161 | Understanding Pilot Pulse - Diesel Tuning
Summary
One of the common complaints when it comes to diesel engines is the noise generated by the compression ignition process. The result is a knocking sound that’s particularly audible at idle. In this webinar we’ll see how modern CRDI engines have largely eliminated this noise by virtue of pilot injection pulses. We’ll discuss the concept of pilot injection and then see first hand the effect it can have on engine noise.
More diesel tuning information can be found in the Diesel Tuning Fundamentals course.
00:00 | - It's Andre from the High Performance Academy, welcome along to this webinar where we're going to be talking about pilot pulse injection on common rail diesel engines. |
00:10 | We're seeing a huge improvement in the technology behind diesel engines over the last few decades. |
00:16 | And certainly with the advent of common rail diesel injection where we're talking about incredibly high fuel pressures and the incorporation of electronic control over the diesel injection strategy, we've seen some huge improvements in both the efficiency and operation of the engines. |
00:33 | We've also seen obviously some of the latest crop of turbo diesel engines produce fairly impressive levels of both power and torque. |
00:43 | We've also seen one of the long term advantages with diesel engines has always been their impressive fuel consumption figures. |
00:52 | However some of the downsides of diesel engines which have prevented or limited maybe their adoption in mainstream passenger vehicles is the fact that diesel engines do produce quite high noise levels. |
01:05 | In particular here I'm talking about the knocking sound that we'll often hear from diesel engines, very noticeable particularly at idle. |
01:13 | And also the emissions from diesel engines can be problematic. |
01:18 | So in particular, and this is really the focus of today's webinar, a technique or a means of reducing that diesel knock was required in order to make them more appealing to the mainstream user and see the more widespread adoption of diesel engine technology. |
01:36 | Now as usual with this webinar at the end of the webinar, we will be having a section for questions and answers so if you've got anything to do with diesel pilot injection or anything that I talk about during today's webinar that you'd like me to explain in more detail, please ask those in the comments or in the chat and the guys will transfer those through to me, we'll deal with those at the end of the webinar. |
01:56 | Also want to just say thanks to the guys at Motec in Australia, we are using a couple of the slides from some of their own diesel training to help with today's webinar. |
02:08 | This webinar also runs on the back of our introduction to diesel webinar which we ran recently. |
02:14 | If you are interested in learning a little bit more about diesel tuning, please check that one out in our archive too. |
02:22 | OK so it's important to start at the start, we're going to look at the diesel combustion process, so we can jump across to my laptop screen. |
02:31 | And for a start it's important to understand that during the intake stroke of the diesel engine and the compression stroke, we only have air in the cylinder. |
02:39 | When the air inside the cylinder is compressed, it becomes super heated. |
02:45 | And somewhere near the top of the stroke, somewhere near to top dead centre, the diesel fuel is then injected. |
02:50 | So that's what we've got going on here. |
02:53 | So our diesel is injected directly into the combustion chamber via the injector fitted into the cylinder, into the cylinder head, and as that diesel is injected it becomes super heated by the compressed air that's in the cylinder. |
03:09 | Once the fuel becomes super heated, some of it will reach its ignition point, and it will begin the combustion process, it will actually begin burning. |
03:18 | So the important takeaway from this is, from the point that our diesel is injected, we have an ignition delay as it's referred to, so there is some amount of time, some finite amount of time it takes before our diesel will actually begin burning. |
03:33 | Once we get to a point where our diesel begins to burn, it will burn very very quickly, much faster than a petrol engine. |
03:42 | What we essentially get is each of the diesel molecules produces its own flame front and it consumes all of the oxygen around it. |
03:49 | So we end up with multiple flame fronts and we end up with a very fast combustion process. |
03:56 | And this is part of the problem that we end up with with a diesel engine because we get that very fast combustion process, what it results in is a lot of noise happening as the pressure spikes very quickly inside the cylinder. |
04:14 | So if we can again jump across to my laptop screen, this is what the pressure inside the cylinder essentially looks like. |
04:22 | So we've got our black line here which is essentially what the pressure inside the cylinder will do with no diesel injection, with no combustion, so naturally as the piston rises towards TDC, the pressure increases because the air trapped inside the cylinder is being compressed, as it moves away obviously that pressure reduces again. |
04:41 | So we've got our injection event being displayed here. |
04:44 | So in this case for this particular little example here, we've got an injection event that's 0.8 milliseconds long, and you can see that there is a delay to combustion, our ignition delay there of 0.5 milliseconds. |
04:59 | Because the combustion happens very quickly when it does initiate, what we see here, is we've got this very very sharp rise in our pressure, and it's this sharp rise in the pressure just before we get to TDC that causes that knocking. |
05:13 | That's the audible knocking that we can hear. |
05:17 | OK so that's the principle very roughly behind diesel injection, diesel combustion, and this is why we have that knocking noise that occurs. |
05:30 | It's also important to understand that diesel injectors, common rail diesel injectors, also exhibit very similar aspects to our normal gasoline injectors and that is the fact that there is some latency involved with their operation. |
05:47 | Now I will, I'll just go across to my laptop screen, I will apologise in advance for the shocking quality of this photo, but I only hope that I can get the idea across to you. |
05:59 | So what we're looking at here is two plots. |
06:01 | At the top we've got the current being supplied to the injector from the ECU or injector drive. |
06:06 | So we see our current rise, it peaks and then it drops away, so the current that the ECU is providing, versus directly below this we've got our actual fuel injection. |
06:19 | So what we can see is that there is a delay in both the opening time and closing time of the injector. |
06:25 | So again very similar to what we'd see with a petrol injector, a gasoline injector, but it's important not to overlook that this is a very real effect. |
06:34 | So there's going to be a delay in the signal being sent to the injector, from that time until the injector actually opens and starts flowing fuel. |
06:43 | And likewise when the ECU signals the injector to close, it will take a finite amount of time for the injector to close. |
06:50 | Now this is all quite critical with a diesel engine because we are very closely or very accurately trying to control the injection event. |
06:59 | So we've seen what happens there with a single injection pulse and because of the advances that we've seen with common rail diesel engines, the ability to run exceptionally high fuel pressure, this also means that now it's possible to run multiple injection events per engine cycle. |
07:18 | So instead of one single injection pulse where all of the fuel is delivered, it's now possible to split that up and it's quite common to see diesel engines running three or even four injection events per engine cycle. |
07:31 | And these are broken up into pilot pulses, which is what we're going to be talking about today, and then quite often we'll also run a post pulse or an after pulse that happens during the power stroke at some point. |
07:46 | OK so what we want to do is understand what's actually happening when the combustion process takes place. |
07:56 | And in order to do that we'll just jump across to my laptop screen and again we're gonna have a look at what is unfortunately a shocking quality image here but hopefully again this is going to be enough to explain what's going on. |
08:10 | So we've got two points labelled here. |
08:12 | We've got SOI which stands for start of injection, and we've got EOI which stands for end of injection. |
08:18 | So this section here that I've just highlighted in red, let's just do a better job of that. |
08:27 | From this point here to this point here, this is when our injector is actually open and injecting fuel. |
08:35 | OK so what we end up with straight away is an ignition delay which is this point here. |
08:41 | So we get a delay which is where you'll remember, this is where the fuel is becoming heated by the air, the compressed air inside the cylinder. |
08:49 | After that we see we've got this large spike in our heat release which also coincides with a spike in our pressure. |
08:57 | And this point here is what is the cause of our diesel knock and this is referred to as the premixed combustion phase. |
09:07 | I'm going to explain each of these terms in a second individually, I just wanna get an overview of them for a start. |
09:13 | Once we go through that we see our pressure drops back down and our rate of heat release drops back down and then we get a slightly slower and more consistent rise and drop away in our rate of heat release. |
09:26 | And this is referred to as our mixing controlled combustion phase so this is a much slower combustion process. |
09:35 | And then following that we have a last stage of our combustion which is known as late combustion phase. |
09:41 | So I just wanna talk about each of those individually. |
09:45 | So first of all we need to understand what's actually happening during our ignition delay period. |
09:50 | So remember this is the delay between the fuel initially being injected by our injector and the start of that combustion process. |
09:58 | So during this point we've got the atomisation of the actual jet of fuel entering the cylinder. |
10:04 | After this, once the fuel enters the cylinder, it goes through a stage where it vaporises. |
10:08 | And then that vaporised fuel starts to mix with the surrounding air. |
10:14 | So the ignition delay period will vary from one engine to another depending on a number of factors to do with the engine's mechanical design. |
10:24 | However a typical delay might be somewhere in the order of about 0.4 through to one millisecond. |
10:29 | So again if we can just refer to our screen here, my laptop screen. |
10:34 | So that section that we're just talking about here is our ignition delay. |
10:38 | So this is prior to any combustion taking place. |
10:42 | Following that we move into our premixed combustion phase. |
10:45 | So this is the initial combustion of that premixed fuel and air. |
10:51 | So this is the vaporised fuel and air that has occurred during the ignition delay period. |
10:58 | So that vaporised fuel starts to mix with the air. |
11:01 | It's characterised by a very fast heat release which is what we can see here by our vertical climb on our graph here. |
11:09 | Hopefully you'll be able to see that anyway. |
11:11 | And this also incorporates very fast combustion. |
11:14 | It happens within just a few degrees of crankshaft rotation and this also as I've mentioned results in a very sharp rise in our pressure. |
11:24 | We've already seen that on our previous slide. |
11:26 | And this is what results in the knocking sound from our diesel engine. |
11:32 | This occurs obviously if the mass of fuel is sufficient to result in the pressure rise being enough to actually create that knocking effect. |
11:42 | So once we move on from our premixed combustion phase we move into our mixing controlled combustion phase which we've already looked at. |
11:50 | During this phase our burning rate is controlled by the rate at which the mixture is made available. |
11:57 | Remembering if we again refer to our graph here, we're seeing that our end of injection event is still continuing through this process. |
12:11 | So the speed of burn during this part of the combustion process is mainly controlled by the mixing process of the fuel vapour and the air inside the cylinder. |
12:21 | Lastly and probably less important to us, the late phase combustion, so the heat release that we're seeing here will continue into the power stroke. |
12:33 | There's a couple of reasons for that. |
12:35 | Some of the fuel being injected may not have combusted, and we also see some of the energy contained in the soot and also some fuel rich deposits can be released during this time. |
12:46 | So that's essentially what's happening inside the combustion chamber during the combustion process with a diesel engine. |
12:54 | And it's that premixed combustion phase that's probablematic for us, this is what creates noise. |
13:00 | To a lesser degree, we'll talk about it in a little bit more detail, this also creates, this is the time when a lot of the oxides of nitrogen that are present in the exhaust emissions will be formed as well. |
13:12 | OK so let's just get another slide up here. |
13:17 | If we can jump across to my laptop screen now. |
13:21 | So the way we can help reduce this diesel knock is to use pilot injection. |
13:26 | So again this is something that's been used in OE applications now for a long time. |
13:31 | And what we're doing with pilot injection is we are bringing in one or potentially two pilot injection events prior to our main injection event. |
13:39 | So here we've got our main injection event. |
13:42 | Looks like we've got that starting around about 10 degrees before top dead centre. |
13:47 | And in this case what we're doing is we're bringing in a secondary event, our pilot event here, and we're bringing that in about 23, maybe 24 degrees before top dead centre. |
13:59 | So injecting fuel prior to the main pulse has the effect of increasing the pressure and heat inside the combustion chamber prior to our main injection event and the advantage of this is that it reduces the ignition delay when we have our main pulse occur. |
14:18 | So again just looking at our slide here we can see that after our pilot injection event, we've again got our ignition delay and we see that the pressure inside the cylinder increases and what we can see here in our slide is that instead of the sharp rise in pressure that we saw without our pilot event, we see that that rise in pressure is now smoothed out, it's much more gradual, and because we're reducing that sharp rise in pressure, this helps eliminate the knocking sound that we get. |
14:52 | So it's all about reducing the ignition delay for our main injection event and hence reducing that premixed combustion phase. |
15:00 | This is the key to the way the pilot injection event helps us out. |
15:06 | So as I've said as well, because we see primarily a lot of the oxides of nitrogen being formed during that premixed combustion phase, anything we can do to reduce the timeframe for our ignition delay, that will help reduce the oxides of nitrogen being formed. |
15:30 | It's not all a free lunch though in terms of emissions. |
15:34 | What we do find is that pilot injection does increase soot formation in the exhaust gas. |
15:41 | So it's likely that we may find our engine smokes when we are using pilot injection. |
15:49 | So in the OE applications we find that this is dealt with with diesel particle filters and also after injection can also help to reduce those soot emissions. |
16:02 | OK so we're going to move into questions and answers shortly but we're going to go through a quick practical demonstration. |
16:10 | Before I go into this practical demonstration I want to add that this is a complex operation that we're trying to optimise here and without the benefit of in cylinder pressure detection as well as proper emissions monitoring techniques and an opacity meter to see what our smoke output is, it's very difficult for us in the aftermarket to be able to truely say when we've got this optimised. |
16:39 | So I know a lot of you out there are probably thinking to yourself right now well how on earth do we go about tuning this and it's a fairly valid question. |
16:47 | The aim of this webinar is simply to introduce the pilot pulse technology and explain to you what it is, why it works, and essentially how it works. |
16:58 | In most instances you're going to be able to rely on your OE mapping strategy because you're going to, most often people who are going to be tuning diesel engines, common rail diesel engines, will be using a reflashing package that allows you to optimise or adjust the factory calibration aspect. |
17:20 | So in a lot of instances you're going to be able to rely on leaving the OE calibration for the pilot pulse injection as it is and it's probably going to work absolutely perfectly for your application. |
17:34 | With our demonstration today we're going to be demonstrating this on a Motec M150 standalone ECU. |
17:40 | So this obviously gives us a little bit more flexibility or in fact a lot of flexibility in that we may have no starting point for a map. |
17:49 | Fortunately Motec, for the engines that they support, are providing startup maps that are going to be enough to get you up and running and get you close, but it's going to be a perfect way today of demonstrating the techniques of tuning because we'll be able to instantly see the effects of the changes that I'm gong to make. |
18:07 | The other thing before we move into this demonstration that I just want to mention, is that often the OE manufacturers are working to a very different set of guidelines to what we are. |
18:19 | When you're working in the OE world, emissions are really king, and that comes before everything else. |
18:27 | So obviously depends what part of the world you're working in and what sort of tuning you're doing, but often we may be able to make our tuning changes based more along the lines of fuel economy, torque and power output, and sacrifice some of the emissions. |
18:44 | Of course if your engine still needs to be emissions compliant, that's not going to be the case. |
18:49 | So it's going to really depend on exactly what you're doing. |
18:52 | Alright so what we're going to do is jump in and do a practical demonstration. |
18:57 | Let's start by just jumping into our laptop software, and I just want to give you a quick look at what we're going to be changing here. |
19:05 | So on our Motec M150 here, we are on the first pilot worksheet. |
19:12 | In this case we can use a second pilot and also post fuel, we're only going to be concentrating on our first pilot for our demonstration today. |
19:20 | And the two tables that we're going to be working on include our fuel mass pilot one nominal. |
19:27 | So this simply defines the mass of fuel that's going to be delivered through our first pilot pulse. |
19:32 | And then also our fuel timing for our primary pilot one. |
19:37 | OK so the way this work is that the ECU is already calculating based on some separate tables that we won't look at today, the total mass of fuel that's going to be delivered for a given combination of engine RPM and throttle position for example. |
19:52 | Also affected by our boost pressure. |
19:54 | So basically we're looking at a mass of fuel versus a mass of air that the ECU is calculating is going to be injected. |
20:02 | And then it's possible to further break that total mass of fuel up based on our pilot pulse. |
20:09 | So if for example we are requesting 20 milligrams of fuel total being provided, we can then in our fuel mass pilot one table, we can request two milligrams, and what that will do is take our 20 milligram total fuel delivery, two milligrams will be delivered via our pilot pulse and the other 18 milligrams is going to be delivered via our main pulse. |
20:36 | So the total has not changed, it's just how the total mass of fuel is split up amongst the different pulses. |
20:45 | OK so what I'm going to do now is I'm just going to highlight in our table here the area that we're idling at and I'm just going to reduce our pilot pulse, I'm just going to set that to zero, and you'll be able to hear, I'll stop talking in a second, you'll be able to hear the typical rattle or knocking that you'll hear from a diesel engine. |
21:06 | OK so that's a pretty typical sound from an old generation diesel engine and this is the exact problem why diesel engines were struggling a little bit for mass adoption. |
21:19 | So this is that sharp pressure spike caused by that premixed combustion phase that we've already talked about. |
21:26 | So what I'm going to do now is I'm going to add back in one milligram to those cells that we are currently operating in and as I press return I want you to hear the difference in the engine though. |
21:36 | As I press enter this change will be locked in and we'll see the pilot pulse now add that fuel. |
21:45 | So hopefully at home you'll be able to hear that, it really is night and day just simply adding in that pilot pulse, we see a really dramatic effect on the noise that the engine is producing. |
21:57 | In our time graph over here on the right, let's just full screen that and I'll pause it. |
22:02 | We also have the ability to monitor exactly what's going on and any particular point. |
22:09 | In particular here at idle we've got 800 RPM on board. |
22:12 | We've got our fuel mass main. |
22:15 | In this case we are delivering or requesting 2.8 milligrams of fuel, and you can see at this particular point we've got zero being provided by our pilot pulse. |
22:27 | And we can just come back over here, you can see that at this point, this is where we had our pilot pulse active. |
22:34 | The purple line on our group of data below this, indicates our pilot pulse pulse width, and we can see that our pilot pulse now is providing 0.5 milligrams of fuel and we're providing 0.6 milligrams through our fuel main. |
22:52 | So that actual total fuel mass hasn't changed, it's just the distribution, the way that fuel is apportioned has changed. |
23:00 | OK so what we'll do now is we're going to have another look at a couple of tests here. |
23:04 | And again just basically this comes down to our requirements or our aims in the aftermarket may not match the OE manufacturer. |
23:13 | So what I'm going to do is get us up and running here at 2000 RPM and we're going to have a look at the fuel delivery for our pilot pulse, and we're also going to have a look at our fuel injection timing. |
23:28 | So what we'll do is we'll just come up to 2000 RPM. |
23:34 | Now obviously at this point you're not going to be able to hear over our dyno, the effect of the pilot pulse tuning. |
23:42 | But what I want to do is show you anyway. |
23:44 | So at this point here in our table we've one milligram of fuel being delivered via our pilot pulse. |
23:50 | And you can see that we've also got an injection angle for our pilot pulse of 15 degrees. |
23:56 | So what we could do is go ahead and see how both of these factors affect our torque. |
24:02 | So what I'm going to do is I'm going to maintain a consistent or relatively consistent mass of fuel being delivered, in this case I'll just try and target 40 milligrams of total fuel. |
24:12 | Just using my throttle to adjust that. |
24:14 | And what we wanna do is have a look at the torque on our Mainline dyno here. |
24:19 | So you can see it's moving around a little bit but we're around about 180 maybe 190 newton metres. |
24:27 | So for our first change here, what I'll do is just so we've got no danger of interpolation just gonna highlight all of those cells there. |
24:35 | Let's just disable our pilot pulse entirely. |
24:38 | And we straight away see that we've just dropped a massive amount of torque. |
24:43 | So let's see by increasing our pilot pulse, we'll go in 0.5 milligram steps. |
24:50 | So with 0.5 milligrams we've gone from 100 newton metres to 170, we'll go back to one. |
24:57 | See we've gone up to 180. |
24:59 | We'll go to 1.5 And we'll go to two, as we go to two we see that our torque actually drops away. |
25:07 | So somewhere in the region of about one milligram which was the mass of fuel we actually started with there obviously seems to be a pretty good place for our pilot pulse at 2000 RPM with 40 milligrams of total fuel. |
25:23 | Now of course I'm just doing relatively broad changes there, we have the ability to make smaller changes of 0.1 milligram. |
25:31 | But we can see if we're not worried about emissions and smoke output, we can see the effect of that pilot pulse. |
25:37 | Let's jump down now, we'll do exactly the same here with our injection timing. |
25:43 | So what we'll do is we'll start here by reducing this to 10 degrees. |
25:49 | Again I'm just highlighting all of those cells so that we have no effect of interpolation. |
25:56 | OK so again we see that our torque plummets, we're down at about 107, 110 newton metres. |
26:03 | We also do need to be a little bit wary that there does need to be a sufficient gap between our main pulse and our pilot pulse as well. |
26:11 | So if we try and run our pilot pulse too close to our main pulse, we find that the engine doesn't run particularly happily. |
26:18 | So what we'll do now is we'll increase that to 12.5 degrees. |
26:24 | And we've seen very little change there, let's try 15 degrees. |
26:29 | Jumped back up to our 180, 185 newton metres, no big surprise, that's where we were. |
26:34 | We'll try 20 degrees now. |
26:37 | And again we see that our torque plummets. |
26:40 | So unsurprisingly with our test there, the values that we had in our table were very close to optimal. |
26:48 | Of course in some instances that may not be the case. |
26:52 | But the aim of this little experiment, this little test, was simply to show you the effect of that pilot pulse. |
26:59 | And if you are reflashing a factory ECU, and you're not in a position where you need to be emissions compliant, it is something that it is worth having some adjustments on and seeing what the effect is on your particular application and seeing if you can get any improvement from it. |
27:18 | Of course if you are working with an OE ECU and you're reflashing it, as I've said during the body of the webinar, you're already ahead of the game because you're going to have a fully developed table for your pilot pulse injection, so you don't have to develop this from scratch. |
27:33 | Alright we'll jump into some questions, and if you do have any more, please ask them in the chat or in the comments. |
27:44 | And I'll do my best to answer them. |
27:46 | OK first question comes from D Martin who's asked, I know in the previous webinar I mentioned the main injection being too advanced would cause piston cracking, would the pilot do the same to the piston or not because of the amount of fuel injected at the pilot compared to the main injection? Yeah I know exactly what you're saying, this was the problem that I did mention in our introduction to diesel tuning webinar. |
28:07 | And if you do advance your main injection event too far then yes you do risk doing damage. |
28:13 | But in this case the pilot pulse, because we are providing such a small mass of fuel, we're not going to have the same sort of problems as we would if we advanced our main injection point to the same sort of level. |
28:29 | So it's all about the mass of fuel and how small that pilot pulse is relative to our main pulse. |
28:35 | And really it comes down to the heat being produced in the cylinder and the pressure inside the cylinder. |
28:42 | Cypher Monk and Nick Brenner have both asked similar questions here. |
28:46 | Other than reducing the knocking noise and making for a smoother ramp in cylinder pressure, is there a power or torque benefit to the pilot pulse? Really hoping that you guys both asked that question before I just did that demonstration, so as we can see, yes there is an effect. |
29:00 | Certainly if you are comparing a calibration where there is no pilot pulse active at all, there's quite a significant difference of bringing that pilot pulse in. |
29:11 | Again my little test that I've just done there is a little bit unfair because we are dealing with a standalone aftermarket ECU. |
29:17 | Currently in the common rail diesel world, that's certainly very very rare. |
29:21 | And you won't find an OE calibration on a late model common rail diesel engine that isn't using pilot pulse injection. |
29:29 | So you're not going to get that night and day difference by applying a pilot pulse that wasn't there in the OE calibration. |
29:35 | D Martin's also asked, is there a general rule of thumb for the amount of fuel injected to pilot versus the main? Say example 5% of the main injection. |
29:44 | Right now, I'll be completely honest, we haven't got a rule of thumb that we can apply here. |
29:48 | You need to understand that right now we are also very early in our diesel tuning knowledge and experience. |
29:56 | So we are developing our diesel tuning course right now. |
30:00 | And hopefully we'll be able to give you a lot more input and guidance on that. |
30:05 | What we've just seen though with the demonstration that I've done is the dyno can guide you on the sort of results. |
30:12 | And with the pilot pulse injection in particular, you're not going to see an improvement in power and torque by using a lot more fuel. |
30:21 | And as we just saw in that demonstration, we started with zero. |
30:25 | We saw as I brought up the injection pulse to one milligram, we saw the torque increase quite dramatically and as I actually continued to increase it we saw the torque drop away. |
30:36 | So again you can use the dyno to help guide you there. |
30:41 | Terry has asked, does a knock event in a diesel engine damage parts the same way as it does in a petrol engine? Essentially in a round about way we could really describe the diesel engine as constantly suffering from knock. |
30:54 | It's not the same as a petrol engine. |
30:56 | But this is the way the combustion process occurs. |
31:00 | In a diesel engine we are getting spontaneous combustion of the fuel and air molecules inside the cylinder. |
31:06 | So one of the reasons why we don't see damage from the operation, normal operation of a diesel engine though is because the parts inside the diesel engine are built with this in mind. |
31:18 | So this is why you'll see components inside a diesel engine are much much beefier, much much stronger than parts in a comparable gasoline engine. |
31:28 | So yeah very very different engines, very very different engine construction, and completely different operating principle. |
31:35 | D Martin's got one last question, who's asked, should you refine the main injection first and then refine the pilot injection, or a combination of back and forth for optimum results? In our own testing so far, we've basically started with a developed pilot pulse injection table which again as I've mentioned a couple of times now, you're probably almost certainly going to be doing as well, and then optimising the main injection pulse. |
32:02 | This is still gonna be the place that's gonna have the most effect on your engine performance. |
32:07 | Once you've got that pretty well dialled in where you want it then it's definitely worthwhile going back and having a look at your pilot pulse, trimming that and seeing if that's had any effect. |
32:20 | Alright guys that's brought us to the end of our questions there so thanks guys for all of those questions. |
32:26 | Hopefully that's given you a little bit more insight into another aspect of diesel tuning. |
32:30 | Of course we will be having plenty more diesel tuning webinars coming up, as well as our course when that is released. |
32:37 | As usual if our HPA members have got any further questions, please ask those in the forum and I'll be happy to answer them there. |
32:44 | Thanks guys, I'll see you all next week. |
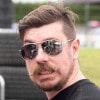