 | So if we're talking about our traction aim slip target, I probably wouldn't notice the difference between 3 and 4% or maybe 5 and 6% slip so I probably if I'm getting started I might make a change of maybe 3 to 4%, maybe 3 to 5% per switch position so i can actually get a real feel for what that's done and know by the seat of the pants, by how the car's responding, whether that change that I've just made has been better or worse so that's why I've limited the number of positions that our switch is using here instead of the ability there to run all 10 of those positions. |
29:24 | Alright so coming down here we've got our traction aim switch so that's for our traction target, traction slip target so again that's from our driver rotary switch 1 and I'll talk about how I've done this. |
29:40 | We've also got the ability to have a driver switch for our range index which I'll talk about what that is, don't worry about these terms if you don't understand them. |
29:48 | So at the moment I've got basically everything is run off the driver rotary switch. |
29:53 | So top one there, we are defining whether the traction control system is physically on or off, whether it's functioning or not. |
29:59 | Then our aim is being controlled by the same rotary switch and then our range which defines essentially the range of RPM across which the traction control engine speed limit will work, all off the same rotary switch. |
30:13 | Of course you can have mutiple in there. |
30:16 | OK coming down, we've now got our traction aim main. |
30:20 | So how does this work? Pretty self explanatory, this is just our slip target and what I've generally done here, these numbers in here are actually from some testing that I was doing and they aren't very realistic. |
30:34 | I would probably have something more along the line of 12%, maybe 8%, 6% and then maybe 4% or something of that nature. |
30:45 | And what this does is basically in this case, position 1 would be our least aggressive traction control, we're allowing the most amount of wheel spin, in this case 12% wheel spin. |
31:00 | And of course traction control position 4, we're only targeting 4% so it's not going to allow very much wheel spin. |
31:05 | The specific numbers are going to be up to you. |
31:08 | Probably 4% is about as low as you'd want to go in my own experience just purely because as I've mentioned, you're always going to see some amount of wheel slip there. |
31:18 | So if you've got that set too low, it's going to be very over bearing and it's going to be doing a lot of work. |
31:24 | Of course you do need to be careful with your default setting as well and your setting in position 1 here, you don't want to have necessarily too much wheel spin and this will come down to the specifics of the vehicle an the specifics of the driver and how comfortable the driver is with that. |
31:44 | Alright so that's the main aim slip target table but there are a couple of modifiers for this so let's come down to our next one here which is our traction aim compensation vehicle acceleration lateral. |
31:59 | Again, but of a mouthful but what you do get to appreciate with the MoTeC M1 platform is that the channel names are very specific so you can really understand from that channel name, parameter name exactly what it's there for. |
32:14 | So what we can do here is essentially feed in a lateral G force or a G force sensor in general into the ECU, lateral of course, cornering. |
32:23 | And then we can adjust our, or compensate our slip target based on whether the car is in a straight line with no lateral G force or whether we're accelerating hard. |
32:34 | Now you can see I'm not using this and, maybe a personal preference, if we want to set this up, what we can do is enable the axes, so clicking on enable and you could basically set this up to be whatever you want in terms of the G force. |
32:50 | You can also add a second axis there to turn it into a 3D table based on vehicle speed. |
32:55 | So the premise behind this, what that's there, it's pretty self explanatory, wheel spin in a straight line the car's going to move around a little bit but it's probably not going to be very difficult to control when the traction control strategy actually does kick in. |
33:09 | However if you've got the car loaded up at maybe 0.8 to 1 G and the track's wet, or even if it's dry for that matter, and you get a little bit of wheel spin, essentially you're straight away going to have the rear of the car, assuming rear wheel drive of course, break away and start to slide so what that means is that when you've got some lateral G force occurring, the driver's actually still going to have to be reasonably quick if you've got a lot of lateral G force occurring, to catch that slide that's inevitably going to occur. |
33:37 | Even with the traction control coming in. |
33:40 | So personal preference as to whether or not you use that, does require the G sensor but if you're running something like we are with the MoTeC C125 dash that has a 3 axis G sensor built in and you can send the G sensor data between the C125 dash and the MoTeC M1 ECU via CAN so not very difficult, doesn't require an additional sensor. |
34:04 | The other compensation we have here, if we come down, is for our aim compensation for the current gear. |
34:12 | So again pretty self explanatory, 2D table here with our current gear. |
34:15 | Now the reason we might want to do this is that when we're looking at that slip it is a percentage base so again using the numbers that I had before, if we were at 100 km/h, 10% slip, that's a 10 km/h difference between our driven and undriven wheel speeds. |
34:33 | That's possibly fine at 100 km/h, if on the other hand we're doing 200 km/h, that's now 20 km/h so slip in some ways maybe isn't necessarily the best way of representing our traction control targets. |
34:50 | It's pretty generic, it's fairly widely used as a traction control input but it does bring in this problem with the amount of actual wheel spin we get at low speed is dramatically less than what we get at high speed. |
35:04 | So we've got the ability to compensate that based on our gear if we want to. |
35:09 | What I would recommend is just being a little bit careful though how you do this because these all add up. |
35:17 | So if you're in 5th gear, 4th gear and you've got a compensation there to reduce the amount of slip that is achievable, but you're also cornering and you're using your lateral acceleration compensation, both of those will be working on your main aim target slip and what you thought maybe was a perfectly reasonable slip target might start to get down to the point here just small natural differences in our wheel speeds can actually register enough slip to be hitting that traction control limit so what that feels like from the driver's seat is that the car is almost misfiring when we're driving it around the track, even when it is definitely still hooked up so that's something you do need to be mindful of there and it's always a good idea to be logging these parameters, which I'll talk about as we go through so that you can pick up if there is a problem like that, what's actually causing it. |
36:10 | Now we'll just come down as well to this next parameter here which is our traction activate vehicle speed. |
36:17 | So you can see I've got this set up to 20 km/h which is relatively low. |
36:21 | The reason that we need to consider this is the interaction between our launch control strategy if you're using that and your traction control so basically where do we want the launch control to sort of deactivate and the traction control to start coming in and picking up on the top? So I generally will allow the car to get off the line without the traction control coming in, I'll be using launch control for that and then once we're up and running, maybe from normally 40 or 50 km/h I might start bringing in the traction control, again very dependent on the specifics of your vehicle, gearing etc. |
36:56 | But that is a parameter you do need to understand. |
37:00 | Alright we'll get in now to a conversation around the way the MoTeC M1 does its limiting because what we've got here is this next parameter which on face value is not actually that obvious or easy to understand which is our traction engine speed limit fuel margin, again bit of a mouthful and you'll see I've got this set to -500 RPM. |
37:24 | So in MoTeC's engine speed limiting functionality, this is how the ECU defines whether it's using fuel cut, ignition cut, a combination of both and what range of RPM will be used so that between the margin and another parameter called range. |
37:44 | So I've stolen this next photo, I think it's stolen, no I can't get to that, let's try that. |
37:51 | There we go, stolen this next photo straight out of the MoTeC M1 help file so you will find this, it's a little bit tricky to find, it's under the initial setup 1 engine speed limits worksheet so I'll go and show you where to find it so you can have a look at this at your leisure. |
38:07 | But this is really what describes what's happening. |
38:09 | So first up here, if you have positive numbers for your fuel margin. |
38:16 | Then if we have an engine speed limit, regardless of what that engine speed limit may be, so in our case we're talking about traction control, so if our traction control engine speed limit and our fuel margin is let's say 200 RPM, what will happen is that right at the traction engine speed limit, so when that engine speed limit first becomes active, it will start by using ignition. |
38:41 | So we are starting our cut by using ignition. |
38:45 | The ignition cut range will be set by another parameter called ignition range. |
38:52 | So that's basically this section here and when we get above the traction control engine speed limit by the range RPM, at that point we will get a 100% ignition cut. |
39:08 | I know this is a little bit complex to get your head around but it is really important to understand it. |
39:14 | So let's say for example we've got our fuel margin set at 200 RPM so we're going to also have our ignition range set at let's say 100 RPM. |
39:26 | What would happen is that we would start, when we get to our traction engine speed limit, we would start with our ignition cut and then when we get 100 RPM above our traction engine speed limit, we would be at a 100% ignition cut. |
39:39 | Now the other part there though is our margin, so our fuel margin, I said that was 200 RPM. |
39:45 | So that actually defines this little bit in here. |
39:48 | This is again where it gets a little bit complex because we can have this interaction if we've got a potential to have full ignition cut with no fuel cut, we can have full fuel cut with no ignition cut which we'll look at next and then we can have an interaction where we have both fuel and ignition cut occurring sumultaneously. |
40:06 | In this case if we've got our engine speed fuel margin set at 200 RPM, the fuel cutting will not begin until we are 200 RPM above our traction engine speed limit or whatever our engine speed limit has come in for. |
40:22 | So you can see that by adjusting that margin and the range for our ignition cut, we basicallly can alter how these come in. |
40:30 | So in this particular example here, we can see whatever the numbers are, they don't really matter, we can see that our engine speed fuel margin there is less than our ignition range. |
40:44 | So the ignition cut, sorry the fuel cut will actually start coming in just before we get to a 100% ignition cut. |
40:53 | And then on top of that we have the exact same thing, we've got a range for our fuel as well. |
40:59 | So little bit complex, that's if our margin is greater than 0 so we're going to be beginning with ignition cut, or at a very minimum we will have ignition cut active. |
41:10 | Below that is what we get if our fuel margin is a negative number. |
41:17 | So if it is less than 0, what we're going to end up doing this time is switching things around and now when we get to our engine speed limit, we're actually going to start straight away with fuel cut and the ignition cut will not start occurring until we're at this point here which is defined by that fuel margin. |
41:38 | So let's say we have a number of -500 RPM. |
41:42 | What that would mean is that we're going to start with fuel cutting and the ignition cut will not come in until we are 500 RPM above that engine speed limit point. |
41:53 | Now by manipulating this along with the range, we can get to a situation where we can get the ignition cut out of the ballpark so that we are only working with fuel cut. |
42:03 | I know again it is a little bit complex but this is how MoTeC have chosen to do it. |
42:09 | Let's just head back across to the tuning software, we'll go to our initial setup and engine speed limits and I think if we press F1 here, yep there we go. |
42:20 | I just wanted to show you how you can find that yourself because it's not everywhere and there is exactly what I just showed you. |
42:28 | Alright so why is this important? The reason it's important is because the type of cutting we're using is very important to the reliability of your engine and we, if we look at, for example the SR20DE and DET are a classic for this. |
42:49 | We know that they have bad reliability with the rockers being not shaft mounted so what this means is that if we're using an ignition cut, particularly at high RPM and wide open throttle, on a turbocharged engine this can result in explosions taking place in the exhaust manifold because we've got unburned fuel and air from the cylinder that's just had the ignition cut occur, being passed through into the hot exhaust where it can combust so what that can do is create pressure spikes which then pops the exhaust valves back off the seat and that in turn can end up popping the rocker off and doing some quite serious damage. |
43:24 | Even with a shim style valve train like the Nissan SR20VE, ignition cutting can be enough to actually pop a shim off as well and we've had exactly that problem with our VE turbo engine so the safe bet is usually in most instances to focus on fuel cutting and stay away from ignition cutting unless you're very certain that you have a valve train that is not going to be adversely affected by ignition cut. |
43:52 | So really important to understand that and how it works. |
43:56 | Alright, I know I've talked a lot about the ignition cutting and the fuel cutting and how to set that up but it is sort of part and parcel of this setup so let's have a look at, now we have a better understanding, a look at how that works. |
44:09 | So we've got our fuel margin which we now hopefully understand, you can see I've got that set to -500 so from what I've just explained, what this means is that when we get to our traction engine speed limit, we will be functioning a fuel cut first. |
44:23 | The ignition cut will not come in until we are 500 RPM above our fuel cut starting point, our traction engine speed limit. |
44:34 | Now that is high enough in this instance that it should be basically pushed right out of the way and we should never have an instance where we're going to end up hitting that ignition cut which was my preference, that's what I was trying to achieve there. |
44:48 | Alright so the next thing we have is traction range. |
44:52 | Now this is a little bit of a peculiarity here, there is actually a misprint in the help file here for this particular package and depending on what package you're working with, you may actually have another parameter up here which will be fuel range, you may have ignition range in there as well. |
45:11 | In this case the traction range defines the range for both fuel and ignition but just to be a little bit more confusing, it is actually a percentage number as well. |
45:22 | So this essentially controls the RPM range above our traction engine speed limit, across which the fuel or the ignition cut or both will function. |
45:34 | So for example again, when we get to our traction engine speed limit, we're going to start with basically the very minimal amount of fuel cutting and let's say we're got a range of 50 or 60 RPM, as we get to that full range, 50 or 60 RPM above that calculated engine speed limit, we will be slowly moving to 100% cut so it's really important to have this tuned because if we have a number of 0 in there and essentially we're going straight to 100% cut, ell it's going to work, it will stop the wheel spin but what we're going to end up with is a very harsh traction control strategy that's definitely not going to make the car easy to drive or fast when the traction control is functioning so we need enough of a range so that the control is smooth but the flipside of this is if our range is too great, it's essentially almost extending the amount of slip that we can create because we're not getting that hard cut right at the traction control engine speed limit which is the slip target that we've got, we're going to be extending that a little bit further so it's just really important to understand the interaction between the slip aim and our range. |
46:47 | Alright let's move, we're going to move into questions really shortly, I'll just call for those questions now so that I can get to those and I'm just going to go over a testing strategy at least one that I've found works well for me because the obvious question here is what sort of numbers should we be putting in here and how should we go about testing and finding how well the system works? So again obviously everyone can have their own preferences on how to go about this, I'm just going to talk about from my own perspective what I've done with this car and our other 86. |
47:23 | First point is to make sure all of our inputs are correct and I can't stress this enough, if we don't have things like our diff ratio, our gear ratios, wheel circumference set correctly, we're going to be in a position where we're going to be on the back foot from the get go and the ECU is already going to be calculating some amount of wheel slip, it's just not going to be able to do the job properly so really important to make sure that that is all working. |
47:51 | A good sanity check for this is also looking at the logging from your 4 wheel speed sensors in a straight line where you know you've got no wheel spin and making sure that they are in fact matching each other. |
48:05 | You can also log the slip channel, so that's the generated slip channel based on wheel spin so you can see what that's actually doing and whether that seems realistic. |
48:15 | I would suggest, even if you don't intend to use a multi position switch in the car, it really does just speed up the testing because we're going to want to test for multiple slip aim values and we're also going to want to test for multiple range values to get an idea of what actually works best for your car and your preferences. |
48:37 | So again, you can take that switch out of the car but it will speed up because you don't have to come back to the pits and consistently grab the laptop and make changes to those targets. |
48:47 | So let's go back to our aim main. |
48:50 | So for values in this table, I would suggest that you're probably going to end up wanting to be in the region of maybe 5-10%, maybe 4-10%. |
48:59 | So that's a rough guide that should at least get you into the ballpark and you can fine tune from there. |
49:07 | To reiterate, probably you want to make sure that if you are using that multi position switch that you are making a significant enough change in the slip aim to actually be able to feel or understand what that affect has been. |
49:22 | However as I've also mentioned, our traction range is also going to affect this and this is where I've got another tip for you as well. |
49:30 | So again I went through this with MoTeC just recently and they'd suggested that probably somewhere in the range of 10-15% for the range is a good place to start. |
49:40 | Found that that was actually pretty close, I think we ended up at 15% if not 20 but again just having the ability to change these on the fly here and again I've made changes of 5% just so that they're big enough so I can physically feel them. |
49:55 | However this is where these two do interact with each other. |
50:00 | So while you're starting and you are going to want to start most likely by setting up this range value, I would suggest that if you are using the same switch for both as I am, what I would do is come back and initially set all of your traction aim values, your slip values to the same value. |
50:22 | So let's say 6%. |
50:25 | So what that means is that you're not going to be confusing yourself by changing both the slip aim and the range at the same time. |
50:32 | So you're always going to be targeting 6% slip and then what you'll be able to do is see OK I change from 10-15, 15-20% for my range, how's that actually made the car control when it is sideways, when it's wheel spinning and how smooth is it and that's what you're going to be wanting to look at. |
50:53 | Really important for this as well to make sure that you are using the logging to actually see what's happening. |
51:01 | Again I mentioned logging the wheel speeds, you can also log the traction aim engine speed limit so you can actually see what that's doing. |
51:11 | You can log basically all of the parameters to do with slip and the traction control strategy and see what exactly is going on. |
51:19 | I always like to log both the ignition cut count and the fuel cut count so I can see what those have been doing in the log file and a nice feature of the cut count is that it doesn't really matter what your logging rate is, you're not going to miss a single cut. |
51:38 | Let's just go back into the screenshot of that. |
51:46 | So we actually had that down here, so this is the ignition cut count. |
51:50 | So basically this number is just a counter that will increment between 0 and 255 and then it will reset and go back to 0 and start counting up again. |
51:59 | So you can get a problem where if you've just got maybe 1 cut event occurring, depending on your logging rate for your ignition cut or your fuel cut, it can actually be possible to miss that in a log file. |
52:13 | Even if you're logging at a reasonably high rate, maybe 50 Hz, you can potentially miss one cut event, if you're looking at that cut count, doesn't matter what your logging rate is, you're not going to miss it because even if you're down at 2 or 5 Hz and a cut occurs between logging samples, it's going to have incremented that cut counter so it's a really good way of making sure that you never miss a cut and even irrespective of traction control in general, this is a really good way of kind of focusing on or figuring out what's actually happening. |
52:44 | If you've got a weird cut occurring that you're not quite sure what's going on and you can also look at what the cut is being brought in for, looking at the state there as well. |
52:55 | Alright so once you've got this set up, obviously the next step is to head out onto the road or the racetrack and actually do some testing and see how it's working and what your preferences are. |
53:09 | I find it's easiest to start with of course if the track, the surface is wet because it's going to be easier to induce wheel spin but we also may want, with powerful cars, to be able to test this in the dry as well so really just dependent on your car and your setup, but it is going to take a little bit of testing to find what works and that's why I again like that multi position switch because as you get more comfortable with the car, as the track evolves, as the tyre conditions changes, you may find that what worked well at the start of the race may not be ultimate once you're 6 or 8 laps into it and I find exactly this with our endurance series races. |
53:50 | These are rolling starts, it's very difficult I find to get the tyres really up to temperature on the formation lap and generally for the first 1 or 2 laps I'll run a little bit of traction control just in case I do have some breakaway wheel spin there until I do get the tyres up to temperature and then I will basically disable the traction control assuming that the track is dry. |
54:15 | Alright we'll move into our questions now so if you've got any more, please keep them coming. |
54:22 | Wedge has asked, any suggestions for implementing traction control on a FWD rally car? Noting that we often left foot brake and intentionally spin the front wheels and lock the rears, we'd be fighting against the traction control system in that case. |
54:35 | Yeah I think you're going to have a lot of problems with that situation. |
54:40 | Particularly with rally as well, when you're on a loose surface like gravel, wheel spin sometimes can be actually beneficial well and above the slip ranges that I was talking about because often on gravel for example that can actually allow the tyre, particularly a specific rally tyre to get down through that gravel and actually grip what's below. |
55:00 | So traction control, in the driver's that I've dealt with in rally, I've never seen it used. |
55:07 | I can't say that's the case across the board but particularly when you are left foot braking and you're inducing wheel spin, the situation is quite different. |
55:17 | Would be easy enough to have a traction control disable when the handbrake is used, that wouldn't be too difficult because obviously under those conditions you're straight away going to see massive slip values that aren't entirely real because obviously you've purposefully locked the rears. |
55:34 | So you could use something like a driver switch there to simply disable the traction control system when the handbrake is active. |
55:43 | Zansteatt has asked, what about boost limiting to control power output? Well I've talked about that as we went through, 100% I definitely would suggest doing so. |
55:52 | Again it's a case of trying to dial in the torque that the engine delivers in order to basically match the torque to the amount of traction that the car has available so then the traction control's not going to be working too hard. |
56:08 | F1hotrod's asked, do any aftermarket ECU's use throttle to cut power in traction control? Not to the best of my knowledge. |
56:15 | I can't speak for every ECU but I haven't seen it. |
56:19 | I actually tried it in a development package on our other can and I didn't find it particularly effective, it was quite hard to get it to work smoothly. |
56:31 | Obviously lifting off the throttle was a really good way of getting grip back but it also has a dramatic effect on the engine torque which if you're kind of on the limit can end up being upsetting to the car balance in itself so I didn't personally find it very effective. |
56:48 | Suhas has asked, is there any way to implement traction control without wheel speed sensors? Is there another parameter other than wheel speed as an input to traction control? Whats the difference between them, I mean disadvantages/advantages? Well I mean realistically you are going to need some way of knowing if you've got slip so wheel speed really is the fundamental way of doing that. |
57:08 | There are other strategies where you could use GPS based speed. |
57:15 | That needs to be treated carefully, most of the mainstream enthusiast level GPS sensors are only 10 Hz which simply isn't fast enough to be effective for traction control. |
57:25 | There are some now that work at 50 Hz which I know a lot of people have been using for traction control, how effective it is I can't say because I haven't used it myself. |
57:35 | If you look at other options for the likes of drag racing, monitoring the driveshaft speed versus time is quite common there. |
57:46 | And basically they're profiling that driveshaft speed to what they consider should be the driveshaft speed on a perfect run. |
57:55 | And basically if the wheel speed, sorry if the driveshaft speed exceeds that profile, what that suggests is that the car has broken into wheel spin. |
58:04 | Bryguy's asked, without a lateral g-sensor, is there a need to average the undriven wheel speed across the front or rear etc? So this is getting a little bit too deep but I believe that the MoTeC will do that in terms of giving an average. |
58:24 | So obviously if you're turning, you're going to have a difference in wheel speed for the inside of the corner versus the outside of the corner so what we're looking at there or what should be looking at there is the average undriven wheel speed and the average driven wheel speed and the slip is based off that. |
58:43 | So you also need to take into account there, things get a little bit tricky when you've got something like an open diff versus an LSD. |
58:50 | With an open diff you could end up creating large amounts of wheel spin on the inside wheel but if you're looking at that average, still does take that into account. |
58:59 | Chuck has asked, when dealing with launch and transitioning from launch limit to traction control limit I find it’s easier to use traction control instead of launch as launch will also control timing by retarding it and causing the engine to have less power. |
59:11 | OK I think this is one of those cases where there's no black and white answer as to how you must do it and it also comes down to what you're trying to control in terms of your launch control strategy. |
59:26 | For us with a drive by wire throttle body, I'm using drive by wire throttle position versus wheel speed. |
59:33 | So that's very effective to get the car hooked up. |
59:35 | If you are simply using it as a launch RPM limiter, then maybe that's not going to be quite so effective so I think it's a little difficult to say there's a black and white answer that this is how you must use it. |
59:49 | You are right though with the M1 the ignition retard is quite aggressive. |
59:55 | I actually got around that because I didn't want a lot of ignition cutting and ignition retard there with our engine but again a lot of that comes down to your settings. |
01:00:07 | There is a webinar in the archive on launch control which you can check out if you want to learn a little bit more and we've also got our launch control tuning course where we have a worked example on the M1 platform. |
01:00:24 | Got another question from F1 hotrod. |
01:00:27 | Is there a way to use G force data as an input for traction control? Yes potentially. |
01:00:34 | I have definitely never tried doing this but obviously when we get wheel spin, we're going to see a dip in our G force, our longitudinal acceleration is going to be reduced because the wheels aren't hooked up. |
01:00:48 | So we could potentially implement that as a method of traction control. |
01:00:54 | It would require a lot of work around it because obviously the longitudinal acceleration is going to also be factored in based on the current gear that we're in, we're going to obviously accelerate faster in second gear compared to 4th, 5th and 6th gear. |
01:01:10 | So there'd be, I would imagine quite a few complexities in getting that system to work but it could be possible, definitely there is a correlation between wheel slip and longitudinal G force but there's probably simpler ways of really defining that wheel slip which we've talked about. |
01:01:30 | Alright that brings us to the end of our lesson, remember if you do have questions, if you're watching this in the archive, please ask those on the forum and I'll be happy to answer them there, thanks for joining us. |
01:01:41 | Now for those who are watching today on our YouTube channel or Facebook, this is just an insight into what we put on every couple of weeks for our HPA gold members. |
01:01:50 | Our gold members get to review these webinars in our archive where we've got around 300 hours of existing webinar content. |
01:01:57 | It is an absolute gold mine of information, one of the fastest ways to expand your knowledge on a huge range of tuning, engine building or wiring, car setup and driver education topics. |
01:02:08 | Gold members also get access to our private member's only forum which is the best place to get reliable and trustworthy answers to your specific questions. |
01:02:15 | You can purchase gold membership for just $19 USD a month but you will get 3 months of free gold membership with the purchase of any of our course. |
01:02:24 | You can find our entire course database at hpacademy.com/courses. |
01:02:31 | Alright thanks again for watching and we'll see you all next time, cheers. |
Timestamps
0:00 - Introduction
1:25 - How it works
4:06 - Why do we want it?
6:11 - Not all created equal
8:03 - Grip vs slip
10:00 - Should be considered a safety backstop
13:14 - Torque management
17:45 - Traction control in the M1
25:21 - Main control
37:00 - Engine speed limiting
46:55 - Testing strategy
54:23- Questions
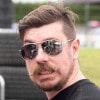