202 | Getting Unbeatable Launches With Launch Control
Summary
If you want fast and consistent launches from a standing start, launch control is a valuable function to understand. In this webinar we’ll discuss how launch control works, what options are available, and go through the process of configuring and testing it on our 1UZ GT86 using a MoTeC M150.
00:00 | - Hey guys, Andre from High Performance Academy, welcome along to another webinar. |
00:04 | And this time we're going to be talking about launch control and how we can utilise launch control to give us fast, consistent, reliable standing starts. |
00:13 | Now when we talk about launch control, quite often I end up getting a few people saying that they can get fast standing starts manually, just using their own combination of RPM and clutch position. |
00:27 | Well that's great and quite often that will be the case, with a really talented driver they will be able to get good standing starts. |
00:34 | The problem with this is getting consistency with those standing starts is a little bit more tricky. |
00:41 | And it's really difficult for even a talented race driver to do exactly the same thing on every standing start. |
00:48 | And this is where a computer is really hard to beat. |
00:51 | You tell the computer what to do and that computer is gonna do exactly the same thing every time. |
00:56 | So this is why relying on a well tuned launch control strategy can give you a real benefit and a real advantage on the start line. |
01:05 | Now the other thing to mention here is that if you've got a driver who really is genuinely very talented and can get some amazing standing starts, well that's still great because what it means is that we can datalog exactly what the driver's doing during that launch and then we can use that data and help replicate it using the launch control strategy. |
01:26 | So either way there's a lot to be gained here by using the launch strategy. |
01:30 | As usual with this webinar, we will be having questions and answers at the end so if you've got anything I talk about that you'd like me to delve into in a bit more detail, please ask those questions in the comments and the guys will transfer those through to me. |
01:44 | OK so we've talked about why we need launch control, where that advantage is, the ability to get those fast consistent standing starts. |
01:51 | Also just a subtle aspect there is that we can really fine tune this system and optimise the amount of wheel spin we get to really try and get the most traction off the line. |
02:03 | However the other aspect we need to talk about is how the system works. |
02:07 | And really here we're breaking it down into two types of launch control strategy. |
02:12 | The first is where we are using the ECU to provide just a secondary rev limit. |
02:20 | So basically when our foot's on the clutch, or the car's stationary, we've got a lower RPM limit, so instead of launching off the engine's rev limiter, normal rev limiter, at let's say 7500 or 8000 RPM, we might be holding the RPM at 4500 until the clutch is released. |
02:36 | So that's a simple strategy, as soon as the clutch is released or wheel speed is detected and the car starts moving, then the normal engine rev limiter will be reinstated. |
02:46 | Now the problem with this sort of system is of course once the car has actually left the line it's still up to the driver to actually control wheel spin using the throttle. |
02:55 | The other type of system that we have available is where we are monitoring the wheel speed as well as the ground speed. |
03:03 | So this is really only applicable on a two wheel drive vehicle. |
03:07 | So let's say here on our Toyota 86, we're a rear wheel drive vehicle, we are monitoring the wheel speeds on all four corners of the car through the ABS unit, this is data coming into the ECU via CAN. |
03:18 | And from the front wheels what we're getting is ground speed. |
03:22 | So what we can then do is set up a three dimensional table, essentially giving us a RPM limit relative to our ground speed. |
03:30 | So let's just quickly head across to my laptop screen. |
03:33 | And we'll see exactly this here, on the right hand side of my screen. |
03:37 | Don't worry we're gonna talk about this in a bit more detail here. |
03:40 | But let's just full screen this. |
03:44 | And what we've got here is a three dimensional table. |
03:47 | Doesn't actually need to be three dimensional but we've got vehicle ground speed on our horizontal axis here and then, the reason this is three dimensional is on our vertical axis, we actually have the ability to run a multi position driver switch here, so we can choose our launch control strategy based on a driver switch, and this allows on the fly adjustment depending on track conditions, let's say, the race initially starts and it's going to be dry and then on the out lap maybe it starts drizzling or pouring with rain, we can adjust the launch control strategy while the car's actually on the track. |
04:21 | So the numbers inside this table are of course our engine RPM limits. |
04:25 | And if we look at that graphically we can see a nice exponential shape to this. |
04:30 | Now we'll find out how we get that data shortly as we go through today's webinar. |
04:35 | Let me just head back across to my notes here for a second. |
04:40 | OK so those are our two main methods there. |
04:43 | So the first method where we've just got either a simple clutch switch or a simple system where the car is stationary. |
04:50 | Quite often this is referred to as a two step launch control or two step limiter. |
04:56 | And it's quite often used in a drag application. |
04:58 | We'll see a little bit later on in the webinar how we can use this strategy as well to build boost. |
05:04 | But of course, as I've mentioned, the downside there is as soon as we drop the clutch, often it's up to the driver again to control wheel speed. |
05:12 | Another consideration we need to factor in here is our clutch slip. |
05:17 | So there's only so much that the ECU can do here and really what we're doing is using the ECU in some way shape or form to limit the engine RPM, and the reason we're doing that is because there's obviously a relationship in first gear between our engine RPM and our rear wheel speed. |
05:35 | So by limiting that RPM, we can limit the amount of wheel spin being produced. |
05:39 | The problem is if we look at the relationship between engine RPM and our wheel speed, obviously when our wheel speed is zero, when we're sitting there stationary, the engine RPM, to achieve that, if the clutch is fully engaged, would also be zero. |
05:55 | Clearly we don't want that, that's not gonna work. |
05:57 | If we drop the clutch and the engine RPM was clamped to zero, the engine's going to stall. |
06:02 | So this is a little bit problematic and really to get really perfect starts, get the best possible start, there is still a little bit of driver involvement that we'd like to have in here and what this really entails is the driver not simply side stepping the clutch. |
06:17 | Instead what we want to do is have the driver just gently release the clutch and allowing a little bit of wheel slip initially, and what this does is it just smooths that transition between our engine RPM and our rear wheel speed sort of matching where we want it to be. |
06:33 | So it prevents us needing to clamp that engine RPM down too low and have risk of the engine stalling or dropping off boost if we've got a turbocharged car. |
06:41 | But we don't end up with our wheel speed jumping straight up to a excessive level. |
06:49 | So let's just have a look at that on a little horribly drawn graph that I'm going to make here so let's look at a little two dimensional graph that we're gonna draw. |
07:00 | So what we've got here is our wheel speed. |
07:08 | Let's try that again, told you it was gonna be a horrible drawing. |
07:11 | OK so we've got our wheel speed on the vertical axis there. |
07:16 | And we've got our start point is gonna be right here. |
07:21 | So this is where we're actually dropping the clutch. |
07:24 | So what we're going to end up with in the perfect world is we want something that sort of ends up going a little bit like this. |
07:30 | So we actually start with our wheel speed at zero. |
07:32 | Of course what we end up getting when we drop the clutch with let's say 4000 RPM on board, is initially our wheel speed jumps straight up and we've got a lot of wheel spin and then we sort of try and wait for it to catch up like this. |
07:45 | So this is the area here where what we can really do is get some benefit from slipping the clutch slightly so that we don't have excessive wheel spin. |
07:54 | And another key to understanding this as well is understanding how our tyres work. |
07:58 | And most people think that in order to get maximum acceleration from our tyre, we don't want any wheel spin. |
08:05 | That's actually not the case. |
08:07 | There's several studies and tests have shown that we find that depending on the particular tyre we're running, that we'll actually get maximum acceleration with a small amount of wheel slip, somewhere in the region of about 6-10%. |
08:21 | So we actually want the rear wheels in a rear wheel drive car to be just ever so slightly spinning and that's going to give us a traction advantage from having everything completely hooked up and no wheel spin at all. |
08:34 | Alright so hopefully at this point we've got a bit of an understanding of the techniques available. |
08:40 | We've got our basic two step style launch control and then our ground speed based launch control. |
08:45 | Now the other thing that we need to discuss here is the way the RPM limit can be configured because this has a big impact on the reliability of a lot of engines. |
08:55 | So when it comes to RPM limit configuration, we can choose to set up our RPM limit using either a fuel cut or an ignition cut. |
09:04 | Now I've talked about this numerous times and there are some specific webinars in the archive that you may want to review, if you search for RPM limit, you'll get a little bit more background on these strategies and the pros and cons of each but essentially in a nutshell, the ignition cut style RPM limit can be quite harsh on engines that have sensitive valve trains. |
09:29 | One that I'll just pick out that I know quite well is the Nissan SR20 DE and DET with their quite heavy rocker style valve actuation. |
09:38 | These don't respond well with an ignition cut rev limiter unless the rest of the engine has been modified to suit. |
09:45 | And if you're not careful, this can result in the rockers being thrown off and quite a lot of expensive damage being done. |
09:53 | So the gentler technique there is to use a fuel cut limiter and this is what I'd recommend unless there's a very good reason why you need to use an ignition cut, and that very good reason would be if you are running a turbocharged drag car and you've got a large turbocharger and you're trying to drive that really hard in order to build boost on the start line. |
10:15 | In this case you're going to be needing to use a lot of ignition retard and that strategy will only work well if you are using an ignition cut. |
10:23 | Don't worry, we're gonna talk a little bit more about how that works very shortly but essentially just you need to understand if you are using that, there are some downsides that you really need to keep that in consideration with your engine build and make sure that the engine is going to be reliable with that. |
10:39 | OK so let's talk about our two step launch control first of all and we'll have a look at how that can be set up. |
10:47 | So the two step is the simplest because we really don't need a lot of inputs to the ECU. |
10:53 | You don't need wheel speed. |
10:55 | This will often be set up with a clutch switch. |
10:59 | So we'll just have a simple digital switch that is connected to the clutch, and wired up to the ECU, and essentially while that clutch switch is active, it'll simply bring in a lower engine RPM limit. |
11:10 | So it's very very simple, all we're doing is we're choosing a launch RPM level that's going to allow us to get off the line without massive amounts of wheel spin. |
11:20 | But of course we want to launch the engine somewhere where it's actually producing enough torque to turn the wheels and get the car into a little bit of wheel spin so we can start getting moving, and then as I've mentioned, it's up to the driver of course to modulate the throttle to control the amount of wheel spin that it's getting. |
11:38 | So the advantage here is simplicity, we really only need that clutch switch. |
11:42 | One thing I will mention here that is often set up wrong with this style of launch control is that we do want the clutch switch to be quite carefully set up so that the clutch switch is activating right on the point where the clutch is beginning to engage. |
11:59 | So quite often you'll find that a factory car will have a clutch switch. |
12:03 | Sometimes the clutch switch operation isn't ideal for this type of launch control though so an example here is where the clutch switch happens right at the very top of the pedal, so that as soon as you start touching the clutch and start moving it towards the floor, the clutch switch will engage. |
12:19 | Now of course the problem here is that as we start releasing the clutch, the clutch will start grabbing or start engaging well before the pedal gets to the top of the travel, so we've sort of launched the car and we're still sitting on our secondary rev limiter. |
12:35 | So this can result in the car stalling or at least not getting off the line cleanly. |
12:40 | So that's one really key point that we need to keep in mind there. |
12:44 | Now I'll just show you quickly here in the Motec software, so let's jump across, this is actually the older Motec 100 series ECU manager software. |
12:52 | But I just want to show you quickly how we can set up that style of launch control. |
12:56 | So if we go into our adjust menu, and we'll set this up in our digital input functions. |
13:02 | And the input function we're looking at here is listed. |
14:02 | Alright sorry about that guys, just lost the laptop but we've got it back up and running now. |
14:07 | So just wanna show you this on the Motec 100 series ECU software. |
14:11 | There are a couple of varieties or variations on how this will work. |
14:16 | But the basic or fundamentals are pretty similar. |
14:18 | So I'm not quite sure where that laptop dropped out here. |
14:21 | So we'll start again, on the adjust menu, if we go to our digital input functions and you'll see here that digital input two is set up as dual RPM. |
14:29 | So this is the function that we are setting up and if we click on our parameters, this is where we can set up that dual RPM limiter. |
14:36 | Not too much to worry about here that's too advanced. |
14:41 | We've got our logic polarity so this is essentially when the ECU will engage the dual RPM limiter. |
14:48 | So basically whether that clutch switch or digital input is in the high or the low state and then we've got our low RPM rev limiter. |
14:57 | So in this case, this is actually for a drag car that we tuned back many years ago. |
15:02 | So the actual main engine rev limiter's about 10500 RPM and we're leaving the line there at 7200 RPM. |
15:09 | So that's as simple as it it, basically as soon as the clutch is engaged, the RPM limit goes from 7200 up to our normal engine rev limit. |
15:16 | There are a couple of other functions here, RPM rise rate and ignition retard. |
15:21 | I'm not gonna touch on these now, we're gonna leave those for a moment, we'll talk about those a little bit further through the webinar. |
15:27 | That's sort of some of the more advanced functions there so just give me a second here, I'll get back to where we were. |
15:37 | OK so essentially the process for tuning the two step style launch control is a trial and error approach where we're just going to adjust our secondary rev limiter and try launching the car. |
15:52 | And really we're just trying to get that nice compromise between a little bit of wheel spin without it becoming excessive. |
16:00 | Obviously if we've got it set too high, when we drop the clutch, the car's essentially not gonna move and it's just gonna sit there and go straight up onto the engine rev limiter. |
16:08 | If we, on the other hand have our RPM launch limit set too low, the car is likely to bog in and become, the engine may even stall when we drop the clutch, so really the only way of getting through that is a little bit of trial and error. |
16:21 | But the next method we're going to talk about is a lot more advanced and gives us a lot more control and this is where we are going to need a car set up with speed sensors. |
16:32 | In particular we're going to need here a speed sensor that's going to give us ground speed. |
16:37 | So this is from an undriven wheel. |
16:39 | Now I will mention here, this potentially can be done using a GPS speed input. |
16:45 | I haven't personally done this, this is something we wanna test out in the not too distant future. |
16:50 | You cannot do this reliably and effectively though with the standard 10 hertz style GPS that most aftermarket ECUs and dashes are using. |
17:01 | 10 hertz is simply not fast enough in its update to be able to give us launch control or traction control strategies. |
17:10 | What we're going to need instead is one of the more expensive 50 hertz style GPS' so we're hoping to test that in the not too distant future and then we'll have a little bit more detail around exactly how well that works. |
17:22 | Alright so if you've got your speed based input then what we've got is a lot more functionality around basically controlling our rev limit based on our ground speed. |
17:34 | So this is what we already looked at, let's just jump back across to my laptop screen here in. |
17:38 | In the Motec we've got our three dimensional in this case table of our RPM limit versus our ground speed. |
17:45 | But of course the key is where do we come up with numbers to put into this table? And this is where we are going to need to do some testing. |
17:53 | So what I suggest here is that, we'll just jump across to my laptop screen again. |
17:59 | What I suggest here is that you gather some actual solid data to get a locked down relationship between your engine RPM and your ground speed. |
18:08 | So what I've done here, this is actually when we were setting up the launch control strategy on this Toyota 86 here before a race meeting. |
18:15 | So at the top here we've got our engine RPM in purple and we've got our throttle position in green, not too worried about that. |
18:23 | At the bottom is the key to all of this though, we've got our wheel speeds. |
18:27 | So what I've done here is I've just got the car moving, I've sort of given the engine a bit of RPM just to get it moving and then we've engaged the clutch at very low wheel speed or ground speeds. |
18:39 | So in this case we're sort of only starting at about seven or eight kilometres per hour. |
18:42 | And at this point the clutch is compeltely engaged. |
18:46 | And what we want to do is accelerate the car with absolutely no wheel spin. |
18:50 | So we're doing this quite smoothly, not using a lot of throttle, we're not using a lot of power. |
18:55 | We want to accelerate that all the way through to the rev limiter in the top of first gear. |
19:00 | So you can see that's exactly what I've done here. |
19:03 | We've only used the maximum of about 57% throttle and we've got up to 8500 RPM. |
19:08 | So what we've now got is some solid data on what the wheel speed versus engine RPM relationship is or ground speed versus engine RPM relationship is in first gear with absolutely no wheel spin. |
19:23 | So what we can do is then take this data and use it to populate our launch control ground speed table. |
19:30 | So that's back over here. |
19:32 | So for example here at 8500 RPM, we can see that we're basically sitting at about 70 kilometres per hour. |
19:39 | So if we come back over to our table, this is what we're going to then be filling our table in with. |
19:46 | So let's just head back to the start of this table. |
19:50 | So it's important to understand, again we've got that sort of initial bit where we leave the line, obviously we can't leave the line with zero RPM. |
19:59 | We need enough RPM to actually get the car to generate a litle bit of wheel spin and leave the line without the engine bogging. |
20:09 | So that's a bit of a trial and error method again, exactly like our two step and we found that on a dry track with our slicks on this car, 4500 RPM gave us a pretty good compromise, it smoothly left the line without a lot of wheel spin, and the engine wasn't bogging. |
20:26 | Problem is, 4500 RPM, if we go back to our log data and we have a look at what 4500 RPM gave us, we can see that's gonna actually be about 35 km/h of wheel speed. |
20:38 | So this is the problem, if we lock our clutch there and we just jump off the clutch completely, as soon as we do that, the rear wheel speed's gonna jump straight up, let's just draw a little bit of a line, that's probably better than my last attempt. |
20:51 | Our rear wheel speed's gonna jump straight up and we're gonna go something like this. |
20:54 | Now that'll work but again remember what we're trying to get is somewhere around about maybe 8-10% wheel slip so that's not ideal. |
21:02 | So we still want to have some clutch slip in there and what we need to do if we go back to our 3D table here, is we actually end up bringing our engine RPM down. |
21:14 | So what we can see is we leave at 4500 RPM, and then between zero and 15 km/h we actually pull our engine RPM back down slightly, and this just helps reduce that massive wheel spin we initially get, we're coupling this of course with the driver manually slipping the clutch a little bit. |
21:32 | So we hold about 4300 RPM and then by the time we get to 20 km/h, this is where we actually start the RPM climbing again. |
21:39 | And this is a key part that a lot of people overlook when they are setting up ground speed based launch control. |
21:45 | We don't wanna just hold our initial launch RPM and then increase from there. |
21:50 | That's gonna result in way too much wheel spin at low ground speed. |
21:54 | So we actually wanna reduce our RPM and we're going to need to test this because again, if we reduce our engine RPM too much, we risk having the engine actually stall or drop off torque and then we're going to be in a bit of trouble. |
22:09 | So it's a bit of a balancing act there. |
22:12 | Once we get to a point where we can start accelerating the engine though, what we're looking for is basically creating just a little bit of wheel spin and we can do this quite accurately. |
22:21 | So I don't actually know how well this will work but let's have a look here. |
22:24 | So at 50 km/h let's just have a look and see what our engine RPM is. |
22:29 | So I'm just cycling through here and we see that our front and our rear wheel speeds were both 50 km/h and we can see at that point we've got around about 6200 RPM. |
22:40 | So what we can do there, if we also look at a 10% slip, that will give us about 55 km/h and we can see 55 km/h, we've got about 6700 RPM engine speed. |
22:58 | So what we can do is go back to that. |
23:00 | And you can see, yeah I actually have done my job pretty well there. |
23:03 | We've actually got our RPM limit there set at 50 km/h at 6600 so again just trying to get that little bit of wheel spin, maybe around about 8-10%. |
23:13 | And again there's a little bit of trial and error comes in here. |
23:16 | We can't say that 8-10% wheel spin is a rule of thumb that's applicable to every vehicle and some testing needs to be done. |
23:23 | Of course with the data logging and the launch control strategy, the advantage here is that we can do several back to back tests, varying our launch RPM table by let's say 100 or 200 RPM. |
23:33 | And quite quickly we should be able to zero in on the sort of numbers in this table that actually give us the best possible results. |
23:42 | So then of course once we've got to a point where wheel spin isn't really an issue, we can increase the table values, so you can see here, by the time we get up to 70 km/h in first gear, or even 60 km/h, wheel spin really isn't too much of a consideration. |
23:57 | At 70 k there I've hit 9000 RPM as my launch limit. |
24:01 | That's actually above the factory, the main engine speed limiter. |
24:06 | So what this means is the lowest of any of the engine speed limits becomes active so we'd basically be sitting on our 8600 RPM engine speed limit. |
24:16 | And at this point of course I'm gonna be shifting into second gear as well. |
24:19 | Alright remember we are gonna be having some questions and answers. |
24:22 | I know this is a complex topic, I've tried to break it down and make it as simple as I can but yeah it is complex so feel free to ask any questions and I will try and clear those up. |
24:32 | Before we get into our questions and answers, I just wanna talk about a couple of other aspects here which is the more advanced topics of tuning launch control. |
24:43 | So in some ECUs we may also have the ability as well, or in addition to just controlling our launch RPM or our RPM versus ground speed, we may also be able to adjust our drive by wire throttle opening. |
24:57 | And here what we're doing is we can basically use the drive by wire throttle translation to map the throttle opening during first gear. |
25:06 | And this allows the driver to stay at wide open throttle, but instead of delivering way more engine torque than we actually need, we can reduce the throttle opening to try and basically match the amount of engine torque being delivered to the amount of traction available. |
25:21 | So this just means that our rev limiter isn't working so hard, it's smoother on the engine and well tuned, that can give us a bit of an avantage in terms of our launch control strategy. |
25:32 | The other aspect that I wanna talk about here is building boost on a turbocharged engine, 'cause this is really important, particularly if you've got a large turbocharger on a small capacity engine. |
25:44 | And this is where we may want to have an ignition retard being used to help basically create combustion very late in the engine cycle. |
25:55 | We're also going to be using this generally in conjunction with an ignition cut rev limiter so we've got unburned fuel and air passing through the engine and combusting in the exhaust system. |
26:05 | And when this happens, essentially it creates a lot of energy to drive the turbocharger. |
26:11 | And using this strategy to our advantage, it's possible to spool turbochargers that traditionally maybe on a small capacity engine, we may not see full boost 'til 6000 or 7000 RPM. |
26:22 | We can have full boost at maybe as low as 4000 or 4500 RPM for our launch control strategy. |
26:29 | So there's a couple of ways we can do this and we're just gonna head back across to my laptop screen and we're going to look here at our Motec 100 series. |
26:39 | Again just to try and show you a couple of different variations of how this works. |
26:43 | And while this isn't gonna be the same on every ECU, the strategy or fundamentals are the same. |
26:49 | So again we're looking at our dual RPM limit here. |
26:52 | And the aspect that I didn't talk about before was this parameter here, our ignition retard. |
26:59 | So what we can do is use this ignition retard value to retard the ignition timing from the normal ignition table values. |
27:06 | And we can retard it depending on how we've set this up in the Motec. |
27:09 | Either in degrees from our main table value or we can retard it in a percentage of that main table value. |
27:20 | So this allows us to adjust the ignition retard value, and again as I've mentioned, this creates combustion late in the engine cycle into the exhaust system and helps build boost. |
27:31 | The problem with this is it's very black and white and it doesn't give us a lot of control. |
27:36 | Basically if we wanted to retard the timing there by 30 degrees, that's gonna be a fixed amount of retard and what we find is that initially to start building boost on the turbocharged engines we may need a lot of retard, 30 degrees probably isn't uncommon, but as the turbocharger starts to create boost, basically it becomes self fulfilling and we don't need to use as much retard anymore. |
27:58 | So with a system like this where we've got a fixed ignition retard value, what we can find is that the boost actually continues to climb a little bit out of control or at least above where we want it to be. |
28:09 | So the way I've actually done this in this particular calibration, let's just have a look. |
28:13 | Instead of using that value, I've left it zeroed out. |
28:15 | And I'm actually using an ignition comp table instead. |
28:19 | So we'll go across to ignition comp one. |
28:20 | So this is set up as a three dimensional table. |
28:24 | And what we've got here is our two step posiiton. |
28:27 | So whether our clutch switch is in or out, and on the load axis here we've got our manifold absolute pressure. |
28:35 | And what we can see is that when the clutch is engaged, so when our foot's off the clutch pedal, there's absolutely no compensation being applied here. |
28:43 | We've just got our normal ignition table, our main ignition table values being applied. |
28:47 | However when our clutch is disengaged, when our foot is on the clutch, we're going to be operating over in this column one. |
28:55 | So we can see that down in the vacuum areas, we've got no trim being made. |
29:01 | And the reason for this is again if every time we put our foot on the clutch, we're pulling out 30 degrees of ignition timing. |
29:06 | This can make the engine really hard to drive around the pits or bring it up to the staging line and what we find is that every time we put our foot on the clutch, because we're pulling so much retard out of the engine, or timing out of the engine, the engine can want to stall. |
29:19 | So this allows us to drive the car around the pits or up to the staging line completely normally. |
29:25 | But as soon as we go above 95 kPa, so essentially we're gonna need to be pretty close to wide open throttle. |
29:30 | We start pulling a little bit of timing 10 degrees in this case. |
29:32 | Then as the RPM builds and we start coming up to 105 kPa, we're pulling 20 degrees. |
29:40 | Once we get into the meat of this table here you can see we're really aggressively pulling out 32 degrees timing. |
29:45 | However in this case our target boost pressure was 250 kPa so that's 22 psi of positive boost. |
29:52 | Once we go above this, so in this case 260 kPa, you can see that we're actually adding some timing back in. |
29:58 | Instead of 32 degrees retard, we're only retarding the timing by 28 degrees. |
30:02 | So by setting this table up, we've actually go quite a good amount of control, and coupling this with a wastegate control table as well to control what the wastegate's doing and where it's opening, when we're on the two step, we can actually get really really good control of our boost pressure. |
30:16 | Particularly for a drag application, it's really important to make sure that every time we leave the line, we've got the same RPM, we've got the same amount of boost, this gives us consistent parameters to allow us to tune the engine properly, and allow us to expect to get good control. |
30:31 | The other aspect here that I just wanna talk about, our last topic that I'm going to touch on, again we'll just use the M800 software. |
30:38 | If we go back into our digital input functions and we go back to dual RPM, and we go into parameters, there's one more parameter here that I haven't talked about yet which is the RPM rise rate. |
30:48 | Now at the moment this is actually set to zero. |
30:50 | So this function does nothing. |
30:52 | It's a really nice function that I use quite a lot with some of the four wheel driver drag cars we tuned where we couldn't use the ground speed based launch control table. |
31:02 | So here we would have the engine making, in this case, about 22 psi of boost at 7200 RPM. |
31:08 | And when the driver side stepped the clutch, the engine's obviously producing a lot of power and it is quite possible here that the engine would just break away or the car would break into wheel spin and run straight up onto the engine rev limiter. |
31:20 | Now we didn't want that to happen and it is really really hard with these cars to control this with the accelerator pedal. |
31:26 | So what we did instead was use this RPM rise rate function. |
31:30 | So this essentially dictates how quickly the engine RPM can rise from our low RPM limit, in this case 7200, up to our main engine RPM limiter. |
31:41 | So for example if we set this RPM rise rate to 3000 RPM, what that would mean is that it could rise at a rate of 3000 RPM per second, and the ECU would instigate essentially a continuous rev limiter that increased as the time went by to make sure that we didn't break straight into wheel spin. |
32:00 | So I kind of used this as a bit of a safety backstop so that if we had a little bit too much power, and the car did break into wheel spin, it wasn't just gonna sit there on the line moving nowhere and running straight onto the RPM, the main engine RPM limit. |
32:13 | Alright so complex topic, a lot to take in, hopefully that has helped you understand there. |
32:20 | Remember if you do want a really thorough understanding of this, we do have our launch control tuning course which goes into a lot more detail including worked examples that I can't really do justice to here in a short webinar. |
32:30 | We'll jump in now and we'll have a look at our questions. |
32:36 | First question comes from Craig who's asked, could a clutch solenoid be used to control the clutch control slip with launch control similar to a line lock control? Craig, absolutely and in fact that's exactly what we did with our four wheel drive drag cars. |
32:50 | I'd like to think that I was one of the first people to use this and in fact I think it was probably a situation where at the time I was drag racing, there were a lot of competitors using this and no one wanted to talk about it. |
33:02 | So I don't know where I came in terms of whether we were first or whether we were last but we were definitely using it to our advantage. |
33:09 | So what I was actually doing, just to explain the system in detail, what I was doing was I was plumbing a modified boost control valve, this was a manual Turbosmart Boost Tee into my clutch line. |
33:22 | And essentially what we were doing there is the boost tee could be used to control how quickly or how slowly the clutch pedal would release. |
33:31 | So the driver could come up to the line, stage the car, and then when the tree counted town, could just literally side step the clutch and the clutch pedal would actually take almost two full seconds to come back up from the floor. |
33:42 | So this made sure that the clutch would slip if the car came off the line. |
33:46 | And this transformed all of our cars from cars that would be very difficult to get consistent launches to ones that were cutting really really good reaction times and really good 60 foot times. |
33:58 | The Evo 9 that we built that claimed the world record, that ran consistent 1.260 60 foots. |
34:05 | Which only recently we've seen a few cars go faster than that. |
34:09 | So yeah really really important particularly for a four wheel drive drag car to get consistency there. |
34:17 | Andy has asked, what happens when both front wheels are in the air? Well if both front wheels are in the air, you're probably gonna have a bit of trouble getting ground speed aren't you. |
34:25 | The issue is that this is really something we're using predominantly for circuit racing where we're using ground speed based launch control and I have not been fortunate enough to tune any circuit cars that launch with the front wheels in the air. |
34:40 | Definitely more of an issue for drag racing, however drag racing in a lot of instances, specifically prohibits a lot of these ground speed based launch control strategies that I have talked about. |
34:52 | There's ways around this though. |
34:54 | A lot of the very powerful two wheel drive drag cars will be using a profiler. |
35:01 | Excuse me I'll try and get my words out. |
35:06 | In Haltech with their race expansion module, they include torque management and essentially what they're doing there is profiling the driveshaft RPM versus time. |
35:16 | So profiling a perfect pass and how fast the driveshaft RPM increases versus time during the run. |
35:24 | And if the car breaks into wheel spin, of course the driveshaft RPM is going to spike and then the torque management strategy can do something about that, either fuel or ignition cutting or ignition retard. |
35:37 | So no matter how you wanna go about this or what these perceived rules are in a class, there's always potential ways around this. |
35:45 | Quentin has asked, for older cars with no existing wheel speed, ground speed data or ABS sensors, have you retrofitted a ground speed sensor and if so, what's the method you'd normally use to retrofit wheel speed? There's a variety of options there, it's pretty easy normally to fit a speed sensor depending on what you've got to pick up from. |
36:05 | A pretty common technique if you've got access to them is to fit a speed sensor, a reluctor style, variable reluctance style sensor that picks up on the back of the wheel studs if you can get access to those. |
36:18 | That's pretty easy. |
36:19 | Another way of doing this is you can actually pick it up off the wheel. |
36:23 | So really it comes, or the brake rotor, really it comes down to just what you've got easy access to. |
36:30 | But there is gonna be a little bit of ingenuity in mounting a system like that up. |
36:34 | Darius has asked, could a pressure sensor be used on a clutch line to act as a position sensor and maybe have a gradual transition instead of an on off switch? OK so on face value you'd think that this might be a sensible approach and it's certainly something that I considered for a while until I sort of did a bit more homework on it. |
36:52 | The problem with it is that the clutch pressure is not something that we can correlate directly to clutch postion. |
36:58 | And for the reason that the clutch pressure, during the initial part of the clutch travel, is actually going to stay relatively consistent. |
37:06 | It will move around a little bit just dependant on the position of the diaphragm and the pressure that that's exerting but yeah you can't really use pressure alone to correlate clutch position. |
37:19 | You can use a clutch position sensor though, it's possible to fit a rotary or linear travel sensor to your clutch pedal, this can even be done at the clutch slave cylinder. |
37:30 | So again that's something you can use to get a lot more information. |
37:33 | The problem is though, you still need a way of manually controlling this, and this is where the driver being able to manually slip the clutch a controlled amount repeatedly every start is very difficult which is why we come back to the answer to Craig's question where we can use a solenoid and a bleed valve to control the rate that the clutch is engaged. |
37:56 | Mark Williams has asked, any extra concerns or tips with four wheel drive launch control? I've sort of touched on this, I mean this kind of was my specialty I guess through the last 10 years of my old shop where four wheel drive drag racing was kind of our main thing. |
38:12 | And yeah you can't use ground speed based launch control with this sort of system. |
38:18 | There's a couple of ways of doing it, I've already talked about the RPM rise rate, actually a technique that I didn't mention there is that in a lot of ECUs we also have the ability to provide timer based functions. |
38:29 | So with that four wheel drive system you could instigate a timer based RPM limit. |
38:34 | The problem with this is it's a passive system and if something goes wrong, you don't get the perfect launch, that time is still gonna be counting down and doing the same thing every time. |
38:46 | So it is something that you're going to need to really play with and test to get something that's working. |
38:52 | And the other option of course, which I've touched on in this webinar, haven't really done ourselves yet, is a high speed GPS based launch control strategy for four wheel drive drag cars. |
39:01 | I know that one of the people that we interviewed at World Time Attack Challenge which is god now I can't remember his name. |
39:13 | There's a very fast Subaru drag car from Scotland, hopefully someone in the comments is gonna be able to pick up the name that I've currently forgotten, running four wheel drive drive train there with a Syvecs ECU, he was using a 50 hertz GPS with ground speed based, sorry GPS based launch control. |
39:30 | So it's potentially possible. |
39:33 | Andy White, Andy White? Yeah, Andy from Scotland anyway, there we go. |
39:40 | Andy Forrest, that's the one, thank you. |
39:44 | Got there in the end. |
39:45 | Dave has asked, I'm adding a clutch slipper this year on my sport front wheel drive car, is there a general rule of how far out to slip the clutch, two feet, five feet, 20 feet et cetera? I've been doing it manually with good results but it's so inconsistent. |
39:57 | OK so from my own experience and admitedly this is all four wheel drive based, I haven't been involved with the tuning of any sport front wheel drive cars, is that you're actually probably going to need to slip the clutch quite a lot longer than you would initially think. |
40:11 | And I believe in our four wheel drive drag cars, ultimately we were slipping the clutch essentially the whole way through first gear. |
40:18 | And it's all about maintaining, or reducing that initial wheel spin that you're gonna get with a very high launch RPM. |
40:27 | Like we looked at in our Motec example there, that was from our Evo 9 drag car. |
40:32 | Launching the car at 7200 RPM, let's just say for round numbers, that was gonna give it a ground speed of 60 km/h. |
40:40 | So initially when we first dropped the clutch at 7200 RPM, that would involve the wheels spinning at 60 km/h. |
40:46 | Massive amounts of wheel spin, huge amounts of slip, we're not gonna get good traction like that. |
40:51 | So yeah I generally would start with our four wheel drive drag cars with the clutch movement taking around about 1.5 to two seconds and then I would tune from there. |
41:00 | And the advantage with that clutch slipper that we were using is that, if anyone's using Turbosmart Boost Tee, it is graduated, every time you move it a little bit it clicks so you've got really fine control over exactly how much slip that clutch has. |
41:15 | It doesn't take you very long to dial it in. |
41:17 | I will just mention here, a really big downside with that system is because you are creating a lot of clutch slip, obviously you're gonna be burning out clutch plates pretty quickly and we were going through a triple plate clutch in about 10 passes. |
41:30 | So yeah there's no free lunches in this world unfortunately. |
41:35 | Jay has asked, when using anti lag with launch control or rolling anti lag on a daily driven street car, can it destroy the exhaust valves and turbo if only used for brief periods like three to five seconds at a time, five to 10 times per week? I see where your question's going there Jay, and I'd love to be able to give you the confidence that you can do exactly that but there are just so many variations and aspects that go into this that could affect your end result. |
42:02 | Generally, I would say that short bursts of rolling anti lag or launch control like that shouldn't do any damage, but again as I've mentioned as well, you do need to consider the base engine configuration and whether that engine has a nice strong reliable valve train. |
42:16 | The problem with a very aggressive rolling launch control or anti lag strategy is that those big pulses of pressure that occur in the exhaust system from combustion, do tend to pop the exhaust valves back off the seat. |
42:29 | And when this happens, particularly if you've got a hydraulic lifter arrangement, this can pump that lifter up and then hold the valve open and of course then if you've got a rocker style system, valve actuation, this can involved the rocker falling off. |
42:43 | Lachie has asked, how can the launch control be tuned for different road surfaces, could it be adjusted by rotary dial, controlled by the driver? Yeah absolutely Lachie that's kind of what I was getting at with our three dimensional table in the Motec M1 there, that's a driver rotary switch that we can move on that vertical axis and you could use this for wet or dry road conditions. |
43:05 | I'm basically using this on tarmac for circuit racing so we've already got a reasonably consistent surface it's just whether it's wet, whether it's dry, whether it's just slightly damp. |
43:16 | Of course you could make much more dramatic changes to suit gravel versus tarmac as well if you've got a rally car. |
43:22 | Victor has asked, doing launch control on a stock turbo with a little more boost with a cat, does the cat make more damage to the engine? The cat won't make more damage for the engine but you do need to be very careful with that launch control because if you are using an ignition cut style launch control, where you're passing unburnt fuel into the exhaust system, that can damage the cat, likewise the explosions that occur with an aggressive launch control strategy on a turbocharged car, that will also quickly destroy your catalytic converter, so you do need to understand that. |
43:53 | I would suggest, if you are gonna use launch control, on an engine still equipped with a catalytic converter that you make sure you're using a fuel cut launch control and make sure that the engine is nice and smooth on that limiter. |
44:08 | Barry has asked, what would you recommend as the best method to reference ground speed when tuning four wheel drive cars where all wheels are driven? So same answer really there Barry is it's difficult, you can't really use a wheel speed to correlate to ground speed because as you've mentioned there, if you've got wheel spin, all four wheels are spinning together. |
44:31 | Particularly in our drag cars, we ran essentially a locked transmission, or locked four wheel drive differential so if one wheel spun, all of them were spinning. |
44:39 | GPS there is probably your best option, but again if you want to use that for a launch control strategy, you're going to want to get a high frequency GPS, at least 20 hertz, preferably 50. |
44:51 | Sard Engineering's asked, what are your thoughts on integration of drive shaft speed as opposed to the timer applied to the rising rate of engine speed? Also what are your thoughts on accelerometer data for measuring acceleration as opposed to looking at the slip ratio between driven and non driven wheel speed data? OK two questions in there, I'll actually deal with your second question first because that was something I actually meant to show and talk about so thanks actually for bringing that up. |
45:14 | So yeah if you've got a g sensor on the car, it is a really good idea, when you are doing your testing to log longitudinal g force. |
45:23 | And then what you can do, as you're making small adjustments to your launch control strategy, look at overlays with that longitudinal g force. |
45:30 | So that will show you whether you're making small improvements or you're going backwards because the g sensor's gonna be much more sensitive than you are. |
45:37 | So it's gonna pick up those subtle small changes in acceleration force. |
45:42 | And the other thing is when you are tuning this, you may find that you pick up acceleration in one area of your launch strategy, or launch phase, but then you actually end up going backwards in another area. |
45:53 | So if you're looking at the longitudinal g force there, you can decide where to pinpoint those changes, where you've made those improvements, keep those and fix the areas that you've gone backwards. |
46:03 | Now integration of driveshaft speed as opposed to a timer applied to rising rate of engine speed. |
46:12 | I'd need to probably think about this in a little bit more detail. |
46:13 | Basically for a manual transmission, if your clutch isn't slipping, the issue you're gonna have is that your driveshaft speed essentially is directly correlated to your engine RPM. |
46:24 | So I'm not sure where you're going with this, if you're talking about for that first portion where you've got wheel slip. |
46:33 | I'm not too sure there, sorry clutch slip. |
46:35 | As I've kind of mentioned in another question, again, not sure if this was your angle, on a lot of the drag cars they are using the driveshaft speed as a kind of subtle traction control strategy but yeah not 100% sure exactly where you're aiming with that one sorry. |
46:52 | Alright guys that has brought us to the end of our questions. |
46:55 | Hopefully I've made that topic a little bit easier to understand. |
46:59 | There is a lot to take in and of course as usual if you've got other questions that come up after this webinar has aired, please ask those in our forum and I'll be happy to answer them there. |
47:09 | Thanks heaps for joining us and I look forward to seeing everyone next time. |
Timestamps
0:00 - Launch control explained
2:00 - Launch control methods
5:10 - Clutch slip considerations
8:40 - RPM limit configuration
10:35 - 2 step launch control configuration
16:20 - Ground speed based launch control configuration
24:30 - Drive by wire throttle control
25:30 - Building and controlling boost on a turbocharged engine
30:30 - RPM rise rate
32:35 - Questions
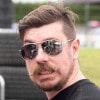