332 | Setting Up Individual Throttle Bodies - ITBs
Summary
Individual throttle bodies are a deceptively simple device that adds a few easy to overlook complexities into the tuning and setup process. In this webinar we’ll take a look at the mechanical setup requirements and what you’ll need to cover off when you’re fitting ITBs to your engine and getting them up and running for the first time.
00:00 | - Hey team, it's Andre from High Performance Academy here, welcome to another one of our webinars and this time we're going to be diving into individual throttle bodies, specifically here I'm going to be talking about the mechanical setup. |
00:12 | We'll hold another webinar in a few week's time where we're going to dive into the specifics of tuning them but I'm going to separate these out because they are two very different elements and I think the setup is the place where most people go wrong so understanding the implications of fitting ITBs to your engine and then what you need to do in order to get the most out of them is really critical. |
00:37 | I see so many people with individual throttle bodies fitted to their engine with a really horrible driveability at part throttle and at idle and it's kind of become accepted that that's just how ITBs are. |
00:51 | The reality is it absolutely does not need to be that way, you can get a set of ITBs to drive just as nicely, if not nicer than a single throttle body and plenum arrangement so that's what we're going to be diving into. |
01:06 | The first element here, I am going to talk about tuning, just because this is a really key element with ITBs, and I know that a lot of people argue this point and I just want to really be clear about this. |
01:19 | When it comes to tuning with individual throttle bodies, we have to make a pretty significant change to our tuning strategy and that is using the technique of alpha n which is essentially using throttle position on the load axis instead of manifold absolute pressure. |
01:34 | Now when we look at a conventional engine that runs a large plenum chamber with a single throttle body, conventionally we would use manifold absolute pressure on the load axis and that will not work if you're running individual throttle bodies so let's talk about why that's the case because I have people argue with me that they absolutely can get good drivability using manifold absolute pressure, basically treating individual throttle bodies just like a single throttle and large plenum. |
02:07 | So if we look at what's happening with a single throttle body and a large plenum, the volume of that plenum is really the key element, we've got a large volume of air behind the throttle plate and that is where our manifold absolute pressure signal is coming from, so we're basically measuring the average pressure, air pressure inside of that manifold and of course in our four cylinder or six cylinder or whatever it is, we'll have one cylinder go through the intake stroke, so the intake valve opens and it then draws air from that plenum. |
02:38 | But because of the large volume of air in that plenum chamber, essentially we're averaging that out and that is the air pressure available to go into that cylinder when the intake valve's open. |
02:51 | So it works out really nicely, it gives us an accurate measurement of the air pressure available that's going to go into that cylinder which in turn we can basically infer the mass of air that's going into the cylinder. |
03:03 | Alright stay with me here, I know this does get a little bit complicated. |
03:06 | Now if we look at individual throttle bodies in comparison, and let's just get a set of these under our overhead here, these are a set of Jenvey ITBs that are going on our Honda K20. |
03:18 | This is the actual throttle bodies themselves, obviously we've got our trumpets here and this is simply an adaptor that goes to the cylinder head. |
03:28 | So the element here is that if we flip this over, this will be the underside, got these little bosses here and what we would do is basically tap each of those for a pressure port and we'd run those to a vacuum balance bar so we haven't got that done on that set of throttle bodies but I've got another set here from an LS and I'm just going to flip these upside down. |
03:57 | And we can see that's exactly what we've got here, so we've basically got a tapping on each of the intake ports and then it goes to this little canister here which is basically a balance bar and we've got one port that comes off this which is going to go to our MAP sensor. |
04:14 | So all well and good, this is the argument I get, OK well now if we do that, if we go through that process, we now have a valid manifold absolute pressure signal so we can feed that into our ECU and we can just pretend it's like a conventional single throttle and plenum. |
04:32 | Unfortunately that's not the case, we can't do that because the reality is what we're doing now with that balance bar setup is we've got a pressure port coming from the back of each of the individual throttle bodies. |
04:45 | So we're going to be measuring the average of all four cylinders, let's just keep it simple and pretend we're dealing with our K20, measuring the pressure behind each of the throttle plates on all four cylinders so let's say we've got something like 70 kPa being measured, we're pretty close to wide open throttle, let's say 60 kPa just to bring our throttle opening down a little bit. |
05:08 | So the problem is that when the cylinder opens its intake valves on the intake stroke, we don't have the large volume of air between the throttle plate and the intake valve that we do with our plenum so what happens is as soon as the intake valve's open, the air is going to go into that cylinder so if we could measure just the specific air pressure on that cylinder, we're going to see our air pressure drop right down. |
05:35 | But because the other four cylinders, the intake valves are still closed, what we end up with is we're measuring the average across all four so our average pressure doesn't drop so no longer are we getting a realistic representation of what the air pressure is on the cylinder that counts, the cylinder where the intake valves are open, instead we're getting a very unrealistic representation because it's skewed by those other three cylinders where the intake valves are closed. |
06:05 | Now the reason that doesn't happen or doesn't cause problems with our single throttle and plenum is because we've got that large plenum which has got a large volume of air that each of the cylinders is drawing from so we are in that instance getting a realistic pressure signal. |
06:20 | So what does that actually mean for us? Well what it means is that if we try and tune the ITB engine, the same method using manifold absolute pressure, we're going to have a couple of problems. |
06:32 | What we'll find is that initially we can start the engine and we can get it idling nicely and we can even get moderately good drivability. |
06:39 | Where the problem comes is in the part throttle region. |
06:43 | At closed throttle, everything works pretty well and at wide open throttle, it doesn't really matter because our throttle bodies are wide open so the pressure signal is going to be at or very close to atmospheric pressure but at that part throttle, this is where we get these big variations between the reported manifold absolute pressure and what's actually happening in the cylinder where the intake valves are open. |
07:06 | So we get this situation where we're going to either be very very rich at part throttle or very very lean and depending where we are in the throttle, we just cannot get everything to work perfectly right through the range of throttle and RPM and believe me I have tried this numerous times in the past, take this from personal experience, I'm not just quoting here, the technical reason why it can't work, I've tried both ways, and it does not work. |
07:32 | The other option that does work but we don't really see it in the aftermarket world is of course we can use a mass airflow sensor and we see this on two of the factory individual throttle body turbo engines that I have been involved in tuning which is the Nissan RB26 and also Nissan's GTiR or N14 based SR20DET, both run turbochargers and individual throttle bodies from the factory but both of these engines in factory form use mass airflow sensors so kind of takes out the irrelevancy or the, sorry the inconsistencies with the manifold absolute pressure signal because we are physically just measuring airflow directly so that is what the ECU needs to know in order to give the correct fuel. |
08:19 | So without trying to dwell on this in too much more detail, just understand that if you want to get good results with ITBs, it is going to be essential that you tune using alpha n with throttle position on the load axis. |
08:34 | Let's talk a little bit about the mechanical setup of our throttle plates because this is the other area that I see people go wrong time and time again. |
08:42 | So we'll get our Jenvey throttle bodies under the overhead again and what we'll see is that between each of the throttle bodies we've got, they're not locked hard together, we've actually got a little bit of flex in here and we've got some adjustability and that's really really important. |
09:02 | Now what you'll quite often find with individual throttle bodies is that when you get the engine up and running, it's not going to idle very nicely, it'll often pop and bang at idle and the other part where we see a lot of issues with individual throttle bodies is when we just first crack the throttle, probably the first sort of 3-10% of throttle opening, we can find that the engine is going to run really really rough and almost irrespective of what we do with our fuelling, if we're looking at the air/fuel ratio. |
09:33 | So why is that the case? Well there's two elements to this, first of all, what we need to understand is that the airflow through a throttle body is really non linear so what I mean by this is that when we first crack that throttle body open, we see the airflow increase quite sharply, quite a lot so for a very small opening in throttle, we're going to see quite a large increase in airflow. |
09:57 | And then as we continue to open the throttle body, that airflow sort of flattens off a little bit, sort of it's kind of like an exponential curve but it gets less as we open the throttle more and it's really easy to see this effect if we're dyno tuning any engine, even a single throttle plate, if we hold the engine under steady state conditions and we open the throttle 5% or let's say 10% to just get a baseline, we look at the torque and power the engine's producing and then we double the throttle opening, we go from 10% to 20%, we're not going to get a linear increase in our power and torque and then if we go 20 to 30, 30 to 40, what we're going to find is that initially we get a really steep rise in our power and torque output for a small increase in throttle opening but if you get up to 80% throttle opening, between 80 and 100% throttle opening, often the difference in power and torque will be minimal, only maybe a few percent if that so that's just that airflow through the throttle bodies. |
10:57 | Alright so now we understand that,the next element is that that means that the throttle tuning, throttle body tuning is going to be very very sensitive, closest to closed throttle and what I mean by this is we want to make sure that each of the individual throttle plates is sitting at exactly the same position and we only need a few thousandths of an inch difference in throttle plate opening to have a really big impact on the airflow through that particular throttle body so you can understand that if we've got these throttle bodies here, and we've got three of our throttle plates essentially almost completely closed at idle and then the third one's cracked open let's say an eighth of an inch. |
11:39 | The one that's cracked open is going to have a lot more airflow through it and hence that cylinder is going to be running lean, it's simply got more air entering it and this is easy to overlook because if we are tuning using a single lambda sensor that's placed in the collector, it's going to be reporting the average of all four cylinders. |
12:00 | So even though we might have one cylinder that the throttle plate's cracked open too far, it's going to be running lean but if our other three cylinders are there or there abouts, the actual reported air/fuel ratio's probably going to be still pretty close to our target and even if it's a little lean and we richen the whole fuel map up a little bit so that our lambda's tracking correctly, we're still going to find that we're going to have one massively lean cylinder and three that are just slightly rich and that's how kind of averaging obviously works. |
12:30 | So what we need to do is spend the time initially to make sure that all of our individual throttle bodies are matched or calibrated together correctly. |
12:40 | So how do we do that, well we actually need to use a carb balancer. |
12:46 | So if we jump across to my laptop screen, there are a variety of different brands and styles of this but this one's pretty typical. |
12:54 | What we can see is we've got a little rubber bit at the end which fits nicely inside the intake trumpet so it seals to the intake trumpet so that all of the air that is entering that particular cylinder has to come in through this mechanism here and then it has a little moving vane that you'll be able to see through this window and basically it's going to show how much airflow's going into that particular cylinder. |
13:22 | So what we do is essentially get our engine up and running at idle and we'll go through and we'll place that in each of the individual trumpets one at a time, taking note of the airflow and we want to basically open or close the respective throttle plates until we've got all four matched within as close a range as we can. |
13:45 | So this is the key part that people really really often overlook and if you don't do this right, it's going to influence the rest of your tuning and the rest of your tuning is unfortunately going to simply be very very difficult at best. |
13:59 | Now don't get me wrong, you can still get the engine running really nicely at wide open throttle and it comes down to what I was saying earlier, the airflow through the throttle bodies is really really non linear, remember I said that perhaps between 80 and 100% throttle, might only be looking at a few percent difference in terms of power and torque. |
14:20 | Well that's because we're only looking at a few percent difference in terms of airflow, hence we might be massively too rich or too lean down near closed throttle because those differences get magnified but once we get up past about 50 or 60% throttle, we're probably going to find that even if the throttle plates aren't calibrated or equalised properly, it's not going to really be noticeable in terms of drivability. |
14:44 | Doesn't make it right but it still will work so if you're tuning an all out, all motor drag engine, well this will also be the same to be fair for a turbocharged ITB setup, then you could overlook it but it's still going to give you a really really poor idle quality but if you do want drivability, if it's a road car or a road race application, this is absolutely an essential, you cannot overlook that. |
15:11 | Alright so that's the first step once we're up and running is to go through and very carefully balance the throttle bodies and make sure that the airflow into each cylinder is the same. |
15:21 | The other element though comes back to this vacuum balancing. |
15:25 | So it is possible to run the engine with no manifold absolute pressure signal with alpha n. |
15:35 | And I would not recommend that. |
15:37 | The reason for this is that most ECUs run a background fuel compensation based on manifold absolute pressure and this is simply based around the ideal gas law which means that if we double the air pressure, all other things being equal, we need to double the mass of fuel being delivered in order to maintain the same air/fuel ratio. |
15:58 | So most ECUs will do that calculation in the background based on the manifold pressure and basically it aids the resolution in our fuel table. |
16:06 | So we really want to still take benefit of that if we can but the other element is, and this gets quite fussy or quite finicky but I am fussy, and you will notice this in a road car application most of the time. |
16:21 | So we can drive our engine at let's say 3000 RPM and 15% throttle on a level piece of road and if we looked at the manifold absolute pressure, we'll have a certain value. |
16:35 | So if we are accounting for our manifold absolute pressure signal, the ECU's obviously looking at that and making adjustments in the background to the fuel delivery in order to keep our air/fuel ratio where it needs to be. |
16:47 | Now most people assume that for a fixed RPM and a fixed throttle position then also our manifold absolute pressure is fixed. |
16:56 | To a degree that's true but what you'll find is that if you now take that car and you drive it down a slight hill and you maintain that same throttle opening and that same RPM, obviously that gets a little bit tricky because the car's going to want to accelerate but just in a split second if you look at that same point, the manifold absolute pressure signal will be slightly different. |
17:19 | So if you are not feeding a manifold pressure signal into the ECU, it cannot do that background fuelling compensation and what you will find is that with ITBs at part throttle, when you're going over undulating ground, uphills, flat, downhills, you will see small discrepancies in your air/fuel ratio. |
17:38 | Now yes there are other ways around this, if you were running a wideband air/fuel ratio sensor and controller fed into your ECU then you could absolutely fix this by using closed loop fuel control but I feel it's always better to actually address the real problem which is this fluctuating manifold pressure signal. |
17:59 | So this is where the vacuum balance bar comes in, so again just looking at our system here, we want to basically make sure that we're taking a feed from behind each throttle plate, and it must be between the intake valve and the throttle plate, feed this into a canister which has got a feed from all four or six or eight cylinders, whatever it might be and then that's where you can then take a manifold pressure signal and again the ECU is going to be using that for that background fuel compensation so while it can be tempting now that you've got a manifold pressure signal into your ECU, for all of the reasons we've already talked about, we definitely don't want to be running on manifold absolute pressure. |
18:43 | Alright so that's the fundamentals, we also need to consider how we're going to do idle speed control. |
18:51 | So conventionally what we would do is have an air bypass around our single throttle body into our plenum and that doesn't really need anything special to consider as far as the tune is concerned because again we've got that large volume in the plenum chamber, it's averaging that manifold pressure and we've got a realistic understanding of what the manifold absolute pressure is when the intake valve's open for the cylinder that's on the intake stroke so basically in that instance, when we're using manifold absolute pressure as our load axis, as we open and close that air bypass around the throttle body the computer can track what's changing with our manifold pressure and make the appropriate adjustments to our fuelling as required. |
19:36 | It's not quite so simple when we're bypassing air around the throttle plates in ITBs and there's a couple of ways of doing this so first of all what we need to understand is with the ITBs, if we aren't physically opening and closing the throttle plates, then our throttle position is not going to move, and the ECU really doesn't know that we've got that extra air bypass around the throttle plates so we need another way of doing this. |
20:04 | In the perfect world, this might be a little controversial, in the perfect world I feel the easiest and cleanest way of doing this is by using drive by wire throttle actuation because then we're actually opening and closing the throttle plates to affect our idle speed. |
20:18 | There's arguments about the pros and cons of drive by wire, I'm not going to get into that argument, I'm just saying that that is a really nice way of directly actuating the throttle plates in order to open and close them and chase our target idle speed. |
20:33 | If on the other hand you're going to bypass air around the throttle plates because you're using a conventional mechanical throttle mechanism, you are going to need kind of another balance bar like we've looked at because the air bypass is also going to need to be delivered to each of the cylinders, be it four, six or eight. |
20:53 | So you can't just bypass air into one individual throttle body so you're going to get back into that same situation I was talking about before where you're going to have that individual cylinder running excessively lean when we start bypassing more air into it so it has to go to all four cylinders. |
21:08 | Now yes you are going to have the benefit of the MAP balance still helping you here but generally in my experience, if you're going to use that sort of technique, you will need to add a compensation table to add or subtract fuelling based on the RPM and the idle speed control bypass position so just a consideration there as to how you're going to do that, it's always good to think through these things before you actually commit to the mechanical setup. |
21:40 | We will dive into this in a bit more detail when we look at the tuning elements in a future webinar. |
21:46 | Now I'm going to have questions and answers really shortly so if you do have any questions, now's a great time to put them in. |
21:54 | The only other topic I really wanted to cover today was the trumpet length. |
22:01 | So we've got a sample here of another one of the Jenvey ITBs from our K20, this one is I think a 48 mm and we've moved to 50. |
22:12 | But the length of the trumpet is obviously a tuning element that's quite important with ITBs and one of the reasons why we would consider going away from a single plenum, plenum and single throttle anyway. |
22:25 | So really what we're interested in here is the length from the trumpet to the intake valve and essentially we can take advantage of the tuning effect and the resident frequency and basically if we tune this right in terms of the overall length from the trumpet to the intake valve, we can get that resonance occurring at a certain RPM to basically create a ram effect and improve the volumetric efficiency of the engine. |
22:53 | There's no free lunches here because this is all about compromise. |
22:58 | We're going to end up improving the volumetric efficiency at one point in the rev range but it's going to hurt it at other points so there is no magic number, there are calculations you can go through to get yourself in the ballpark but ultimately I've always found that that's going to get you close but you almost certainly are going to benefit from testing a few different length trumpts and see what actually gives you the powerband that you want. |
23:24 | Now problem being that these trumpets can end up being quite expensive so if you want to buy three or four sets, you don't really know where you need to be, that's going to end up costing you quite a bit of money. |
23:37 | These days with the relatively cheap access to 3D printers, and the likes of Fusion 360 which can also be pretty cost effective for personal use, this is actually a 3D printed trumpet, this is just a bit of a test piece that we made in house just to see how well this is going to work. |
23:58 | It isn't the nicest looking and I definitely wouldn't recommend it for permanent use but for a relatively modest input in terms of time and cost, you could print out a range of these in maybe 10 mm increments and really quickly dial in what the ideal trumpet length is for your particular application and then once you've got that set in stone then of course you can buy a set of aluminium or carbon fibre trumpets and that way you only really have to do it once so if you own a 3D printer or alternatively you know someone who does, it's a relatively straightforward and simple production task to make those. |
24:41 | So that covers the mechanical elements of the ITB setup. |
24:45 | Not particularly difficult but I do constantly see people get these fundamentals wrong and it's really going to take away from your experience once it comes to actually tuning the vehicle or more importantly actually driving it so if you get these right, the tuning elements, which we will talk about in the upcoming webinar, everything's going to be so much easier. |
25:06 | Alright let's have a look at our questions. |
25:09 | Lolapalooza's asked, you'd want the vacuum manifold separate from any other vacuum system like the brake booster, is that correct? Yes absolutely, so a brake booster, you would always want that separate from your actual manifold pressure signal anyway. |
25:25 | Often when you're going to ITBs, you'll actually be running without a brake booster but yeah you could run another balance bar for your brake booster alone anyway, just gets a little bit more complicated in terms of obviously you've got a lot more plumbing going on but absolutely that is the way I would do it. |
25:43 | Alpine Vice Motorsport's asked, in addition to trumpet length, could you speak to selecting throttle diameter or perhaps injector position in the runner? Yeah OK throttle diameter, it's a bit of a tough one. |
25:58 | We've actually just gone through this procedure and we'll be doing a video covering what we find with this. |
26:05 | With our K20 we've currently got a built Honda K20 in our CRX racecar and again off the top of my head I think I've got this correct, we started with 48 mm throttle bodies, what we want to do is increase the power the engine's making just like everyone wants to of course but we're also going to be doing this at higher RPM and there are a few other changes we've been making to the mechanical setup including the cam profile but essentially to make more power higher in the rev range, we have decided to try stepping up to the 50 mm throttle body. |
26:38 | You'll find if you Google there are numerous resources in terms of throttle body sizing for specific engines for certain power levels. |
26:49 | I think at the end of the day, this is still only going to be a guide that will get you in the ballpark and ultimately unfortunately it is an expensive exercise, ultimately the only way to find what is actually going to be ideal for your application is going to be to do some real world testing so yeah unfortunately that particular testing ends up expensive. |
27:10 | Injector position in the runner, so this is an interesting one. |
27:14 | So ideally what we find is that most manufacturers place the injector very very close to the intake valve and the has some benefits for OE manufacturers, specifically, particularly when the engine is cold. |
27:29 | It reduces the amount of the fuel from the injector that's going to wet out on the port wall so probably this really all stems around emissions and they can target the injection very nicely to get it exactly where they want it. |
27:44 | There are benefits from a motorsport application in actually moving the injector further outboard and quite often, particularly if you've seen old NA F1 engines, the injectors are actually completely outside the trumpet so advantage with this is it gives a lot more time for fuel to mix, so we get a nice homogenous fuel/air charge, we don't get rich and lean areas in the charge. |
28:09 | There can also be some advantages in terms of the cooling effect of the fuel on the inlet intake charge which can in turn give a small but measurable improvement in engine volumetric efficiency. |
28:23 | In the perfect world, while it's a lot more complex but this is what we're going to be trying on our K20, is we run two sets of injectors, we run a set of injectors in the stock location down near the intake valve, that's used at idle, light throttle openings and then at higher RPM and wide open throttle, we would then stage into a set of injectors mounted outside of the intake trumpets. |
28:47 | Now again what are the real world benefits? You're going to need to test and find, again we'll be doing a video on exactly that as well. |
28:54 | William has asked, what's the benefit of ITB's on naturally aspirated motors vs boosted motors? What about a boosted H or K series? OK so first of all, individual throttle bodies, absolutely can be used on NA or boosted engines. |
29:12 | We don't see them that often on turbocharged or supercharged engines and I think this really comes down to complexity. |
29:20 | As I mentioned earlier, Nissan decided to run ITBs on both their RB26 and the N14 GTiR SR20DET, both turbocharged engines and at least as far as my understanding goes, the intention here was to improve throttle response. |
29:39 | I've driven GTRs with individual throttle bodies and factory plenums and I've driven them with a single throttle body and plenums and I can't really speak to a massively noticeable advantage in throttle response from the ITBs but I'll also add a caveat here, I haven't been able to test back to back the exact same engine, the exact same turbo combination, everything the same except for single vs multi throttle so it's very difficult for me to state with authority that there's no advantage. |
30:12 | Obviously Nissan saw fit to do that. |
30:15 | In terms of why we would fit individual throttle bodies to a naturally aspirated engine, it does give us a lot more flexibility in the tuning elements, the intake length which is a lot more difficult to do with a plenum, also the flexibility to change things like the throttle body size independently as well so there's a tuning element that is beneficial there to naturally aspirated engines. |
30:38 | In my personal experience, I would say a lot less of an advantage when we're adding boost. |
30:44 | Next question, if I have a throttle cable and six ITBs, I feel it's heavy on the pedal, is that correct? Unless there's a throttle by wire solution? Well this is really going to come down to the return spring on your throttle body setup and basically the mechanical leverage. |
31:02 | It shouldn't need to be overly heavy but that really comes down to a setup element. |
31:08 | I have had trouble, wasn't a six cylinder, have had trouble years and years ago, it was a K20 that I tuned for one of my customers and they had supplied, I think it was TWM throttle bodies and they were absolutely horrible. |
31:24 | They would essentially go almost over centre and the throttle plates would jam in the throttle bodies so that would happen when it was closed fortunately, probably better than it jamming at wide open throttle, but if you're driving it around town, you'd sort of come up to a stop, close the throttle and then when you'd try to get going again, the throttle was rock solid and when you tried to move the throttle, had to overcome that friction and then the throttles would pop open and you'd sort of end up having the RPM jump up to sort of 4000, 4500 RPM so you felt like a bit of a noob driver and it just was a horrible experience but that was the throttle plates actually jamming in their housings as opposed to the return springs, sounds to me more like you've got a return spring problem. |
32:10 | Manitou Black's asked, is it worth leaving individual O2 sensors in the exhaust pipes for ongoing data logging and tune improvement? Yeah so I probably should have touched on this, might go into this in the tuning webinar as well but yeah I think ITBs are one of those areas where individual cylinder lambda is a bigger benefit than running the same on a single throttle plenum arrangement because what I was saying if you've got one cylinder where the throttle is cracked open a little bit further, with individual lambda you're going to instantly see that you've got one cylinder that is lean. |
32:47 | Now you could fix this of course then with individual cylinder fuel trimming but that's putting a bandaid on the real problem which is getting our mechanical setup dialled in. |
32:57 | So when we get our mechanical setup dialled in, the individual cylinder lambda, it's nice to have but certainly not essential to have. |
33:05 | In terms of leaving them there as well, generally individual cylinder lambda, I would use this for dyno work and maybe some validation on the racetrack or the road. |
33:17 | Once you've got that tune dialled in, things shouldn't move around so there's no real need to retain all four or six, whatever it is, individual cylinder lambda sensors, these are expensive and they will also wear out so generally they're used for the dyno work only and then removed. |
33:32 | Obviously we would still have a single lambda post collector so that we're using this for overall fuel delivery confirmation and if we're running closed loop lambda that'll run off that. |
33:45 | Blake has asked, is there any reason more aftermarket setups don't use mass airflow sensors? OEMs must have done their due dilligence. |
33:54 | Yes and no, so the nice thing with a mass airflow sensor is that when it is calibrated correctly and the calibration is accurate, it is reporting the exact mass of air that's entering the cylinder. |
34:07 | And that's really what the ECU needs to know in order to achieve a specific air/fuel ratio, that is just the ratio between the mass of air entering the engine and the mass of of fuel being delivered so if the ECU accurately knows the mass of air and it of course knows what size injectors are fitted or, to put it another way, what mass of fuel will be delivered for a specific pulse width delivered to the injector, it can really accurately achieve that. |
34:30 | That's the upside but it's not always like that. |
34:34 | Mass airflow sensors get dirty, their calibration can change, their calibration, well change when they get dirty, it doesn't just change by itself. |
34:43 | The calibration is also very sensitive to the entire inlet track so what I mean by this is if you change the air box, fit a cold air filter, cold air intake I should say, even if you change the air filter element, that can be enough to influence the mass airflow sensor calibration so then the fuelling is no longer going to be correct. |
35:03 | From an aftermarket standpoint, mass airflow sensors are a bit cumbersome. |
35:07 | They are difficult to mount in the engine bay. |
35:10 | The other element that we need to consider is the resolution of the mass airflow sensor. |
35:15 | Mass airflow sensors will have an upper limit in terms of how much air they can measure so obviously in an OE application they're chosen to suit, everything works nicely, it's very easy in most OE applications to increase the boost for example in a turbocharged engine, exceed the mass airflow sensor capability and then you can't really read that additional airflow. |
35:38 | Now yes there are ways around this, we can fit larger mass airflow sensor tubes but basically in the aftermarket a lot of complexity, speed density system using a manifold absolute pressure sensor works really really well. |
35:50 | We're simply calculating the mass airflow instead of directly measuring it but it's a well proven system and significantly simpler. |
35:59 | Nacker's Jewels has asked, in theory if ITBs were installed inside a conventional manifold, could a mass airflow sensor be used? Absolutely yes, no problem whatsoever and as I've already mentioned, while they are turbocharged engines, both the RB26 and the GTiR do exactly that with a mass airflow sensor. |
36:20 | Manitou Black's asked, if you can't bypass idle air or use drive by wire, can you reliably use ignition control to manipulate the idle? Yes and no. |
36:30 | Idle ignition control, and just very briefly, that is the process where we advance or retard the ignition timing quite quickly in order to add or reduce engine torque at idle and therefore increase or decrease the idle speed. |
36:43 | There are limits in terms of the range that you can achieve if you are only using idle ignition control though. |
36:50 | Ultimately when the engine is cold, to get a good idle speed, you will need additional air bypass so generally for a racecar, I will quite happily run with no idle speed control circuit. |
37:00 | What I will do is at a hot idle, I will purposefully set the air bypass, so the throttle stops, to give the idle speed maybe 200 to 300 RPM higher than I actually want and I'll use idle ignition control to bring that back down. |
37:15 | You need to be careful here because you could set it 1000 RPM higher than you want and then use really aggressive retard to pull the idle speed back but you're going to be idling the engine with the timing at zero or -5, maybe -10°, that's going to build up a huge amount of heat so that's why I say there's a realistic range that we can use, so I will probably accept the idle speed being 200 to 300 RPM higher with normal timing, let's say 15-16° when it's hot and conversely when it's stone cold, at cold start we'll probably find that the engine will most likely idle by itself but it'll probably idle quite low, it might idle a few hundred RPM below where we desire and that's about the best we can get if we're only using idle ignition control. |
38:05 | Pocks has asked, thoughts on sharing the idle air with MAP balance bar instead of using a second one? So you can do this, I think it's the 4AGE 20 valve throttle bodies essentially do this. |
38:23 | I am trying, I'm struggling to remember, we've got a set in the shop at the moment and I should have paid more attention to them before starting this but if my memory serves correctly, basically that feeds the idle air bypass into the same balance tube that essentially runs across the top of all of the ITBs and then at least in the black top the manifold absolute pressure signal comes off that. |
38:45 | That's a great example, coming back to that other question, about using a mass airflow sensor. |
38:50 | The silver top 20 valve 4AGE from Toyota, that used a mass airflow sensor, was the black top that went to manifold absolute pressure. |
38:59 | OK so the problem I see with this is that quite often you'll end up with, depending on the frequency that the idle speed control solenoid is being pulsed at, this will introduce basically a wave in terms of the manifold absolute pressure signal so I try and separate them where possible but I can't say that you cannot do it. |
39:27 | NRG Racing Engines has asked, in any scenario with ITBs how can the PCV system be properly retained? Yep that is a real problem, I would say that with racing engines or heavily modified engines with ITBs, more often than not, the PCV system is basically ditched and we run this into a catch can. |
39:49 | Now I do understand that depending where you are in the world, that may not be legal. |
39:55 | The only other way of getting around this would be basically run your ITBs into a common manifold and then an intake pipe running off that and run your PCV into there so it can be done but it's not that pretty. |
40:09 | Also when there is a lack of vacuum due to a radical cam, how could the PCV system in an LS7 be retained in this scenario with Jenvey ITBs and a MAP sensor? So you'll get a lack of vacuum at idle with a really large cam but what you will find is that once you're off idle and you're maybe sort of 2000, 2500 RPM at part throttle, you will still get a reasonable amount of vacuum under those conditions so basically trying to do what you're talking about there, you're dealing with compromise no matter how you look at it, perfect world you would run the ventilation into a catch can and be done with it. |
40:50 | Next question, would ITBs benefit from ram air? Yeah absolutely, if you can arrange ram air then yeah, so you'd really want to take advantage of that by also, that's another reason why you need to be monitoring manifold absolute pressure. |
41:08 | I gave one example of when that's important but if you have got a ram air arrangement at high speed, you would be getting a very very modest amount of positive pressure potentially and that's going to obviously influence the fuelling requirements but background compensation for manifold pressure would account for that. |
41:27 | NRG Racing Engines asks can you go into a bit more detail about the background fuel compensation with the MAP sensor, what would this fuel table look like and would you also utilise another timing table? So I probably will go more into detail on this when we get into the tuning side of things but this is nothing new, most ECUs do this, I don't have anything loaded up that I can show you but essentially it is just a case of when we double the manifold pressure, we also double the fuel being delivered and that's done in the background so we don't actually have to make really large steps in our fuel table so what we end up with in comparison to a fuel table where there was no background compensation like that, we end up with a flatter table that in turn gives us more resolution, in other words, we can make finer changes to the fuelling. |
42:17 | You don't need to utilise another timing table, the timing table is still just based on throttle position and I mean if we want to get really technical, the timing requirements of the engine will depend on air charge which is influenced by manifold absolute pressure but realistically, the timing table can stay just based solely on manifold absolute pressure, sorry on throttle position and you're not going to need to swing that massively, even in that previous example if there was a ram air effect, it's likely that the difference in air charge is going to be relatively minor and the engine's generally not going to be that sensitive to ignition timing to require a change for something so small. |
43:03 | Yeah so just to reiterate though, yeah the ECU will double the fuel delivery as we double manifold pressure so that our air/fuel ratio stays, or should at least stay the same, now I'm obviously, if we're talking about a turbocharged engine and we go from 100 kPa atmospheric pressure to 200 kPa or one bar of boost, we absolutely don't want to achieve the same air/fuel ratio at one bar of boost that we did at atmospheric pressure, but we do that in our fuel table but it just means that we don't need to make such dramatic changes to the numbers in order to achieve that. |
43:42 | Apline Vice Motorsports has asked, any thoughts on how close or far the throttle blades should be from the intake port, does it matter at all, assuming the same overall runner length? Look I am absolutely sure that there are some effects on this, I haven't got into this deep enough with my own testing and generally we're kind of stuck with what's available off the shelf, I mean in terms of the Jenvey throttle bodies that we've got for our K20, I mean this is what we're limited to unless you want to go and remanufacture the manifold that it bolts to which I'd say for most people is going to be unrealistic, we don't get to check back to back five different locations, it's just not financially viable. |
44:29 | Ultimately when we're at wide open throttle, should matter little anyway because at that point we've obviously got little to no restriction in the way. |
44:38 | Alright team, some great questions in there so thanks to everyone who has joined in, as usual for our members if you do have questions watching this at a later time in our archive, please ask those in the forum and I'll be happy to answer them there. |
44:52 | Thanks for watching and we'll see you all next time. |
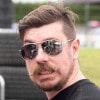