368 | Introduction to Resin 3D Printing for Motorsport
Summary
Most of us are aware of 3D printing and its use for motorsport and automotive design. You're probably more familiar with "standard" FDM 3D Printing technology (Fused Deposition Modeling) rather than Resin Printing. In this webinar we'll look at Resin or SLA (stereolithography) 3D printing, how it works, and how we can use it for our projects.
00:00 | Hey team, Connor here from HPA and welcome to this week's webinar. |
00:03 | This week we're going to be having a bit of an introductory look into resin 3D printing for motorsport or automotive applications. |
00:12 | So, we're going to get started by talking about how resin 3D printing works and how this differs from FDM or FFF , which is a more kind of traditional style of 3D printing plastics that you'd mostly be familiar with. |
00:26 | And most importantly how resin 3D printing is actually useful for us, how we can use it for our projects. |
00:35 | So, we'll get started by just covering off FDM, which is fused deposition modelling or FFF, fused filament fabrication. |
00:46 | Besides a few kind of copyright or product things around that, they're essentially the same thing. |
00:52 | And this is the more typical conventional way of 3D printing plastics , which you're all probably familiar with. |
00:58 | Basically, where it draws in a spool of filament that goes through a heated nozzle and then the nozzle traces the kind of cross section or outline of the part on the build plate as well as the infill and supports and everything, and then it builds that up layer by layer. |
01:17 | So, some people refer to this as kind of the hot glue gun method of melting the filament and laying it down and it basically melts and then solidifies on the build platform and then each layer solidifies as it builds up. |
01:31 | The alternative to this with printing plastics, or one of the alternatives, there's lots of different types of additive manufacturing now, but one of the most kind of accessible and cheap ones is resin 3D printing, which is what we're going to discuss today. |
01:48 | Resin 3D printing is also commonly referred to as SLA 3D printing and that SLA stands for stereolithography. |
01:58 | And this gets a little bit confusing with that name because if you're familiar with 3D printing or 3D scanning and mesh files in CAD, one of the formats for that mesh file is called an STL file and that is also standing for stereolithography, so we've got SLA and STL. |
02:18 | Both stand for the same things , but in kind of different uses there slightly anyway. |
02:23 | So, basically SLA, resin 3D printing, that's all you need to know. |
02:28 | So, let's get into how it works and we'll just jump onto my computer screen here and I've just got this little image I'll pull up to help kind of show a little bit of what I'm talking about here. |
02:45 | So, three main parts to it here, we have the build platform up here and this in this case is in an inverted SLA style setup where the print bed is above and it kind of brings up and the model is built upside down. |
03:00 | And this is the more typical way that we'd usually see SLA printers work, at least in the kind of consumer market anyway. |
03:08 | So, at the top here we've got the build plate here so that'll be flat under this part that you can't see and then we have the, it's called in this case the resin tank I guess, sometimes called the vat as this process is also called vat polymerisation and then at the bottom of the vat we have a clear screen. |
03:30 | So, in this case it's called the digital mask, it's often referred to as the release film or the FEP from the material that it's made out of and that's basically, yeah like I said, just a clear screen and that's a very important and kind of sensitive part of the whole process. |
03:48 | Then down the bottom here we have our light source and there's a few different variations in the light source here. |
03:56 | Typically in the kind of consumer market and what we'd mostly be using, this will be an LCD screen. |
04:05 | Although there's also laser based systems as well or DLP , which is a, I think digital light projection, but basically that projects light into the resin via kind of micro mirrors, an array of micro mirrors, lots of tiny little mirrors on a semiconductor kind of surface that controls that. |
04:29 | But typically we'll be using an LCD screen in most cases. |
04:33 | So, basically how the process works is the build platform here lowers down into the vat, which is full of resin, liquid resin, and then as the screen will basically mask out the cross section of the part, and I'll show you this a little bit more soon to give you a bit more picture of how it all works. |
04:57 | But it'll mask out the cross section of the part and then it'll light up and just the cross section will be exposed to the light source. |
05:06 | And basically because we're using a photopolymer resin, what that means is that light source will cure the resin, so the resin will solidify just in that cross section and it will stick to the build platform as well. |
05:20 | From here the build platform moves up a tiny bit and then the mask on the screen changes to the next slice or kind of outline cross section of the part and then that next layer is cured and it sticks to that previous layer and then basically from there it just carries on and builds up the part layer by layer, solidifying or curing each layer as it goes. |
05:46 | So, it's the same kind of slicing or building up of layers that most additive manufacturing processes work on , but it's just using a little bit different method to do that. |
05:58 | So, like we would typically use a slicing software for FDM 3D printing, we also use a slicing software for our SLA 3D printing. |
06:12 | The difference is that the FDM is creating a tool path of where to move the nozzle whereas in this case it's not so much a tool path, but more a library of these images for the cross section of the part for each layer for the mask or the screen to create. |
06:33 | But the slicing software or if you wanna refer to it as CAM software, which is computer aided manufacturing, similar to the software that would be used to create a CNC machined part. |
06:48 | The CAM software also gives instructions for things like the exposure times, so how long each layer is exposed to that light for, which is one of the most critical settings of SLA 3D printing, but also the speed at, which the build platform lifts up and also things like structural or the supports of the part as well among many other things that we'll have a little bit of a look at at the end of this webinar today. |
07:19 | So, I have a couple of images here. |
07:24 | Do I - just give me one moment to just find those. |
07:39 | One second. |
07:54 | That should be here somewhere now. |
07:56 | Ok so, there we go. |
08:00 | So, this image here is of our Elegoo printer, so with the hood down albeit, but after we've finished printing in that case we move on to these two systems here. |
08:12 | So, we remove the part from the build platform and then it goes into this here, which is the washing station. |
08:20 | So, that's basically just a tub filled with isopropyl alcohol and you can't see it , but down the bottom here there's a little kind of disc with a propeller on it just to kind of agitate the water and move it around and basically remove all the leftover or uncured resin off the part, because as we pull that part off the build platform it has solidified, but it's dripping with the liquid resin that it just came out of. |
08:45 | Typically before we jump into the station we just have another bucket of isopropyl alcohol, which is our kind of dirty wash, which we dunk it into first to remove the bulk of it and then we put the already kind of partially cleaned part into this just to keep the solution in here a little bit cleaner for longer. |
09:10 | So, we'll chuck it in there for 10 minutes or so while this runs and then pull it out of that and then the part is actually not fully cured yet. |
09:20 | It's in what we refer to as a green state, so it'll basically be a little bit kind of tacky or the surface will be a little bit soft on it. |
09:28 | So, what we do from there is we post cure it in this machine here. |
09:33 | So, basically sits on this turntable here and these are UV lights or to the same wavelength as what is used to cure the resin in the actual printer itself. |
09:45 | And we'll turn that on, depending on the resin that we've used to print it, for a certain amount of time and then that will just complete the final cure for the part and it basically means that it achieves the kind of target mechanical properties for the part in the end. |
10:04 | So, that's basically how the process works and I'll show you some of the parts in just a moment to kind of explain that a little bit better. |
10:15 | So, if I just find some other images, before we get into that, shouldn't have minimised that, sorry, jumping all over the place. |
10:28 | We'll just jump into a bit of a discussion about, you might be wondering why we would use this resin 3D printing over the more conventional FDM 3D printing and what kind of the key differences between the two of them are. |
10:42 | So, the first one being that the filament or material that we use in FDM 3D printing is a thermoplastic. |
10:50 | So, when we talk about plastics, there's really two main areas that they fit into, it's thermoplastics and thermosets. |
10:57 | Thermosets is what is used in resin 3D printing and thermoplastics is used in FDM 3D printing. |
11:04 | So, if you think about FDM 3D printing, as it brings that filament through the nozzle, it melts it and then it lays it down onto the build platform and then it solidifies and that's kind of the key part of thermoplastics. |
11:18 | They can be melted down and then re-solidify again, kind of over and over without too much degradation anyway. |
11:28 | The key difference there with a thermoset is once it cures, if it's exposed to temperature, it won't really melt like that, it'll just kind of go brittle and crumble and degrade. |
11:40 | So, that's why the two different kind of methods are used for these different materials. |
11:47 | The key benefit of SLA 3D printing over FDM really comes down to the surface finish and the resolution of the part. |
11:57 | So, I actually do have a part down here, one moment. |
12:03 | It's quite a big one. |
12:05 | So, this, if I just move this out of the way, bear with me. |
12:17 | This brake caliper bracket on the back here is just a 3D printed prototype. |
12:22 | It's a very simple one at that. |
12:25 | I've actually got a smaller part here I've just realised. |
12:31 | So, this is an FDM 3D printed part and you might not quite be able to see on there, but we basically have these layer lines here and as we build up more complex geometries, those layer lines kind of take away from the resolution of the part. |
12:48 | Whereas this is a resin 3D printed part, just a small version of a BBS E88 or LM wheel and you can already see the kind of detail and resolution that we get there. |
13:01 | So, that's kind of one of the key benefits of SLA 3D printing. |
13:05 | It can create very fine resolution and that's why if you Google SLA or resin 3D printing, one of the most common things that pops up is these kind of little figurines that people make for whatever games they use them for or whatever because they can create these little models with really high resolution and high definition and a lot of detail and then they paint them and use them for whatever they use them for. |
13:35 | This is another little part here, which is actually a calibration matrix and it just kind of shows, I know this isn't too zoomed in, but the detail that you can get out of one of these 3D printers. |
13:48 | So, this is just used to calibrate the exposure times for certain resins, which we'll talk about a little bit more in just a moment. |
13:58 | So, that's one of the kind of key benefits of the SLA over FDM. |
14:07 | One of the other main differences is because we have the lack of layer lines, we still get layer lines, but they're not so pronounced and we have chemical and physical bonding between the layers of the part whereas FDM is really just a physical kind of adhesion. |
14:25 | FDM prints are really prone to separation between the layers so if they're loaded in tension with those layers, the layers can kind of pull apart and this is what we call, well that's non isotropic. |
14:40 | So, an isotropic part shares the same mechanical properties really in all its directions, it's more kind of consistent I guess you could say and an SLA print is a lot more isotropic than a FDM print. |
14:56 | They are very strong, the SLA prints, but they're also very brittle. |
15:02 | If we jump under the overhead again here, this is just a part where I kind of printed the flange here a little bit too thin and I was actually drilling out these holes here and you can see it's very brittle and it just broke very easy. That is my fault , but it does show how brittle the part is. |
15:22 | So, basically if we're comparing the strength of the parts, of course the design and the geometry and everything and how the part's actually, loaded plays into that a lot as well, but generally if everything else is the same, an FDM part will be stronger although not loaded in tension between those layers. |
15:45 | The SLA parts will also be quite strong, but they're really brittle. |
15:51 | The thing to just note about that is there are some different resin types that can help a lot with that. |
15:58 | We're going to discuss those in just a moment basically. |
16:02 | If we're comparing the two processes as well I would say SLA 3D printing compared to FDM is relatively trouble free, it's quite easy to do whereas FDM 3D printing with certain materials, certain filaments can be quite annoying or troublesome depending on the printer as well, but SLA is pretty trouble free. |
16:27 | The downside of SLA in that case is it's quite messy, so the parts take a lot of kind of clean up, the resin's very messy and also the fumes and the resin itself is actually really bad for you so there's a bit more of a safety aspect as well. |
16:46 | We need to wear PPE when we work with it and so on. |
16:51 | Before we move forward I'll just make the note, if anyone has any questions that come up during this that are relevant to 3D printing, with any type of 3D printing, feel free to ask them in the chat and I'll do my best at the end to answer your questions. |
17:09 | So, let's jump in to talk about how it's useful for our projects that we're working on. |
17:16 | And this really comes down to the different materials or the different types of resins that we can use in our resin 3D printers. |
17:25 | So, basically these are divided into two more categories. |
17:29 | So, we have general purpose and engineering resins. |
17:33 | There's also dentistry and jewellery resins and things like that that we're interested in anyway, general purpose and engineering. |
17:43 | So, in the general purpose ones we have, I've got some examples here. |
17:49 | Water washable, this one here I think, yeah. |
17:55 | So, general purpose would be something like this here and this is just standard photopolymer resin. |
18:01 | Other examples of general purpose resin would be things like high speed resin, which as the name implies can just be printed at a little bit higher speed, basically the exposure time per layer goes down and that reduces the time spent on each layer and basically makes the print faster overall. |
18:23 | There's also precision ones and precision resins, which have lower shrink rates and things like that and just kind of hold their dimensions a little bit better and that's really good for printing really detailed parts. |
18:37 | And there's also things like transparent resins, so we'll get to this part in just a bit of a moment, but that's kind of semi-transparent, but you can get really transparent ones and you can polish them and things like that so much that they're really clear and that can be used for kind of optical purposes like lenses for tail lights or head lights or any other lights that you might be working with or you just want like a transparent part. |
19:07 | So, prototypes or functional parts, general resins can be really good. |
19:14 | The other kind of general purpose one is this one here, this is a water washable resin so basically all that means is we don't need to be working with isopropyl alcohol to wash the part off at the end, it just makes life a little bit easier. |
19:32 | So, we'll move on to the next kind of purpose, which is, the next group of resins which is our engineering resins. |
19:40 | So, we'll start by talking about high temperature resins and this here is Frozen's TR300 resin and that's a really good example of a high temperature resin. |
19:53 | In this case I'm using this for a project that I'm working on, which I'll show you in a moment, we'll get to that in a minute, but basically, yeah, high temperature resin, exactly how it sounds, it's good for engine bay components and things that are just going to be subject to high temperature. |
20:15 | Actually you have another, this part here, this kind of transparent one is actually printed with a high temperature resin and I have a photo of that part in place so that's my personal car, it's a 240Z with an L series with ITBs on it and that's got some resin 3D printed trumpets on the back there and cos these aren't a cross flow head, the header is right underneath that and I ran these for a month or so just doing some testing and there was absolutely no change to them so you can kind of see that this isn't obviously a motorsport application, it's just a street car, but they held up fine to that kind of engine bay temperature. |
21:01 | That's why they're tested on the back two cylinders as well, because they're getting less air flow there, they're a bit hotter. |
21:09 | So, that's the high temperature resins, we'll move on to some other ones. |
21:16 | So, as I mentioned before, the resins are quite, SLA printed parts can be quite brittle, but if we have something like this, which is branded as ABS like resin, sometimes these are branded as nylon like as well , but these are our tough resins and basically the idea is there to just up the toughness of the resin, which basically means they become less brittle. |
21:44 | So, that's really good for parts that are subject to impact or kind of abrasion as well like if two parts are moving against each other or going to be in a part outside the vehicle where it's just going to be subject to things like dirt and debris flicking up at it and so on. |
22:03 | There are some other resins, which I don't have any of here, things like flexible resins. |
22:11 | So, they're often branded as TPU like, which actually stands for thermoplastic urethane I think or thermoplastic elastomers. |
22:22 | So, these basically can be flexible or elastic and they're great for shock absorption or vibration isolation. |
22:32 | So, things like little pads to just damp any shock. |
22:37 | And there's also things like silicon resins as well, which we can 3D print seals or O rings or boots for tyre rod ends on steering racks for example or to cover rod ends or spherical bearings, things like that with silicon resins as well. |
22:56 | There's a lot more there as well, there's ceramic resins and there's all sorts of different stuff there. |
23:01 | And one of the kind of key benefits of SLA 3D printing is you can actually mix the resins together to kind of, within reason of course, get the best of both worlds. |
23:12 | There's composite resins as well that are like glass filled and things like that. |
23:19 | But yeah, that mostly kind of covers the different resins and basically how we would use them in any application. |
23:28 | Lots of the time how they're marketed, things like tough resins or flexible resins gives you a bit of an understanding of what they're going to be useful for. |
23:39 | So again, any questions that come up, feel free to ask them in the chat and I'll do my best at the end to answer them. |
23:45 | Before we get to that I'm just going to give you a little bit of a demo of how we would take a 3D model from our CAD software and then work towards 3D printing that with our resin 3D printer. |
23:58 | So, we'll just jump into Autodesk Fusion here. |
24:03 | And if I just turn on some of the other parts here. |
24:10 | So, this is a model I've kind of slowly been working on. |
24:15 | That's the front of our K20 powered CRX and I'm just kind of designing the intake system for it. |
24:22 | So, we have these Gen V ITBs here and we've got kind of a specific turned down manifold here because the previous one stuck up on a bit of an angle with the engine there and then if I turn on, got a scan of the inside of the bonnet there. |
24:40 | Basically, we had to cut a hole in the bonnet so the air filter or the intake was sticking out it. |
24:47 | When we're working to refresh this car, one of the kind of main things we want to do is keep the whole intake under the bonnet line to keep it out of the airflow, but also just make things look a little bit nicer. |
25:02 | And we're basically going to create some holes in the front bumper here or maybe use this duct and feed our intake from there. |
25:10 | So, part of that is basically trying to keep the throttles and the trumpets here under the bonnet line. |
25:19 | So, I've just been kind of designing these parts and they're going to be included as a worked example in part of our 3D printing course that we're working on at the moment. |
25:30 | And the reason for 3D printing these parts as opposed to working with a more kind of traditional manufacturing method, one of it comes down to the shape of them being turned down like this. |
25:42 | It doesn't really work if you want to machine them on a lathe for example. |
25:49 | The other thing is we're going to do a few different lengths of them, because that basically has an effect over the power band of the engine where it makes peak power, so we're going to try three different lengths and see what basically is the best length for our setup. |
26:10 | So, being able to create them quickly and cheaply as well is really good for just prototyping and testing like that. |
26:20 | In the end if they hold up to the temperature, because it's going to be directly in the airflow at the front of the vehicle, it should be kept quite cold, we'll probably end up running them, otherwise once we've kind of proved our theory here, we might move to getting these machined or can even electroplate the plastic as well to kind of help there and there's all sorts you can do. |
26:42 | Or maybe we'll 3D print them out of a metal. |
26:45 | The other kind of thing we're kind of working on here is you'll see this fuel rail here with the injectors at the kind of bell mouths of the velocity stacks or trumpets. |
26:58 | So, we're going to work with some primary injectors, which we're going to install right in the port here and that should give us kind of good response and drivability and then the idea around having the injectors at the bell mouth as we get at high RPM and high airflow through the intake, we get some really good air fuel mixing for a more kind of efficient combustion process and hopefully a little bit of power gains at the top end as well. |
27:28 | And I've kind of taken inspiration for this design from the BMW CSL Group 2 cars I think they were. |
27:37 | Rather than having the fuel rail here out in the airflow in the middle and the injectors going straight down the middle, I've just kind of put them through the wall of the part there and I think that just having these little bosses here like this shouldn't impede on the airflow too much , but what we're going to do is all this testing to kind of prove these theories. |
28:01 | So, for this I've 3D printed some parts, which I have an image of here. |
28:09 | I haven't printed the middle two yet, but these are resin 3D printed trumpets here with the mounts on them as well for the fuel rail and they are 3D printed out of our TR300 resin here. |
28:31 | And this is, again jumping back to this part, just an example of one of those parts that I made a few mistakes on this one, the beauty of prototyping, I didn't get it right the first time. |
28:41 | And I can just go back and print some other ones of those. |
28:45 | So, yeah that's one of the parts. |
28:49 | So, we'll just show you how you'd work from this model through to printing one of those parts using the slicing software. |
28:57 | So, if I jump up here to Utilities tab in Fusion, I can go under the Make tab here and go 3D print. |
29:05 | So,metimes this works with the slicing software we're going to use, we'll give it a try first if we click Print Utility. |
29:12 | And then I'll go Custom, I'm going to have to, yeah, oh, looks like it's already selected it so we've got Chitubox Basic, which is one of the most commonly used kind of SLA slicing softwares. |
29:28 | And then I'm just going to select one of the parts that I want to print. |
29:32 | The format here, STL binaries, just a good mesh format that we can use for this. |
29:38 | The unit types, I want to keep in millimetres because that's what I designed the parts in, and refinement I'm just going to keep it high, all on the default settings. |
29:46 | Sometimes, yeah, it doesn't look like it's going to do it for some reason, it's taken me over to it , but it's not dropped that file into the workspace there. |
29:58 | So, rather than doing that, I'm just going to jump back here, do the same thing, 3D print, and I'm going to go Export, select one of those, STL, if I go OK, I'm just going to save that to the desktop, yeah, as body 6, then if I jump over here, I'm just going to jump onto my desktop, find body 6, and drop it in. |
30:22 | So, simple as that, I've just dropped in that mesh file straight into the workplace there and this is kind of showing the build platform of the 3D printer. |
30:34 | So, the first thing that we need to do is basically decide on the print orientation or the orientation that we want to print the part in, because that has some kind of significant lead on effects to how the part is built and also the surface quality that we'll get to in just a moment. |
30:56 | So, if we jump in here, I'm just going to rotate the part and I'm going to bring it around to this position here, just till we get 90 degrees. |
31:07 | So, this would be the typical orientation that we'd print the part in for an FDM 3D printer, the kind of more conventional 3D printing method. |
31:16 | And typically we wouldn't actually do this for an SLA printer, because we'd usually print it on a slight bit of an angle, something like this for example. |
31:31 | And the reason for that basically comes down to the surface finish of the part and also as we build up the part, this kind of large cup shape of it is going to basically seal off the release film and as it pulls up it's going to make a big suction cup and the release film is quite fragile I guess you'd call it and we don't want to create too much force on the release film from a suction cup, because that'll basically pull the part off the build platform and it can also damage the release film. |
32:09 | The release film is like a wear item, it's a part that needs to be replaced every now and then, the more force we put on it, the more chance of our print failing , but also the quicker it wears out. |
32:19 | So, we just want to avoid that. |
32:21 | So, typically in this case we'd kind of lean the part over like this. |
32:27 | Now, the issue is we need to create supports for the part and those supports will contact the part all underneath here and they will create a little witness part, little witness marks, like little pimples on the surface of the part. |
32:44 | And basically I just want to avoid that on any surfaces that we'd see. |
32:48 | So, an orientation like this would be ok, but we can actually bring it around and print it like this. |
32:57 | And that will reduce the amount of supports , which I'll show you in just a moment , but again we're going to end up with that suction cup issue, but if I just bring it slightly off the print bed here, then there's basically just a little gap where that pressure will be relieved so we won't have that suction cup for example. |
33:16 | We won't dive into it too deep, there's a lot more things that go into the, considerations that go into the print orientation of the part, but we'll just leave it like that. |
33:28 | So, from here if I just jump over to the supports tab here, then I can just generate some supports. |
33:36 | So, you can see this has kind of made this raft on the bottom here because the part's not touching the print bed and that's going to be basically how the part sticks to the print bed. |
33:47 | And then we can choose between light, medium or heavy supports and we can basically just create supports automatically and you can see there that it's done that. |
33:58 | And you can see all these kind of yellow, sorry orange parts through there is where the supports are going to be touching the surfaces. |
34:07 | In this case, and like how this part was printed, you might not be able to see under the overhead here, there's just these kind of little raised parts here and they can be easily sanded off with a bit of sandpaper. |
34:23 | But you can see the top part there is nice and smooth and same on the inside here, the kind of critical surfaces. |
34:31 | The bottom of the part was left with a lot of marks, but that isn't going to be seen so again that can just be sanded flat. |
34:39 | There's a few different orientations that we could use here and play with for different results , but that just gives you a little bit of an insight into maybe what to consider. |
34:48 | So, if we jump back to here, the other thing that we need to do is determine or set up the resin that we're going to be printing with. |
34:58 | So, through here we can go to this resin alliance page and that basically has a big library of these different resins that we could choose. |
35:08 | So, if we go resin type, you can see here a lot of the resins that we talked about before, flexible, standard, rigid, tough and so on. |
35:18 | If we go high temp resins here, we can see here we have the TR300. |
35:24 | So, I'll just grab that and then I think we just click application there. |
35:31 | So, I actually already have this part downloaded because I've used it. |
35:36 | So, we'll just exit out of there and if I jump into slice settings here, you can see I've got these profiles here with TR300 and if we scroll down here we have the setup for the print. |
35:51 | So, a key point here is being that exposure time. |
35:54 | So, for this resin, the exposure time is 1.7 seconds. |
35:59 | So, that means each layer is exposed to the light for 1.7 seconds before it moves on to the next one. |
36:06 | If you increase that a lot, then it will be overexposed. |
36:11 | If you decrease that a lot, it will be underexposed. |
36:14 | So, we want to kind of strike that balance there. |
36:17 | Again, we won't get too deep into that. |
36:19 | There's some other settings here like the bottom layer count and so on. |
36:24 | It's all good in this case for this discussion to just leave these as the default settings just to keep things simple and in the future maybe we'll get into discussing these in a little bit more detail. |
36:36 | And the rest of this is basically just the setup of our printing machine. |
36:41 | So, we're using the Elegoo Saturn 4 Ultra printer in our case. |
36:47 | And we can just hit apply to that. |
36:49 | If we did want to change the printer or set up a new printer, we can just jump in here and find any of the printers in here that we're going to use. |
36:59 | So, that's all that was done to set up our one there. |
37:02 | And it basically just automatically has this library of all these different printers in the slicing software. |
37:09 | Just cancel out of that. |
37:11 | So, that's basically that done and then we can hit slice and that's just going to generate the images for each slice layer of the part. |
37:21 | This is always a little bit slow going here, but if I drag this down here, you can see what those cross section images are going to look like. |
37:29 | And this is what we discussed as a part. |
37:31 | So, these are the mast layers that are being built up and exposed to the resin one by one. |
37:38 | So, it has, I'm not sure what it says here. |
37:43 | It's time, it's saying it's taking almost four hours to make this one. |
37:48 | And if I drag it right up to the top, there's 1,871 layers in this case. |
37:55 | So, yeah, hopefully that gives a little bit more kind of idea about, yeah, insight into the slicing process there. |
38:05 | From here I can just hit network sending and then send it to our printer over WiFi in our case. |
38:13 | The other thing that I just wanted to discuss before we move on is printed parts. |
38:20 | So, printing threads, so threaded parts for making fixtures and so on. |
38:25 | In this case these two holes down here is what our fuel rail mounts mount to. |
38:31 | And on this part they're actually not threaded, but on the other ones that I've done they are threaded parts. |
38:37 | Because of the fine detail of SLA 3D printing I was actually able to directly print those threads and then just run a tap through them to just chase them and tidy them up a little bit. |
38:49 | So, that's kind of one of the benefits there. |
38:52 | It's a little bit tricky to drill and tap these parts, because they are brittle in this case , but it can be done. |
38:59 | In an FDM part here, this is actually a part that I was just testing threaded features on, so one of these holes is drilled and tapped, the other is just chased with a tap after printing the threads and then this other one here has this heat set threaded insert. |
39:16 | You can't use those heat set threaded inserts for SLA 3D printing because of what we talked about with this being a thermoset, you can't melt the plastic and it will re-solidify, it'll just kind of degrade and crumble and crack. |
39:34 | But you can use the threaded inserts with the thermoplastic from FDM. |
39:39 | So, that's just a little note on the threaded features. |
39:45 | In the case of SLA, you can print the threads and just chase them with a tap is a pretty good option. |
39:52 | Yeah, I'll just jump into, see if there's any questions and we'll go from there. |
40:02 | Alright, Lechowz07, "How are you guys liking your Saturn 4?". |
40:06 | So, far so good, hasn't given us any issues at all, every print I've done besides my own mistakes has been really good and hopefully we'll be bringing you some more content on that in the future. |
40:19 | But yeah, so far so good, I think that printer is around $1200 NZD, so what's that, $800 or so US dollars. |
40:31 | So, it's relatively cheap and affordable, well that's all relative I guess, but compared to some of the other options, it's quite an accessible printer and yeah, so far it's been great. |
40:43 | Mark, "Are there any considerations you need to make when designing for resin printing instead of FDM printing?". |
40:52 | Yeah, definitely, when you're talking about FDM printing, one of the main things you need to consider is like the layer lines and things like that. |
41:02 | For the SLA 3D printing, one of the benefits is you can include a lot of detail in the part, but maybe you just need to make things thicker for example around the brittle things, but I also have a bit of a cheat sheet, let me just find it one moment. |
41:33 | So, this here is just a design rules thing from Protolabs and this has the design rules around 3D printing and down here we've got FDM and SLA here and then different kind of design rules around the size of features and so on. |
41:50 | So, something like this can be really good to follow. |
41:55 | I would say when it comes to design for manufacturing or DFM considerations, these are some specific ones around feature sizes. |
42:04 | You also want to think about kind of the limitations of the process, so that might just come down to the size of the printer that you're working with or the resins that you're working with, what their limitations are around strength, how big you need to make parts or how thick or so on. |
42:26 | But what you also need to consider is playing to the strengths of the manufacturing method as well so it kind of justifies its use. |
42:35 | So, for SLA 3D printing parts that are kind of big bulky parts might be better printed with another process whereas something for SLA with lots of fine little details would maybe be more suitable. |
42:50 | Hopefully that helped a little bit there. |
42:58 | C. Interante, sorry if I butchered that, "What's the best easiest program to learn modelling from zero knowledge on modelling?". |
43:06 | We push Autodesk Fusion, it was commonly known as Fusion 360 a lot. |
43:12 | That's what we use and that's what we use in our course. |
43:15 | It's very accessible, it's free for private use and it's really designed around being intuitive and easy to use. |
43:23 | A little bit of issues can come in if you're used to working with SolidWorks for example and you've spent years doing that and then you come to Fusion. |
43:33 | It's pretty easy once you know how to know modelling to switch between programs , but some people might find SolidWorks more intuitive than Fusion, but I would say generally speaking for people just getting started, Fusion is a lot more intuitive and it's kind of targeted or designed around people that aren't familiar with more traditional CAD modelling in the way that it makes it easy to find functions and tools and so on. |
44:05 | But it's extremely powerful and it's used all the way up to the highest levels in our industry. |
44:11 | So, we recommend Fusion and saying that I've had some good experience with Onshape as another option and then past that things like SolidWorks and so on, but they get a lot less accessible as you kind of go more in that direction. |
44:31 | Although SolidWorks for makers offering is an option as well. |
44:35 | But of course I would recommend looking at Fusion and then doing that with our 3D modelling course as well. |
44:41 | That would be a good way to get started and using Fusion for that use is completely free. |
44:48 | You also asked, "Also is there a good cost effective scanner for DIY or hobbyists and when scanning does that speed up the process of creating a part from scratch?". |
45:00 | So, for DIY or hobbyists a good scanner that I'd recommend is the Shining 3D EinStar. |
45:11 | That comes in at about $1000 or $800 or so US dollars. |
45:17 | So, I definitely recommend checking that out. |
45:19 | Of all the kind of cheaper scanners I've used, that's really been the only one that I could recommend to anyone. |
45:27 | The other ones I just haven't had a good experience with. |
45:31 | So, check out the Shining 3D EinStar and yes it absolutely speeds up the process so much. |
45:39 | You don't have to keep going back to the part. |
45:41 | It depends what you're working on of course, but going back to for example the engine bay and taking measurements and so on, if you can just work off a 3D scan it speeds it up so much and I find you just get a much better result at the end because you can kind of picture everything that you're working on together. |
45:56 | So, I'm a big advocate for 3D scanning. |
45:59 | Since we've had one in the workshop I use it for almost every project. |
46:03 | Whether that's a good thing or a bad thing I'm not sure, but it's really good. |
46:09 | Chris Crump, "What would you recommend for printing a coil cover for a 4G63? Lots of heat in there.". |
46:16 | So, if you were going to print it out of a plastic, I wouldn't be using SLA in that case, I would be, if you're going to print it on a kind of more consumer grade 3D printer, it would be printed out of nylon, probably glass filled nylon, PA11, polyamide is nylon, same thing I guess. |
46:37 | PA11, glass filled or carbon filled is probably going to be your best bet when it comes to withstanding that heat, but for a turbo application, especially in a race car use, I'd probably print the, yeah, oh coil cover, coil cover. |
46:58 | Yeah, yeah, you could probably print that and then like use that as a prototype and then maybe get it machined or make it from a composite or something like that as well. |
47:10 | I was thinking of coil bracket for a second, yeah, but your best bet for heat temperature for plastics anyway is going to probably be, yeah, nylon 11, glass filled or carbon filled, just yeah, the composite reinforcement adds a lot in the heat deflection temperature or the heat resistance anyway. |
47:37 | Yeah, and that's basically all the questions we've got there, so hopefully that's helped some of you out there and hopefully that's given you a little bit of an insight into an alternative type of 3D printing anyway. |
47:50 | That can be of a lot of use to us and we'll be hopefully covering some more on this topic in the future and keeping you guys updated with the projects that we're working on and using these parts with. |
48:04 | So, yeah, thanks for joining us and we'll be back next week with another webinar. |
0:35 - Fused deposition modelling / Fused Filament Fabrication
2:45 - Resin 3d printing / stereolithography
8:00 - Elegoo example with post-printing curing procedure
10:28 - Resin versus FDM/FFF printing
17:09 - Practical application of various resin materials
23:45 - Take model from CAD to resin 3D printer
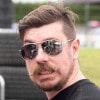