316 | Working With Heat-Molded Boots
Summary
Molded boots and transitions are an important part of professional motorsport harness construction. In this webinar we’ll learn what these are, how to select a suitable boot, how to recover them correctly and how to seal them with epoxy.
00:00 | - Hey team, Andre from High Performance Academy, welcome along to another one of our webinars and in this one we're going to be dealing with heat molded boots, heat molded parts, something that we will be dealing with a lot, particularly at the professional level of motorsport wiring. |
00:15 | Exhibit A here is our little test harness and I'll just get this under our overhead camera. |
00:21 | I'm going to assume it's probably a safe assumption that most people have already seen these heat molded boots before but for those who haven't, if you have been living under a rock, that's essentially what we're going to be talking about. |
00:34 | Now as usual, if you do have any questions, as we move through today's webinar, you can ask those questions in the chat and we'll deal with those at the end. |
00:44 | So let's get started with what a heat molded boot is or heat molded part and why we would need them. |
00:51 | So essentially they're a semi rigid boot that we can heat shrink down using a controlled temperature from a heat gun like this Dewalt one that I've got here. |
01:02 | And I'll just get this out of the way, they come in a range of different shapes and sizes so in this case in our overhead here, we've got a T intersection heat molded boot which is a really common way of branching out our wiring harnesses. |
01:18 | Particularly if we've got a V configuration engine and we want to run the harness down both banks of the engine, maybe for our injectors etc, then a T boot is a really nice way of making that transition. |
01:30 | We've also got straight boots like this one here, obviously this one is a little bit smaller, they come in a range of sizes. |
01:39 | We've got all sorts of different shapes and I'm only scratching the surface here on what is available. |
01:47 | This particular one here is from Hellermann and this is one that I actually used on our FJ40 wiring harness which has just been added in as a worked example to our pro wiring course. |
01:58 | And this is being used in the injector and ignition coil wiring harness. |
02:03 | So essentially that harness, the main branch runs along one of the fuel rails on each side. |
02:08 | And then at each point we can branch out the wiring for our injectors and our coils. |
02:14 | So it kind of gets everything nice and neatly arranged and heading in the right direction. |
02:19 | Unrecovered, they tend to look a little bit more like this. |
02:24 | So we'll get this under our overhead as well. |
02:26 | This one here is a 90° boot so we would use this on the likes of the back of an autosport connector. |
02:32 | So we can see that in their stock form they are actually reasonably flexible. |
02:36 | But if we look at one of these recovered parts, I mean I can't budge that, it is absolutely solid. |
02:43 | And that really comes down to two of the points of why we would use these heat molded boots in the first place. |
02:50 | One is that they do a great job of sealing our harness from the environment. |
02:55 | So they're going to prevent dust and moisture ingress into our harness when they're installed properly and when they are sealed with a epoxy glue. |
03:05 | The other element though that's just as important is that they provide really good strain relief to our harness when they are recovered down because they are essentially semi rigid. |
03:16 | So if we get our harness back into our shot here and we can see that harness, I cannot move that. |
03:25 | So obviously in behind this boot, we've got all of our service loops anyway. |
03:30 | So that's helping with our strain relief but there's likely to also be a number of crimps and splices, splices is what I meant to say, in there, so this is probably the most dangerous part of our harness in terms of reliability so having that heat molded part in there, it is glued to the DR25 of our main harness, it is also glued to the back of the autosport connector here and basically then protects our harness from any strain being placed into the contacts at the back of that autosort connector. |
04:03 | There's a couple of suppliers, the main suppliers in this market, Raychem and Hellermann. |
04:08 | The parts, for all intents and purposes, at least as I've experienced them, are interchangeable. |
04:14 | Part numbers are different between Hellermann and Raychem but essentially it's going to come down, in terms of preference it's going to come down to the supplier that you have access to and what they're actually stocking. |
04:28 | So the parts are interchangeable, there is a cross reference between a Hellermann and Raychem part so not a real big deal there using one or the other. |
04:39 | We tend to end up with a bit of a combination of both just depending on what we can get access to. |
04:45 | Now what I'll do is just bring into shot as well a couple of other examples here. |
04:53 | So the heat moulded parts are not the only way of dealing with environmentally protecting our harness. |
05:01 | So this DTM 4 pin connector here has actually been sealed with a section of SCL heat shrink. |
05:07 | So similar in some regards in terms of its a semi rigid product so obviously not a lot of flexibility in there. |
05:17 | It's doing the same job in so much as it's sealing the harness from dust and moisture and that is also a glue lined heat shrink as well so basically when you shrink down SCL, it will have a bit of a black epoxy ooze out, that's pretty typical. |
05:34 | Problem with SCL is that it is a straight heat moulded heat shrink so it gets difficult again in our example here, we've obviously gone from quite a large diameter down to quite a small diameter. |
05:49 | It's not so bad with our little 2 pin here, you can see the difference in diameters are not quite so dramatic but it can get a little bit tricky with the SCL. |
05:59 | In order to get that to shrink down to the smaller diameter, so often you'll see people using 2 lengths of SCL, one is just going to be shrunk down directly onto the DR25 to essentially create a little bit more bulk so that the second piece that fits over the back of the DTM connector can then shrink down onto it. |
06:19 | There's a few little oddities like that whereas the heat moulded parts from TE Connectivity, Raychem and Hellermann are actually designed to actually shrink down into different sizes at their inlet and their outlet so that's why if we again get our little sample under the overhead, we can see that we've got a dramatically different diameter at the large side compared to at the small side and we can size these to suit our harness requirements. |
06:52 | Now before we get into sizing, also talk about glue versus non glued boots. |
07:01 | They are available in both forms and really a lot of this comes down to personal preference. |
07:06 | Let me just get this one under the overhead. |
07:10 | It might be a little tricky to see, no actually I don't think it's too tricky to see at all. |
07:14 | This sort of grey finish that we can see in here, this is actually a glue lined heat shrink boot so this glue here is pre applied to the inside of the heat moulded boot and when we recover that down using our heat gun that's actually going to essentially melt and can be used them to glue that boot down to whatever we are recovering it onto. |
07:38 | So that's one option, the other option is non glue lined and this one here is a good example of this. |
07:46 | So we can see, nothing in this, it is just purely a heat moulded boot and we're going to need to apply our own glue to that. |
07:56 | So pros and cons with this, using a non glue lined boot allows us a little bit more control over the application of the epoxy and what we're going to use. |
08:09 | Obviously it is a bit of a messier process and it does involve another step and some more consumables so there is that to consider. |
08:17 | Either will work, generally I prefer to work with non glue lined boots but that is partly a personal preference here. |
08:26 | If we are working with non glue lined boots then you are going to need an epoxy. |
08:32 | There are two options that are sort of the industry standard, this is the Hellermann Tyton V9500. |
08:39 | The other one is the ResinTech RT125. |
08:43 | I haven't been able to find a difference between them, I'd suspect they're actually exactly the same product but I can't guarantee that. |
08:52 | As its name implies, it is a 2 part epoxy, you use a mixing gun like this. |
08:57 | There are a couple of options for application. |
08:59 | You can get a mixing nozzle, so that has essentially a spiral pass through it, it is quite long, probably sort of a good 75 mm in length, 3 inches in length or thereabouts. |
09:12 | And basically by the time the 2 parts of the epoxy have gone through that spiral, they've been properly mixed together and when they come out, you can be comfortable in knowing that they are mixed as they should be. |
09:24 | I find particularly when we're only using a small amount of epoxy though for maybe gluing just one boot down, that's a really wasteful way of using what is quite an expensive product. |
09:36 | I tend to use this without the mixing nozzle and what I'll do is apply the amount of epoxy that I think I'm going to use onto something that I can physically mix with a spatula or something of that nature and then what I do is I use a small syringe like this. |
09:57 | I'll get this under our overhead so you can get a better shot of it. |
10:00 | I mean nothing particularly special here, this is just a 5 mL syringe. |
10:03 | They will come like this and these are probably $1 or $2 at your local pharmacy or drug store. |
10:11 | So all you need to do is remove the plunger from it, you can load your epoxy into there and then that gives you a lot more control over how it's going to be applied. |
10:21 | I do however also use these little extensions here, I guess it's kind of a needle. |
10:29 | Relatively small point and it allows you really precise application of the epoxy to the inside of the boot or to the back of a autosport connector or wherever you're applying it. |
10:40 | Little trick when you are using a syringe like this, the epoxy can be quite thick. |
10:47 | Particularly if you're in a colder climate, maybe coming into winter. |
10:50 | So what I find is a really good idea just before you go and apply the epoxy, I use my heat gun and just lightly heat the epoxy in the syringe. |
11:00 | That just allows it to flow a little bit better. |
11:03 | Do need to be a little bit mindful if you're doing that though, obviously that can result in the epoxy setting up a little bit faster. |
11:10 | In general I've never found that to be an issue because these epoxies really need a good 24 hours to properly cure so not too much of a concern. |
11:20 | Now that is the process but I won't be demonstrating, that's what we're trying to do but I won't be demonstrating the full process with the epoxy just because it does tend to get a little bit messy, particularly when we're trying to do this on camera. |
11:35 | Alright so talking about sizing, the key with any of these heat molded parts is making sure that they are the correct size and they do come in a range of sizes. |
11:47 | I haven't got the right one for this autosport connector but one of the nice features with these is that when you have got the correct boot size, it will actually go over the autosport connector so you don't have to assemble these onto your harness as you're building it. |
12:04 | As I've said, this one is not the correct size, it is a little bit too small but yeah if you've got the right one, you'll actually be able to feed this over the autosport connector once the harness is built and shrink it into place. |
12:15 | That's also handy because if you do ever need to cut that boot off, you can install another one without having to depin the entire autosport connector and start from scratch. |
12:25 | So it's a fine, relatively fine line between a boot that's too big and a boot that's too small. |
12:31 | These do have a really high shrink ratio so they're actually going to shrink down a lot more than you think. |
12:39 | And the other element which can be a little bit surprising, we'll get this one under our overhead, I'm going to demonstrate shrinking this one down but as it shrinks, what they're going to do is actually grow in length as well. |
12:53 | So when you're getting some of these boots and you're sort of looking at them compared to the junction that you may be shrinking them over, it can be hard to believe that they're actually going to shrink out and cover the entire section of your harness but you will be quite surprised. |
13:10 | You don't need to guess though because there is a wide range of information available from TE on exactly what these are going to do. |
13:20 | So first of all, let's jump across to my laptop screen, this is a resource that we include in our practical motorsport harness construction course. |
13:27 | You'll be able to find this by searching TE Connectivity molded parts. |
13:32 | It is a pretty extensive list of all of the parts and part numbers that they offer and as I scroll through this, you can sort of get an understanding of the wide variation in shapes that they do offer. |
13:45 | What I would say as well though is depending where you are in the world and who your suppliers are, just because you can find a shape or a part that will suit your application, let's say this crazy looking thing here which branches off in 4 different directions, you may not be able to find that locally so this could end up being difficult or you may need to import it from a supplier overseas so it's always a good idea to really think about these things as you're doing the construction plan for your harness so that if you do need any peculiar boots that you can actually order these in ahead of time so if there's a delay on them, it's not going to affect your harness construction. |
14:28 | I would say, at least in my experience here in New Zealand, all of the conventional straight and 90° boots like this one here that we use on the back of the autosport connectors, there's never really an issue with those. |
14:41 | The little angled boot that I showed for our injector and ignition wiring I did have to get these in from overseas but again depends who your supplier is and what they're using. |
14:52 | There's also a really good breakdown on the part numbering for the Raychem boots so you actually understand what these numbers mean. |
15:03 | The next element that I want to talk about, oh no we'll talk about sizing still. |
15:07 | So that's the main catalog, again I'm not going to go through all of it. |
15:10 | Then it comes down to sizing. |
15:15 | So let's talk about a pretty conventional straight boot which would be like this little one here. |
15:22 | And we want to know what size or what boot part number we need to order. |
15:26 | So this is another one of the resources from Raychem for their boots. |
15:32 | Hellermann have their own. |
15:34 | But this gives you a really good rundown on exactly what's what. |
15:37 | So first of all we have the boot in its unrecovered form here. |
15:41 | Really important, particularly when we start dealing with some of the more intricate shapes like the T boots, to make sure we understand the letters on each of the ends of the boot. |
15:56 | So let's get this under our overhead. |
15:58 | And might be a little bit tricky to see but what we've got here, this side here is J, this side is H and this side is K. |
16:09 | And when you've got this unrecovered, and unfortunately I don't have one here that I can show you, it actually looks like it's a straight through boot so it's important to know once it's recovered, which of the legs is going to actually transition through 90°, otherwise you could end up creating a bit of an issue for yourself if you recover it down and you find that you've actually got your harness in the wrong leg of that particular boot. |
16:32 | So in this instance though, what we can see is H, that is the inlet when it recovers down that becomes the biggest side and J is our outlet and when that is recovered down, that's the one that's going to shrink down like this. |
16:49 | When you are holding these it does become pretty apparent, the H side obviously it is labelled but that is a bit thicker in the material, it's a bit stiffer whereas if we get the J side, that one is much much thinner, much more pliable because that's the side that is designed to actually shrink down in that bottle shape. |
17:10 | We've got all of the dimensions though for each of the parts. |
17:13 | So our recovered and unrecovered size is for our H so for example here if we're looking at a 202K121, the unrecovered size for the H is 24 mm and when it is recovered down, the minimum size it'll recover down to is 10.4 mm. |
17:35 | So it goes from 24 down to 10 mm so it is a massive shrink ratio, a fairly significant shrink ratio. |
17:42 | So what you want to do in this instance here is essentially measure whatever you're shrinking that down onto. |
17:48 | So let's say we've got our autosport connector. |
17:50 | We're going to be measuring the outside diameter of the section it's going to shrink down on and that's going to give us a guide. |
17:58 | Obviously when we're choosing the correct boot for this, we want to make sure that we're choosing a boot where that size falls within that minimum and maximum range. |
18:08 | However it's not just the back of our connector we need to consider. |
18:11 | Obviously the wiring that comes out of the connector, we also need the diameter of that wiring and that becomes our J diameter, this one here and our J diameter is listed here, again minimum and maximum so we can see what that's going to be. |
18:29 | So for that 202K121, the inlet, the H leg will shrink down to 10.4 mm, the J leg starts at the same 24 mm, that'll shrink all the way down to 5.6 mm. |
18:43 | So within this range, you're probably going to be able to find a boot that's going to be able to suit most of the common applications you'd need them for. |
18:53 | We've got another resource in our practical motorsport level wiring course that lists the correct boot size for the common shell sizes for the autosport connectors. |
19:03 | These documents that you've just seen here, these also exist for the T boots and I've got this one here for our 90° boots. |
19:14 | Now a little tip that I would give as well is that when you are terminating the back of an autosport connector, particularly ones where it's getting a little bit busy, maybe you've got a bunch of splices going on there. |
19:28 | It's really a good idea to print out and scale the drawing from TE Connectivity like this, or Hellermann for that matter and scale it out so it suits the finished size of your connector and then use that essentially as a silhouette, you can cut it out and you can use it as a silhouette when you are locating all of your splices to make sure that they are going to nicely sit within the finished recovered boot space. |
19:58 | Otherwise you're going to end up with something that's going to be a little bit messy to work with and probably just not look that aesthetically pleasing when it's finished. |
20:08 | So that's the process of sizing it, going through those documents and again you'll find all of these if you just search for them. |
20:15 | If you are looking at a boot number, if you search that particular boot number, you're going to end up getting to this document that I've just shown you here, not very difficult. |
20:25 | The other element to consider with these is that these boots are available in lipped or non lipped variants. |
20:34 | And what that refers to is the end, or the H end here, if you are going to be using this in conjunction with an autosport connector, then if we get this one under our overhead, what you'll see is that we've got this gnurled section here and then it actually steps down and we've got a lip in here so the lip on the boot is designed to actually lock in behind that gnurling so we do want to use a lipped variant when we are using autosport connectors however, not always do we want to do that. |
21:10 | Let's just get our harness under our overhead and this is where we've used a raychem boot for a transition from our harness, obviously we've got 2 branches coming in here and we've got several coming out and in this instance obviously we don't need the lipped variant so just depending on your application whether or not you want to use the lipped variant. |
21:35 | Alright so I'm going to try a couple of demonstrations here and hopefully everything works out really nicely. |
21:41 | We'll see how that all goes and the first of those we're going to look at applying a heat moulded boot to this potted ignition coil. |
21:51 | Little bit of a back story, this is a Toyota ignition coil, these have a known problem with the pin retention, contact retention on the factory connector. |
22:03 | So they're fine in a road car application until they get very high in the mileage but with the vibration associated with motorsport use, they can be problematic. We had these coils on a 1ZZ-FE that was on our engine dyno and we potted them to give us a little bit more reliability. |
22:22 | So once we've potted them we can essentially leave them like this, I'll get it under our overhead and we can see that essentially the wires have been soldered directly to the terminals inside here and then once that's done, to provide some mechanical strain relief, it's been back filled with a 2 pot epoxy, our ResinTech RT125. |
22:42 | So we could leave it like this, it is environmentally sealed but what we want to do is provide a little bit more strain relief as well. |
22:49 | It is possible to have that solder essentially wick up the conductor strands and make its way further up into the wires which is really the problem with solder. |
22:57 | So a heat molded boot is a really nice way of sort of finishing that off and adding reliability. |
23:05 | So the boot that we've actually got, this is a raychem boot, it is, for those who are interested, a 202D932, slightly more unusual shape in that it is already quite reduced but we do need that due to the difference in the size of the plastic section for the connector body and obviously we've only got three 20 gauge tefzel wires coming out of that with some DR25 over the top of it. |
23:38 | So we'll have a look at this in a second, I haven't at this stage talked about what you're going to need in order to recover these boots in too much detail. |
23:47 | We're going to need a good quality heat gun and you're going to need one where you can actually control the temperature. |
23:55 | So I'll get this hopefully under our overhead, that's probably not ideal but we can see we've got a screen there. |
24:02 | I'll just turn this on and our screen, there we go, lights up and we can control the temperature. |
24:11 | So at the moment we definitely don't want that to be at 500°C+ so for our heat molded boot recovery, we want to be, there will be a guide for each of the manufacturer's boots and we want to be making sure we follow that guide. |
24:29 | Generally somewhere in the 250, maybe 275°C vicinity is about right. |
24:36 | Now there's a couple of reasons why we want to be very careful with that temperature. |
24:41 | The first of these is that if we use too much heat, we can end up damaging the heat molded part, we can damage the connector body beneath that and we can end up damaging our wiring so obviously not really a lot of good's going to come out of that. |
24:55 | The other element there though is that we can actually end up completely melting the boot if we're not too careful and we can end up with that boot recovering too fast for us to be able to actually manipulate it, control it and get it in the right position. |
25:12 | These can be quite tricky, particularly as we get into the more complex T molded boots. |
25:18 | And getting everything to align in the right spot and basically manipulating it as it's starting to shrink, that can be a pretty tricky job so if you are using too much temperature, the boot is going to recover very quickly and you can find that you've got a bit of a mess on your hands because it's recovered before you can really get it properly into location so lower temperature gives you just a little bit more time to work with that and makes your life a little bit easier. |
25:45 | The other thing we're going to need in order to work with this or at least I recommend it is a pair of gloves or at least a glove on the hand you're going to be working with. |
25:53 | Hot things are in fact quite hot and you can end up burning yourself if you're not careful. |
25:59 | And there's nothing worse than having a boot that you know needs to be repositioned or moved but it's also absolutely stinking hot and when you touch it, it burns you so a glove is a really good way of getting around that. |
26:12 | Couple of other elements that we will need, before we apply our heat molded part, we are going to need to abrade the DR25 around it and we're going to want to just rough that surface up a little bit so it gives something for that glue to really bite into. |
26:30 | So just some emory paper, doesn't need to be too rough. |
26:34 | I'll just rip a little bit off there and we'll get our ignition coil back under our overhead and do it under here. |
26:42 | So we can kind of get a sense for where this boot is going to recover down and what we want to do is just gently abrade the surface of the DR25 and if you are using a transition on your harness and it's not actually going onto an autosport connector or the like, you want to abrade all of the DR25 on both sides of the boot, the inlet and the outlet. |
27:06 | Right so that's abraded down enough now and what we also want to do is use some isopropyl alcohol and just clean back that surface as well as the back of the connector body. |
27:20 | So I've just got a bit of isopropyl alcohol in a squirty bottle here and we'll just go ahead and clean that down so not exactly rocket science, basically just make sure particularly on the connector body that we've removed any oils, anything that's going to prevent the boot from sticking. |
27:38 | Not a bad idea to abrade the back of that connector, plastic housing as well just to allow a little bit better grip so I'll get this back into our little vice here and we'l get this a little bit more central so we can see what's going on. |
27:55 | So what I'm going to do is just turn my heat gun on and allow that to warm up and we'll just gently get this located. |
28:04 | This one should be reasonably easy and what we're going to do is we're going to start by shrinking down the inlet and this will allow us to correctly position this as we're going and what I want to do is continuously move the heat gun around so that I'm not shrinking it down, or concentrating the heat for too long in one particular area. |
28:23 | And obviously with the heat as well, again we want to concentrate on a sensitive product like an ignition coil, making sure that we're not heating the coil itself too much so let's grab this glove here, get that on and we'll start shrinking that down. |
28:39 | So again I'll just check my temperature which has for some reason again reverted to 600°C which probably wouldn't end too well. |
28:48 | Alright so at the moment I don't really need to start by touching the boot and we're just going to focus our heat around the outside here, constantly moving. |
29:02 | And what we'll find is to start with, it doesn't really seem like too much is happening but as we start building up a bit more heat into that boot, we will start to find that it will shrink down. |
29:17 | So it's just starting to move now and the other thing I will mention as well is it's quite important to have a fairly narrow tip in your heat gun for this process just so that you don't end up sort of overheating something that you don't want to that's kind of in the path of the heat gun. |
29:37 | Alright so it is starting to move, I promise. |
29:39 | I might actually pull this up a little bit in terms of temperature. |
29:43 | Generally sort of between 250 and up to 300°. |
29:47 | 300° you'll find is a little bit higher than will be recommended in the literature but I have found over time that a little bit more heat than is recommended actually seems to be required in some instances like this one and it doesn't do any damage as long as you're again not concentrating that heat in one place for too long. |
30:11 | So we are just getting this to start shrinking now and this is the point where as it's starting to shrink down, you do want to start just manipulating the positioning of the boot, making sure that we have got it in the right spot, looking pretty good at the moment so I'll just continue going around here. |
30:36 | And I've started obviously right at that lip, right at the entrance and now as it's starting to shrink down, I am just bringing my heat gun back out to start applying heat to the remainder of that boot as well and we want to just basically slowly but surely work our way out. |
31:03 | And I must admit, it does take an absolute eternity when you're trying to do this for a webinar vs when you're actually doing it and you're building a harness. |
31:13 | This thing always seems to go really really quickly, much quicker than you want it to when you are shrinking it down onto a harness but now that I'm doing it for a live webinar, it is taking its sweet time but bear with us because we will get there, it's almost there. |
31:31 | But again the really important point here is not to concentrate the heat in one place for too long, keep it moving, keep working your way around. |
31:43 | And then keep working your way from the inlet side of the boot to the outlet side. |
31:50 | I'm actually just going to give it a little bit more heat again for the purposes of our webinar here so that we're not here for the next half an hour 'cause I'm sure everyone else has places to be and things to do as well. |
32:02 | Alright so we're just getting down to the outlet now and this is where positioning the wiring as well becomes a little bit important because we do have flexibility in this until it actually cools down and once it's cooled down, everything's going to essentially be stuck in the location that we've got it so we want to make sure that we've got our wiring coming out at the right angle, that we haven't applied any undue stress and strain to that. |
32:34 | Once we've got everything shrunk down and we're happy with it, we also just want to spend a little bit of time basically going over the whole boot and applying a little bit more heat and just making sure that everything is fully recovered. |
32:48 | I'm going to leave it there, it does actually require a little bit more time than that but I'm sure at this point you basically can get the jist of the process that is required. |
32:56 | Obviously it can end up being hot when we remove it from our vice as well so little bit of care is required in how we deal with that. |
33:04 | So even now, there's still a little bit of flexibility left in that but it is starting to set up. |
33:10 | We'll get this under our overhead shot and we can see again this does require a little bit more heat because it hasn't fully recovered here but all that is is just a case of time. |
33:21 | Now I'll just go back over those temperature settings as well because as I mentioned, sort of 250 to a maximum of 300, that's about as much heat as I would recommend. |
33:32 | I have punched that up just a little bit for the purposes of our demonstration just to save us a little bit of time. |
33:37 | But you will be thankful of that lower temperature when you're actually doing this because everything does happen really quickly, particularly with the thinner conventional boots, this one is a little bit unique in the shape that we've got but these ones will shrink reasonably quickly which we'll see in our second demonstration in a moment. |
33:57 | I promise this one will go a little bit more smoothly. |
34:00 | Before we do that though, I will mention that if you've got any questions, now's a great time to ask them. |
34:07 | Once we've got through this second demonstration we'll jump into those. |
34:09 | So for our second demonstration, I've prepared a little 2 pin DTM connector just with two 22 gauge wires crimped into it. |
34:20 | Now if you are working with DTM connectors and you want to boot them, you will need to make sure that you are purchasing the DTM connectors that have this little modification here with a lip for a heat molded boot. |
34:36 | That's really important. |
34:38 | Now on the heat front as well with these, these are probably one of the connector bodies that you will really notice if you are using excessive heat because it is quite easy to overheat the connector body and it will end up melting so care is required there. |
34:54 | The boot that we will be using here is this little Hellermann one. |
34:59 | Again the process is exactly the same as what we've just seen, we need to start by abrading the DR25 and making sure everything is nice and clean so we will go ahead and do that now. |
35:11 | Not particularly tricky, this is an area that a lot of people overlook but it is really important because otherwise that epoxy, that glue really has nothing to get a good grip or bite into. |
35:26 | So once we've done that, again a little bit of our IPA and then we can just clean that down on the DR25 as well as cleaning the back of the connector body. |
35:40 | Now this particular boot that I am using here is not glue lined and normally again we would be applying our epoxy onto this as we go and for simplicity and cleanliness I'm not going to but you'll be able to sort of understand that process anyway. |
35:59 | So we'll just get the boot installed. |
36:03 | Now these are ones actually I will mention as well where you do need to be careful because the shape of this, it will not fit over the DTM connector which is obviously, get that back out, it's pretty apparent, it's not going to go. |
36:17 | So you're going to need to think ahead when you are assembling the harness here and actually feed these on before you terminate and pin out the connector bodies, otherwise you're not going to get them on. |
36:28 | So we'll get this connector body back into our little vice here. |
36:32 | We'll turn our heat gun on and again make sure that it hasn't actually just jumped back up to 600° which it hasn't I don't think. |
36:45 | Right so I'll get my glove on here and again we're going to start by just working our way around the connector body itself trying to make sure that we are targeting just the inlet end of the boot and this one is already starting to shrink down so it's responding a little bit quicker than the last boot and here I'm just actually rotating the boot rather than the heat gun and we want to make sure that as that shrinks down we've got it located nicely on the lipped area at the back of the DTM connector. |
37:30 | So again our heat gun temperature is giving me enough time to work with this. |
37:34 | It's shrunk down enough now that it's sitting on the connector body without me needing to sort of manipulate it. |
37:41 | So I'm just going to work my way around here. |
37:47 | And now that we've got the heat moulded boot shrunk down nicely onto the connector body, let's get some heat around the underside of it as well. |
37:56 | Now I'm just going to work my way out a little bit further and we'll start to see the outlet end of that boot start to shrink down as well. |
38:05 | So it's a case of working our way from the inlet to the outlet slowly allowing the boot to properly recover. |
38:18 | And we're almost there. |
38:29 | Well one out of two demonstrations that went pretty smoothly. |
38:32 | So that one has shrunk down quite nicely. |
38:34 | Let's just get it under our overhead and we'll have a look at the finished result. |
38:39 | So at this point it is still nice and soft so this is a point where if we've got our wiring coming off at an angle like this and we leave it like that, that's how it's going to set up so we want to make sure we've got everything manipulated so it's in the right spot. |
38:53 | At this point we can also move the boot still a little bit and make sure that it is in exactly the right position but essentially job done there and we just need to allow that to cool down and it's ready for installation so nice way, albeit slightly more expensive way than using SCL, of finishing off our connections, waterproofing or moisture proofing our harness and protecting it from our dirt and dust ingress. |
39:22 | Let's get into our questions and we'll see what we've got. |
39:30 | DynoDoug's asked, I've been working on repairing an OEM harness for a 350Z. |
39:34 | All of the existing PVC sheathing is hard and cracking. |
39:37 | Depinning every connector to resheath the entire harness seems like a lot more effort than it is worth. |
39:42 | Do you guys have any favourite products for putting new sheathing on an existing harness that does not require the harness to be disassembled? I'm also curious how other folks clean harnesses and connectors. |
39:53 | Is there a good chemical out there that cleans quickly and will not cause corrosion to the terminals? Ideally something I can put in my ultrasonic cleaner, then just submerge the entire connector. |
40:02 | OK I can't speak to the ultrasonic cleaner, I don't have one and I've never used one so I couldn't really give you any input there. |
40:10 | Isopropyl alcohol in terms of cleaning down a harness is a good product, it doesn't degrade the sheathing on the harness so that's probably my go to. |
40:20 | Can be a bit difficult obviously with an existing harness that hasn't been protected with the likes of DR25, over time you're likely to get dirt, grease, grime and oil impregnated into the harness so can be quite tricky to clean out. |
40:36 | I don't use it very often so I cannot off the top of my head remember the name but there is a looming tape from Hellermann, I'll just see if I can find it while I'm talking. |
40:48 | Yeah a looming tape from Hellermann, there we go, it's call Hellermann Tyton cloth tape. |
40:55 | Let's just head over to my laptop screen for a moment and this is just from RS Components but this is essentially what it looks like. |
41:01 | Oh that's the wrong button. |
41:04 | So that one there you can basically wrap around the harness so it's a nicer variant of the old PVC black electrical insulation tape which never really lasts and melts and goes all gooey and horrible as soon as it gets hot. |
41:20 | This is designed for protecting a harness. |
41:22 | There's a number of other products like this. |
41:25 | I don't tend to use them so I can't speak extensively about them and their pros and cons. |
41:30 | Obviously the biggest pro is you don't need to disassemble a harness but because it is a cloth type tape, you aren't going to get the level of protection to the harness from further moisture, dust, dirt etc getting into it that you would with the likes of DR25. |
41:47 | Downside is the only way of getting DR25 onto the harness is going to be depinning all of the connectors as you mentioned so that might be something that's worth considering. |
41:56 | Yeah there are some split loom products as well, again you're not going to get the sort of protection for the harness using those though. |
42:07 | Right we'll head back over to our questions. |
42:16 | Our next question comes from Zack who's asked, I am about to start a project where I am delooming, rerouting some of the wiring and relooming an OEM Honda wiring harness. |
42:23 | Is there a place for Raychem tubing and boots on a project like this? Problem with using heat molded parts is that it really requires you to be working with motorsport grade products from the get go. |
42:37 | The heat that you need to use in order to recover those boots, is going to melt cheaper lower grade PVC insulation. |
42:46 | So you really need to be using TXL at a minimum wire, or ideally Tefzel and really it's designed to work with the likes of DR25 sheathing. |
42:57 | So it's kind of a step up and yeah you're not really going to incorporate this on entry level products, entry level harnesses. |
43:06 | So depends how much time and money you really want to put into the harness as to what the correct materials are to work with. |
43:12 | If you are working with DR25 and TXL then absolutely these are a great addition. |
43:18 | Justin has asked, how would you go about sealing the end of the harness to a factory connector, say coils, cam position sensors, TPS, things that don't have a step for a boot to attach to? So I mean really not to dissimilar to what I just looked at with the little demonstration here. |
43:36 | This is a coil, it's an OEM coil and there isn't a lip for a boot on this but by, in this instance there are a couple of little tabs that suit to locate and positively lock into the factory connector body so those work as a nice locating device for that particular boot anyway. |
43:58 | But provided you are going to abrade the plastic surface that you're going to shrink that down onto, it's still not going to move around once it's glued down, it's still going to do a pretty good job there. |
44:12 | Zach has asked, are there any negatives to not heating the boot up fast enough? Other than taking an eternity. |
44:17 | No just taking an eternity, I mean there is a minimum temperature rated for recovery. |
44:24 | I've always found that that minimum temperature doesn't even get the boot budging so you really do need to be sort of in that 250°C + vicinity but yeah it's just a case of time but that time honestly, when you're not presenting a webinar, you'd be thankful for that time because it allows you to really position that boot and do a good job of getting it all aligned and nice exactly how you want it to sit. |
44:50 | Again as I mentioned, particularly when you're working with some of the more complex transitions such as those T boots. |
44:58 | DynoDoug's asked, on the harness shown early in the webinar, there were two trunks coming into a junction with multiple branches leaving the junction. |
45:06 | Why are two trunks used in this case in lieu of one? Is it a strategy to keep looms more flexible or avoid the need for extra large DR25 which is expensive and difficult to source? No the only reason that that was done like that, and I've actually since remade this harness with a single autosport connector, at the time we could not source a 79 way connector for the bulkhead so two we used instead. |
45:34 | There are some advantages in that, the two autosport connectors on that harness, one uses size 22 contacts and one uses size 20 so when we want to use wiring that can support a little bit more current handling, 20 gauge is around 7.5, 8 amps whereas 22 gauge, you're only going to be able to get about 5 amps through that safely so few idiosyncracies in terms of what you want to choose and why. |
46:02 | Really a lot of it comes down to the planning of your harness construction but absolutely that would not be the norm and certainly not an essential element. |
46:12 | Chase has asked, would there be any benefits or drawbacks of using a 2-part RTV to backfill boots as opposed to the traditional epoxy? Slightly softer cure, maybe less stress imparted on the pin retaining tabs? So if you're talking about a RTV that stays semi, sort of cures not fully rigid, the answer to that I would expect would be a no. |
46:36 | We're not back filling here and if we do backfill, what you're going to end up with is a really big problem if you ever come to actually effect a repair on that particular connector. |
46:47 | Now this little example here, no big deal on this guy but if you are looking at the autosport connectors, there's a lot going on behind these, now granted the actual wiring is wrapped in kapton tape first anyway, the kapton tape is pretty important because it stops the epoxy from actually getting onto the individual conductor strands and means that if we have to cut that boot off we can remove the kapton tape and the wiring is accessible beneath. |
47:19 | If you want to fill that with an RTV style product then that's going to make it a little bit harder again I think if you need to effect a repair. |
47:26 | Really in terms of strain relief, the two key elements in that, or 3 key elements are first of all the actual rigidity of the shrunk down recovered boot, secondly the ability of the epoxy to actually secure it to the autosport connector in that gnurling and then thirdly the ability of the epoxy to also grip down onto the DR25 there. |
47:48 | So those are the elements that are going to give us the protection and strain relief that we want. |
47:58 | Next question comes from Papapetad I think it is, sorry if I've messed up your name there, you're using heat shrink tubing for all the main lengths and runs of the harness, right? And is it all glue lined or are you relying mainly on the branching/splicing/connection zones to insulate the harness from the elements? So to be clear, yeah everything is protected using heat shrink. |
48:20 | This one, the main branch is here covered in a product called DR25. |
48:27 | That is not glue lined, that is just a heat shrink product that is designed for harness protection, particularly it is impermeable to all of the common chemicals that we see in the automotive industry. |
48:38 | It's to a degree, a reasonable degree, abrasion resistant as well so it provides good mechanical protection to the harness but no it is not glue lined as such. |
48:50 | We are relying on the heat molded parts to provide the protection from the environment as you've correctly guessed there. |
48:59 | OK last question here, little bit off the actual topic of today, from TheKillerMarine who's asked, what membership would you recommend for someone who just wants to learn how to build a wire harness for an off road trail rig? So it would have to be watertight and handle the abuse of hitting trails. |
49:14 | So I would probably recommend with that, we have our Wiring Starter Package and you can find that on our hpacademy.com website. |
49:25 | That starter package is still at 50% off with our Black Friday sale as well at the moment. |
49:31 | So with that you can choose our club level or our professional motorsport level course, slightly different price points on those. |
49:39 | Both include our Wiring Fundamentals course which is really important no matter what sort of harness you're building, the wiring fundamentals remain the same. |
49:48 | If you do want to produce a properly sealed harness then typically you're going to be working at the professional level though using DR25 and these heat molded boots. |
49:58 | Particularly with an offroad vehicle or trail rig, it's pretty common to get pretty muddy and to clean it down maybe with a pressure washer, you would not be wanting to do that with an unsealed harness because you can almost guarantee in time you're going to end up with some moisture getting into some of the connector bodies. |
50:17 | Alright that's brought us to the end for today. |
50:19 | Thanks to everyone who has joined in. |
50:22 | Now for those who have not watched live and are watching this in our archive, if you do have any questions, please feel free to ask those on the forum and I'll be happy to answer them there. |
50:32 | Thanks to everyone for joining today and we look forward to seeing you along at the next one. |
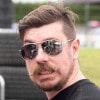