279 | Introduction to Using Damper Potentiometers
Summary
It’s unlikely you’ll find any high-end race car without damper potentiometers. In this webinar we’ll look at why they’re so useful and some of the things you can use them for to tune your chassis and dampers.
00:00 | - Hey team, Tim here from RaceCraft, welcome to today's member's webinar where we're going to be talking about damper potentiometers. |
00:06 | Today we're going to start by talking about some of just the basics and fundamentals of damper potentiometers, some of the more practical elements and then in a future webinar I'm going to get into diving much deeper into the actual analysis of the data itself. |
00:19 | There is quite a lot to consider when you think about damper potentiometers. |
00:23 | This is a term that's often shortened to damper pots, pots is just short for potentiometer, essentially we are measuring the position of the suspension and there's lot of different things we can do with that. |
00:36 | So the first thing to understand about damper potentiometers is there are lots of different types, lots of different ways they can be fitted, mounted, lots of different physical ways they can work. |
00:44 | If we just jump over to the overhead here, I've got a couple of different examples sitting on the table here I wanted to go through. |
00:49 | Now when most people think of damper potentiometers, this is the kind of thing they'll think of, this is what tends to come to mind, this is a linear potentiometer. |
00:55 | You can see it's only measuring travel along one direction, its general layout is it's got an inner section and an outer section. |
01:07 | It's got some sensing elements there to test, it wants to feedback position to where it is, they've usually got enormous resolutions, particularly... |
01:46 | Sorry guys, we just had to cut away there, we just had a couple of technical difficulties which we've now got fixed for you. |
01:51 | I was just talking about some of the general layouts and what these damper potentiometers look like. |
01:55 | So essentially we've just got this inner and outer part. |
01:57 | Obviously there's a sensing element in between there that's giving some feedback to whatever's doing the measuring. |
02:03 | So here you've typically just got a positive, like a positive voltage and a ground and then also an output for the position that it's going to be putting out in a raw voltage, that's what it's going to be outputting out of this thing. |
02:17 | So there's also some linear bearings at each end, so there's lot of different styles they can be, sometimes there's a quick release where they sort of pop on and pop off. |
02:26 | This is the most typical layout where essentially it's got a small spherical bearing at each end and that's just to allow for a little bit of misalignment as this thing travels so it doesn't end up binding up on the shaft. |
02:37 | So this is the most typical thing that people think of with their potentiometers. |
02:41 | I've got a couple of different styles here, well actually exactly the same style, exactly the same brand, even exactly the same series, this is just a longer body version and I'll show you guys a spec sheet a little bit later on for this particular damper potentiometer which shows the enormous range of different packaging lengths you can get these to, I think maybe in this series there's something like maybe 8 or 10 different free lengths in everything. |
03:03 | Usually the main metric that you're selecting these things on is their available stroke. |
03:09 | The most important thing with the suspension is to make sure regardless of where this is mounted, and we'll go through a few different options of that but the most important thing is to make sure that there is no way that we can get to the end of the sensor travel before we get to the end of the suspension travel, these things are really really easily damaged, they're very fragile so you want to make sure you've got a little bit of spare travel at each end. |
03:31 | So depending on where you're going to mount it in your suspension is going to depend on how much travel you go through. |
03:36 | Now there's also another relatively common type which is a rotary sensor so this is, you can see this is obviously this is rotating, this arm is rotating around this sensor, you can see that's the electrical connection there. |
03:48 | So the idea here normally is this section here would be bolted to the chassis and then this little arm, whether you use this original arm or whether you make your own. |
03:57 | the idea is this part's on the suspension and as the suspension moves up and down, this arm moves around and around and we can get the travel reading from there. |
04:07 | Now this is actually an OEM style sensor, the beauty of some of these sensors is they do tend to be a lot cheaper than the linear sensors. |
04:17 | In my experience I've actually had quite a good experience with these rotary sensors. |
04:20 | This particular model is actually really really cheap, I think these are only in the range of maybe $40 USD or somewhere where maybe I don't know exactly but we're probably talking more in the $100 - $200 USD for something like these linear potentiometers. |
04:34 | These are a particularly high quality Penny & Giles, linear potentiometer. |
04:39 | You can definitely get cheaper ones but I have found in my experience if you're looking for a budget option, something like one of these rotary sensors is a really good option. |
04:46 | I've actually got the box over here I'll just grab. |
04:49 | If you guys are interested for yourself this is the part number that's written on the top, I don't know if you guys can see that there but I'll read it out anyway, it is ER10031. |
05:00 | Now that particular sensor is quite commonly used in motorsport. |
05:04 | In one of the previous high end GT teams I worked in, we made use of this exact sensor in the car. |
05:11 | And one of the reasons for that is when it came to crash damage and stuff, this was a lot cheaper and easier to replace than constantly going through these. |
05:17 | Not that we're necessarily crashing the car every race but these are very very sensitive and don't take much to damage whereas something like this is a little bit more out of the way, probably a little bit less likely to get hurt in the first place but if it does, much much cheaper to replace. |
05:32 | So that's a couple of different styles of how those, that's the main 2 styles of damper potentiometer you tend to come across. |
05:39 | Next I wanted to talk about the different mounting options, the way these work and it's probably easiest to do that with a sketch, so I'll just stay on the overhead here and I'll just do a little bit of a sketch. |
05:49 | So if we're looking at, let's draw our tyre here, so just a front or a rear view of the tyre. |
05:55 | So the most common, we I wouldn't say the most common but maybe the most intuitive way that this is working is if you've got your coilover something like this. |
06:07 | So one really common way it's done is we end up mounting the sensor in parallel with the damper. |
06:14 | So what we're measuring is directly the damper position. |
06:16 | So the way that might work, you might have some mount coming off the top part of the damper and some mount somewhere rigidly on the body of the damper and then we'd have our little linear potentiometer here running in line. |
06:27 | So in this case we're directly measuring the damper position in parallel with the damper so the amount of length change we get here, is exactly the length change we get at the damper. |
06:39 | Now there are, probably the next most common way that would work is if you've got your, let's say you've got a suspension arm here. |
06:47 | Let's say you've got another suspension arm here. |
06:50 | The next most common way to do that would be to run a linear potentiometer attached to the chassis. |
06:56 | So let's say you've got a chassis coming down like this. |
06:59 | You might have your linear potentiometer mounted here. |
07:03 | And it might be mounted to a lower control arm. |
07:06 | Now part of that is because sometimes you've got space constraints around where the damper is mounted, sometimes there's not a lot of room, either between the damper can be really close to the tyre, the inside of the damper can be really close to the body, maybe you've got brake ducting and all sorts of stuff going around there, sometimes it's difficult to package so that's an option there is to mount it to one of the suspension arms. |
07:27 | Anything that's moving with respect to the wheel is fine. |
07:28 | We'll talk about the calibration a little bit later, the calibration differences. |
07:31 | Another option which is in the case of a rotary sensor, we might have something really similar to this, maybe our, going to get a little bit messy here but I think you'll get the idea. |
07:42 | if you've got a rotary sensor mounted to the body like this you might have one dropping down onto the suspension arm itself and obviously that is rotating up and down with the suspension. |
07:50 | So those are a couple of the different ways you might mount these things. |
07:54 | Really it's down to a little bit of personal preference and your exact packaging situtation. |
08:00 | It can be a really busy and hostile place inside one of the wheel arches like that so you've just got to think about making sure there's no way it can get damaged. |
08:07 | Making sure it's going to be easy to service, thinking about making sure it's not damaged when you're servicing the car as well, so making sure it's easy to disconnect so that there's not the tendency to try and leave it connected while you pull your dampers out to make spring or damping changes and stuff like that. |
08:22 | It's really a practicality thing and there's not really necessarily a right or wrong way to do it. |
08:28 | Most of the differences can be taken up in the difference when we do the calibration as well. |
08:33 | So one of the things that can be a little bit overwhelming when you first go and choose one of these things is OK you've decided where you're going to mount one of these things, maybe you've had a look through the spec sheet already, you're kind of overwhelmed, it might be a little bit overwhelming at first by the number of different sensors you can get that might even work for your situation but I'll go through a couple of the different practicalities that can help you narrow it down a little bit. |
08:57 | But the part numbers are often quite complicated but the good thing about it is that normally you can go to the spec sheet and read off what those mean so I'm just going to give you an example of what this means. |
09:07 | The part number here, to give you an idea, it's going to be too small to see on the overhead but it's SLS130/75/C/66/1/N. |
09:16 | Now that's going to be absolutely meaningless but you are going to need that exact part number when it comes to actually ordering them. |
09:24 | So if you just jump across to my laptop screen again I've actually got the spec sheet for this exact series of damper potentiometer here. |
09:32 | Now there's a bit of a general description about the purpose and what this sensor's intended to be used for. |
09:38 | Then we've got all of the specs as far as the performance and one of the main ones you'll be looking at here is the damper stroke section. |
09:45 | So that you can see for this particular series which is MLS130, these are all the different strokes we've got available to us here, so there's 25, 50, 75, 100. |
09:55 | So you can see there's a whole lot of different options there straight away. |
09:57 | Oh I've jumped out of that which I didn't mean to do. |
10:02 | Which I'm going to just jump across to that spec sheet again. |
10:06 | So you can see in, let me just get the right one. |
10:11 | So in the top here, which might be a little bit difficult for you guys to see if you're not looking at it on a computer screen is the start of the, well exactly how the part numbering system works. |
10:22 | So we've said all of the sensors in this series start with SLS130 then the first part is the electrical stroke, then it's whether you've got the short or long version. |
10:31 | So there's different packaging, different body length options for different stroke options. |
10:36 | So for a given stroke there's different packaging length options. |
10:39 | Again, that's just a case of helping you package the exact sensor for your application. |
10:44 | You've got different sealing ratings, so different IP ratings, IP stands for ingress protection. |
10:49 | So that's about understanding how much resistance it's got to water and dirt and stuff like that. |
10:55 | Obviously these are in a relatively harsh environment, they're in the outside of the car, if you're running in a wet race or running on a wet track, these things are going to have water splashed all over them and potentially getting grubby and dirty and grimy and stuff so the IP rating does become relatively important. |
11:11 | This particular sensor is actually, one of its intended uses is actually for a motorsport application so that's another good reason to go through the spec sheet to see what its intended use is as well. |
11:21 | Then we've got the second to last one there is the cable length option so a 1 or a 10 metres and then the last option there for a protective sleeve and all of these different codes, if you're not exactly sure what they mean, they're all explained in these diagrams here just to give you a little bit more context so there's a huge amount of information packed into these spec sheets and they're usually available free of charge and publicly available through the supplier. |
11:46 | There's all sorts of different places you can go to get these, whether you're going directly from the place you buy your data analysis tools from, like the places that sell you loggers and stuff like that. |
11:57 | Or motorsport electronics stores stuff like this, there's all sorts of different places you can get them. |
12:02 | But that hopefully covers a couple of the practicalities for you guys as well. |
12:06 | So I want to get onto the calibration and how we use these things. |
12:10 | So there's a couple of different things we're often interested in, we're using these for. |
12:14 | The two primary ones are talking about the travel of the damper and the other one's of the travel of the wheel. |
12:23 | So what I mean by that is sometimes, for some calculations for example, looking at damping histograms and tuning our dampers, we're going to be using, looking at it in terms of how far the damper's moving. |
12:33 | Other times when we're looking at things like roll angle calculations, or something like roll gradients, stuff like that, then that's when you're going to want to start working in terms of how far the wheel is moving. |
12:43 | In many situations you haven't got, the amount the damper moves, in almost all situations, the amount the damper's moving isn't the same as the amount the wheel is moving. |
12:55 | You've got a motion ratio between then and you usually calibrate between them but let me go back one step and just talk about the calibration of the sensor itself. |
13:03 | In fact, I've got over on my laptop screen again, forgot I had this prepared, let me just get rid of this. |
13:14 | So this is a typical calibration plot for a sensor that is mounted, in this case it's a sensor, it's actually one of these style sensors, it's a rotary style sensor where you've got an arm dropping down to a lower control arm and what we're doing here is when I say calibration is we're mapping the output voltage of this sensor to the actual amount that the damper is moving. |
13:38 | So in this situation, we're looking at this third case which I understand has probably become relatively difficult to see in this really crowded diagram but it's this case where we've got this sensor mounted to the chassis and our little arm and a drop link dropping down to the suspension and what we're mapping this to, we're mapping the voltage output to the amount that the damper is moving mechanically. |
14:00 | So the way that's normally done is that obviously this is mounted to the car and we measure the voltage change from one step to another so you might have to start with the suspension completely hanging at full droop. |
14:11 | You record the voltage, you record, you take a set of digital vernier calipers and you can measure, on some convenient place on the damper, maybe between somewhere on one of the spring platforms or somewhere on the damper body to some convenient point on the damper, essentially what we need to start with is a reference measurement for the distance between the top and bottom of the damper. |
14:31 | Doesn't matter where you measure from as long as you can measure from the same position as we move through the stroke. |
14:35 | So you record the voltage, you record the linear measurement and then you step it up in a whole lot of different steps. |
14:41 | Now typically you break this up into approximately 10, evenish steps, they don't have to be exactly even, so you start from there, you move up, you record the distance, you record the voltage and the distance, voltage and distance, voltage and distance, all the way up until your suspension is fully mechanically compressed and that's what you see on my laptop screen here is exactly that relationship. |
14:59 | So you can see we're starting from, in this case, the voltage is increasing. |
15:03 | It doesn't actually matter whether it's increasing or decreasing, we're mapping a voltage output to a physical suspension displacement. |
15:09 | So in this case we've got a voltage starting low and going high as the suspension stroke is changing. |
15:15 | So you can see here we've got, you can see the way that the voltage is mapped to the linear position. |
15:22 | Now this is using MoTeC's calibration, sorry MoTeC dash manager tool that's got a calibration for a certain car inside it and this is just looking at the front left damper pot for a given suspension setup and the nice way about plotting it here is that you can see if there's any irregularities. |
15:42 | When you write these things into a table it's very difficult if not impossible to see unless you've got really big steps or really big inconsistencies, it's very difficult to see how smooth that relationship is. |
15:52 | While we'll have a non linear relationship which is what we see because we've got this, you can see a little bit of a curve to this line here, we expect a non linear relationship because we're using all these non linear quantities. |
16:03 | We've got multiple arcs, everything's moving through in there. |
16:05 | But even though it's non linear, what we really care about is that it's smooth because being smooth means we can linearly interpolate safely between any of those points. |
16:15 | So if we map the voltage to the displacement, then no matter which voltage we have we can be confident that we've got a pretty good approximation of the displacement that we're actually measuring on the car. |
16:26 | So that's it for the electrical calibration. |
16:28 | The process is exactly the same regardless whether you're using a linear sensor or whether you're using a rotary sensor, you're always going to measure the electrical output and that's the electrical output that the dash is seeing and then you're going to relate that back in terms of mechanical travel that you're seeing in the first instance, usually at the damper itself. |
16:46 | Now we've got a way of when we log the data inside our logger, we're not going to be logging voltage, we're going to be logging a position. |
16:54 | And that's going to be a suspension position and because we've mapped it back to how much damper's moving, that's telling us, that means that we've got damper travel is what we're actually measuring, rather than wheel travel. |
17:06 | Now what we need to do next is calibrate that back to wheel travel. |
17:09 | So again there's a couple of different ways we can do that but what we're looking for is to define a mathematical relationship between how much the damper is moving and how much the wheel is changing and something like a double a arm suspension, where you've got the damper on quite a different motion ratio or moving quite a different amount to how much the wheel is moving, you're going to get quite a different relationship, it's not going to be a 1:1 ratio. |
17:33 | So what do I mean by that? Again I'm going to just do a little sketch here, so if we've got our wheel looking from the front and we've got let's say for argument's sake, we've got our control arm like this and we've got our damper, let's say for argument's sake our damper is mounted at this point here on some relatively extreme angle which you might see in some single seater, particularly older single seaters and stuff like that. |
17:59 | So let's say we've mapped our, I should say, I said this was for an extreme case but it doesn't matter, every car is going to have some different amount of motion ratio regardless of how this is laid out as in how much movement we get at the wheel versus how much movement we get at the damper and the important thing to understand about this as well is it's not, often it's not linear. |
18:22 | Usually we can, if it's close to linear we can use a constant or linear approximation to it but in many cases it's not, it's not linear and what I mean by that is the motion ratio we get when we're at one end of the travel is quite different to what we get at the other end of the travel. |
18:37 | But what we're typically doing here when we measure the motion ratio between the wheel and the damper is we're going to have the suspension at full droop and really similar to what we did when we calibrated the damper, we're going to jack the suspension up in steps so let's say that's our total suspension travel. |
18:52 | Again you can do, it depends how non linear your suspension is but if you've got a relatively non linear suspension, you'd probably want to be breaking up into let's say something like 10 equal steps. |
19:01 | What I mean by that, starting at full droop and going to full compression. |
19:05 | So we need some way of measuring some convenient part, some convenient way of measuring from the wheel, let's say our guard or our chassis' up here somewhere. |
19:12 | So we want to be measuring between here and here, giving ourselves a reference measurement starting from full droop. |
19:19 | You can do this from the hub, from the wheel, from the tyre, whatever is convenient and repeatable place for you to do this yourself. |
19:25 | So we're measuring the amount that the wheel's moving up for the amount that the damper is moving up. |
19:31 | So we are measuring this relationship between, and what you're going to end up with is a table of wheel versus damper and you're going to record the measurement at each step. |
19:41 | Now once you've got that measurement between each step you can then divide between 2 values, you're then going to end up with a difference between each value and with that difference between each value, you can work out the ratio of how much it's moving, so how much is the wheel moving, relative to how much is the damper moving? And that's what's giving us our motion ratio calculation. |
20:00 | So you'll find in lots of cases, particularly in a double wishbone or a multi link setup, the motion ratio, the amount that the damper's moving with respect to the wheel, can be really different and it can be, the damper can be moving on the order of a half to two thirds the amount the wheel's moving and that ends up making quite a big difference to your suspension frequency calculations, to your stiffness calculations, to your damping calculations, it's a really important thing to understand. |
20:25 | It's also really important to realise, the reason it's important is because we're measuring damper position but often we want to calculate the wheel position, we can do that with a math channel inside our logger like we've talked about in a previous webinar. |
20:37 | So now that we've got our motion ratio we can now write our math channel inside our logger and now we have a known relationship between how much the damper and the wheel is moving and we can go forward and use that. |
20:50 | Just as a note, there's different ways that people define, people use different conventions for this, but the convention for motion ratio I am familiar with, that I tend to use is the amount of wheel movement divided by the amount of spring movement which in the case of a coilover is just the damper, it's the same thing. |
21:11 | So the amount of motion would be the wheel divided by the amount of spring movement. |
21:16 | That's the convention that I'm used to in terms of working in motion ratio. |
21:21 | So the last thing I want to talk about in terms of the practicalities of damper potentiometers is the logging and frequency requirements. |
21:28 | So depending on what you're using your damper potentiometers for is going to depend on the logging frequency you need to use. |
21:35 | For most applications, certainly most club level applications, if you're using damper potentiometers, they're probably going to be the highest or one of the, if not the highest logged frequencies used. |
21:46 | So in our data, both of our data courses, we give some guides for the suggested logging frequencies you should be using for each sensor and these are normally in the range of 1 to 10 to 20 to 50 Hz depending on for most applications whether you're talking about things like steering and brake and RPM and stuff like this. |
22:06 | When it comes to damper potentiometers, normally you're in the 250 to 1000 Hz so that's in the 250 to 1000 times a second is how often the logger is recording a value out of the damper potentiometer. |
22:19 | Now depending on what you're using it for depends on which end of that scale you need to be looking at. |
22:23 | So if you're just using your damper potentiometers to work out things like roll angles and how much the suspension is heaving, so how much the car is diving in the brakes and squatting under acceleration, rolling in the corners, you can get away with a much lower logging frequency, you can get away with something down to even the 20 to 50 Hz range, that's fine for getting these sorts of movements because these large sprung mass movements are happening relatively slowly in terms of a logging rate like 20 to 50 Hz. |
22:51 | If you're using it for damper calculations or damping force or sorry damper histograms, that's when you need to be bumping this up. |
22:57 | Essentially what we're doing when we're doing damper histograms or damper velocity histograms, we have to take a calculation based off the position signal. |
23:07 | We're doing a mathematical process to that called a differentiation to calculate the velocity from it. |
23:14 | That's why we end up needing to have such a fast logging frequency. |
23:17 | I'll just sketch out something just to make that point really clear what I mean by that. |
23:22 | So just on the overhead here, if we've got, let's say we've got our, this is our front left damper potentiometer. |
23:29 | So let's say our signal is something changing really fast like this, got all these thousands of little points here. |
23:37 | When we're doing a differentiation, when we're doing a speed calculation from a position, so we're taking the mathematical process we're doing, we're taking position and we're calculating velocity with it. |
23:48 | Now what we're doing with that is taking the change in distance divided by the change in time. |
23:56 | What this means in practical terms is if we've got some signal that's changing like this, is we're doing a slope calculation between them so let's say these are the log data points that are actually recorded by the logger, whatever frequency we're using, we're taking, if we're looking over a time scale in this direction, and this is a distance scale in this direction, we're taking the slope between each one of these points and the slope which is the rise over the run, what I mean by that is this, slope is the rise over the run. |
24:32 | If you guys remember, if you used those terms when you guys learned your, in math class when you were at school, so that's the slope and the magnitude of that slope, which is calculated as rise over run. |
24:46 | Is the instantaneous velocity at that point, or at least the calculation or an approximation of the instantaneous velocity at that point. |
24:52 | Obviously our damper potentiometer, this is not measuring velocity, this is measuring position and we're doing a velocity calculation from this position which means we're doing a differentiation which is what essentially why we need these points to be close together because as you can imagine, if let's say I was logging the damper position at this frequency, a relatively coarse frequency, these are the calculations I would end up with with my rise over run which is going to be nothing close to reality, it's not going to, it's completely missing what's happening with the damper from a velocity perspective. |
25:28 | From a position perspective if you log it high enough in the like I said, 20 to 50 Hz range, it's going to be fine, you're going to get a relatively good reading for how much travel from a low frequency perspective you're moving but if you want to pick up the instantaneous velocities which is what dampers are so sensitive to the velocity that they're moving, not their position. |
25:50 | Then we really need to be, if you can see here, you really want to be logging a much much much finer frequency and that means because these dots are now so much closer together, the instantaneous slope calculation that we're doing all the way along here is going to be much much more accurate. |
26:07 | So hopefully that explains a little bit about why you want to use a much higher frequency when it comes to damper potentiometers, particularly if you're interested in doing damper histograms or damper speed calculations to understand your damping forces. |
26:22 | That is a point to mention as well is some I'd say more entry level loggers may not be capable of logging at such high frequencies so if doing damping calculations is important to you, that's something to consider when it comes time to buying a logger, you want to make sure that whatever you're buying has the ability to log high enough. |
26:39 | I would say absolute bare minimum you can get away with, and this does depend on your application, if you're running a really smooth racetracks and without a lot of curbs and stuff like this or just generally it's quite smooth, 250 Hz is going to be fine, if you're running on really rough surfaces or you're doing off roading or rallying, you're going to need to be going into a relatively high logging frequency. |
26:59 | So you're probably thinking more in the 500 to 1000 Hz range. |
27:02 | If it was a circuit car, even if I was running on smooth surfaces and I had the option, I would always be running them at 1000 Hz 'cause it means I know I'm always going to have a really good quality calculation. |
27:12 | Now the downside with running those really high frequencies is that it's going to take up much more logging memory, it's going to make your log files bigger and more cumbersome to real with, it's going to make the computer slower when you're doing a lot of calculations on it so you do need to balance this. |
27:24 | I'd say bare minimum, 250 Hz for dampers, up to 1000 Hz and 1000 Hz will generally be just fine for getting it done. |
27:32 | So guys, if you've got any questions about anything, about what we talked today, about setting up or selecting damper potentiometers or anything generally to do with data analysis, race engineering or any questions you've got, you're welcome to chuck them through now and I will come back and look at those in a second. |
27:46 | There's just one last thing I wanted to talk about, I just wanted to show you guys some actual damper data that I've got up on here on my screen, so if we jump across to my laptop screen. |
27:54 | So this is some raw damping data from a touring car. |
27:59 | You can see I've got, what I've got plotted here is speed at the top, I've got my 3 G forces plotted here, so lat, long and vertical G forces. |
28:08 | And then I've just got the raw damper position data. |
28:11 | So in this case, this is the amount that the actual dampers themselves are moving, not the wheel positions. |
28:17 | So you can see, you've got stuff that's happening, it's changing really quite violently throughout a lap. |
28:23 | You can see it's really important to have, you can see if we weren't logging at a really high frequency, we would be getting, missing all of these really high frequency noise which is really important when it comes to doing damping calculations. |
28:37 | You can see here when I press, so I'm using MoTeC's i2, when I press S, it turns the lines into points so you can actually see the density of the points with each other. |
28:45 | So you can see there it's doing a pretty good job of capturing the actual physics of what's going on with the way the damper's moving. |
28:51 | So here we're looking at the raw damper position, I'm looking at the front left and the front right and the rear left and the rear right damper positions. |
28:58 | So the general shape of what's going on here, the calculation, sorry the convention that we're using here is when the damper gets shorter or when it's compressing, the numbers get larger and when it's extending, the numbers get smaller. |
29:10 | So here you can see the car, at the start of the lap this car's coming into turn one, hitting a braking zone, you've got the front dampers compressing and you've got the rear dampers extending so that's what's happening here, you're going from the car's cruising along a straight hit the brakes, the front's compressed, the rear extends and then as you move through the lap, as you get into, let's say we're in a mid corner at this part of the track here, you can see you've got a differential so we can see, we're turning right here and I can tell that we're turning right because the front left damper is more compressed than the front right as is the rear left and the rear right so we can see the left side of the car's loaded up so we know we're turning right. |
29:45 | So that's generally what the raw damper data itself looks like when you log it. |
29:49 | So what we can do straight away is we can post process that into velocity. |
29:55 | So here I've got a velocity calculation going on where we're doing a differentiation I was talking about before. |
30:00 | Automatically inside the analysis software so it's taking that position data and calculating the velocity at each point. |
30:06 | So we can see quite quickly throughout the lap where our peak velocities are happening on track. |
30:12 | These will be positions where we've got big bumps or big curbs where the car's hitting a lot of curb as it's taking a corner. |
30:17 | And this velocity is what we're typically using when we're tuning our dampers because the damper speed ranges that we are within, define the force characteristics that we've got within the damper so the next display I've got here is what we call a histogram which some of you might be more familiar looking at it in a different format so I'll just change this back over from line to bar format because it's probably what most people are used to looking at. |
30:42 | So the idea here is that we are looking at, we've got a percentage on the Y axis, we're looking at each corner of the car, there's a front left, front right, rear left, rear right, we've got a percentage scale on the Y and we've got damper speed along the X axis so in the middle of the X axis here down here, is 0 for both of them. |
31:02 | So you can see the X axis at the bottom here applies to both of them. |
31:06 | So that's 0 damper velocity and to the right as in down here, we can see that we are getting, this is positive velocity, it's getting greater so it's low velocities in the centre, going to higher velocities at the outside, the right hand side of the plots is compression, left hand side of the plot is rebound in this particular example. |
31:24 | It doesn't matter which way it works, you've just got to tell the software which direction the dampers are moving and it'll plot it automatically for you. |
31:30 | So the reason that's so important is because we can see, because if we can see how much of a lap each damper is spending at each speed range, we can get an idea for how bias the damping is between low speed and high speed and that's what's going on here, we can see in this case, we've got in the low speed range, in the central range, we can see we've got some amount of low speed bias, in this section anyway, towards rebound compared to compression, It's something quite symmetrical, it's happening on the front we've got a little bit of very low speed bias compared to in rebound compared to compression. |
32:03 | Now this is the stuff I'll go through in much more detail, we'll get right into the nitty gritty of more detailed damper analysis in an upcoming webinar when I really want to dive into the data itself. |
32:13 | But hopefully that's given you guys a bit of an introduction and some useful tips and understanding of how to choose your potentiometers, different types and some of the important practical considerations that go with it. |
32:24 | So guys that's it for the lesson, I'm going to jump across now to the questions and I'll see if we have any questions that have come through that I can jump onto for you guys. |
32:36 | It looks like no questions at all so either that was a fantastic lesson or maybe there's actually no one out there watching this live, I'm not sure. |
32:43 | But either way guys if you do have questions that come up I know there'll be lots of you guys that will be watching this after the fact when you watch it in our archive. |
32:52 | If you do have questions that come up either with selecting these things or setting them up or calibrating them on your car, you know you can go to the forum and ask the questions there so I look forward to seeing you guys around the forum and you guys hitting me up with those questions to make sure you guys are getting the most out of your potentiometers in your car. |
33:09 | Thanks very much guys, I will see you in the next member's webinar coming up soon, cheers. |
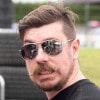