369 | Budget 3D Scanner - Scan Off!
Summary
Is 3D scanning only accessible for top-tier companies with big budgets? In this webinar we will compare the performance of four different scanners from four different brands (all under $1000 USD) to see how useful they might be for your own project.
00:00 | Hey team, Connor here from HPA and welcome along to another one of our webinars. |
00:04 | This week we're going to be comparing budget 3D scanners. |
00:07 | So, we're going to be looking at the performance and usability of four scanners that are all under the $1000 US dollar price range. |
00:16 | At HPA we're lucky enough to have a Peel 3 scanner, which is great , but it is at around the $10,000 US dollar price point, which is what we'd consider more of a professional level 3D scanner. |
00:33 | And this is really out of the price range for a lot of the enthusiasts just getting started in this space or maybe just working on their own cars and such, not in a professional environment. |
00:45 | And a lot of the questions that we get asked around more product specific questions anyway are really on scanners around that $3000 price range or below that. |
00:57 | So, today we're just going to start out our discussions around scanners in that price range looking at the really entry level stuff anyway under $1000. |
01:08 | So, we've got four scanners we're going to be looking at today. |
01:11 | Right here we have the 3D Maker Pro Moose, we have the Revopoint Range 2, we have the Creality CR Scan Otter and we also have the Shining 3D Einstar, which is probably the one that we're asked about the most. |
01:29 | So, you might be thinking to yourself what about the Raptor or the Raptor X, what about the Revopoint Pop 3 or the 3D Maker Pro Seal and yeah all of these companies that we're talking about here or most of them anyway have other products or other models of scanners, usually with ridiculous names like Moose and so on. |
01:54 | And a lot of them are in this kind of similar price point range as well, under a few thousand dollars. |
02:02 | So, I'll just go through the reasons for choosing the scanners that we've got here. |
02:08 | One of the main objectives when we're looking at these scanners is I wanted to find something that's relatively cheap that would be good for scanning large parts. |
02:18 | We have the Peel 3, that's great and we also used to have this Peel 2-S, well we still have it , but we used to use that before we had the Peel 3. |
02:27 | That's a great scanner for really detailed small parts, all the way scanning something like an engine block, something like that , but it really struggles with working with larger areas like scanning engine bays or body panels or so on. |
02:41 | The Peel 3 is great for that , but again it's more suited towards kind of mechanical design and scanning things like the size of an engine block for example. |
02:51 | So, yeah, I wanted something that could scan something big so that's why something like the Range 2, I chose that, is suitable for kind of larger parts compared to maybe the Peel 3 for example. |
03:04 | Ideally what you'd end up with as a scanner, especially at the entry level, that would be able to scan anything from a really small detailed part all the way to something quite large as well, but that's kind of a balance that can be hard to strike. |
03:19 | These are also a lot of the scanners that we've been asked about probably the most commonly so those were kind of my first attention I guess. |
03:29 | And then if you watch today's webinar and have a look at how these scanners go, then you should be able to jump on their webpage and kind of compare the specs of how they compare something like the Revo Point Range 2 to the Peel 3 and get an idea for how those two scanners should compare. |
03:52 | What we'll do is we'll just jump over onto my computer screen and I have a bit of a spreadsheet here, which we can probably share along with some of the 3D scan files as well with you guys. |
04:05 | We'll probably dump those into the forum if you wanna go check this out after the webinar or in the next few days I should be able to get all that loaded up onto a forum post there. |
04:15 | So, like I said we have these four scanners here and I've also jotted down some of the notes on the Peel scanners that we've used as well down the bottom here just for kind of reference. |
04:30 | So, let's just start off with looking at the 3DMaker Pro Moose. |
04:34 | So, this is the cheapest scanner we're looking at, it's about $600 US. |
04:38 | It's the only one that's blue structured light, all the other ones are actually infrared till we get to the Peel ones. |
04:44 | The early ones were white structured light, now the Peel 3's infrared as well. |
04:51 | All of the scanners we're looking at today can work with Mac and Windows, which is good for me cos I'm working on a Mac and oftentimes with CAD software, it's just limited to working on Windows. |
05:04 | For example, the PO scanners, it's only Windows so I can't just be a bit more portable and use my laptop and go to another site for example and scan something there, it's a little bit tricky. |
05:18 | The Einstar wasn't originally on Mac, it was just on Windows , but really recently they've just released Mac OS version of their software as well. |
05:28 | You'll notice up here, if we're looking at the accuracy and resolution, the 3DMaker Pro kind of quotes these really great numbers, 0.03mm for accuracy and 0.07mm for resolution and you can compare that to some of the other ones here as well. |
05:47 | As we get into today's thing, we're going to do a webinar, we're going to do a bit of a look into the accuracy and actually take a few measurements and kind of prove that sometimes these numbers quoted off the website aren't actually as accurate as you might think or maybe just take them with a grain of salt. |
06:04 | The capture area, so that's like really the field of view, so how much view the scanner can see. |
06:12 | For the 3DMaker Pro Moose is 200x100 so that's really quite small compared to these other ones, especially since these are all really ones that I chose to be able to scan larger areas and the working distance is kind of that depth of the field as well. |
06:28 | So, how close the scanner can be to something in capture data and how far away it can be before it loses it and stops capturing it. |
06:37 | That capture area, the field of view that we talked about earlier, really depends on where in that working distance you are because if you imagine the scanner works kind of by triangulation, so it extends this kind of pyramid of view out from the scanner, the capture area at the start of that working distance is going to be smaller than it is at the end of the working distance. |
07:03 | As shown here with the range here, so it says near is 220x425mm and far is 860x1380. |
07:12 | So, it changes quite a lot depending on where that working distance is so a lot of the time when a manufacturer is kind of quoting these specs, they will just use the far distance capture area, because it seems a lot larger. |
07:27 | So, again something to just be aware of when we're looking at these specs and comparing them. |
07:32 | They can all capture colour, texture in this case, for us doing mechanical design for motorsport things, it's not really necessary, but it can be nice to have if you wanna make a really cool looking scan or something. |
07:45 | And then the tracking method, so the method that they can position themselves and track the movement of them relative to the object. |
07:54 | In the case for the Moose, it's just geometry and texture, same for the range too, whereas the Otter and the Einstar can all use texture. |
08:06 | And then down the end here we just have our recommended requirements. |
08:10 | Most of them in this case are asking for about 16 gig of RAM, but really the outlier here is the Einstar, which is, I think, really wanted 32 gigabytes of RAM and it just has a lot more processing requirements to run the Einstar. |
08:32 | I've noted up here what I'm working on today, so I'm just working on my MacBook Pro, it has a M2 chip with 16 gig of RAM. |
08:41 | So, it should be more than capable of working with the Moose, the Range 2 and the Otter, but it is not up to the requirements of the Einstar, but it actually hasn't been a problem working with it to be honest. |
08:55 | So, yeah, again, that's something to just consider with certain scanners like the Einstar. |
09:05 | Compared to the other ones, there's the investment of the scanner itself, but if your computer's not up to the task then that might be another investment or upgrade cost that you need to consider as well. |
09:18 | A lot of time people go out and buy a scanner that's really great and powerful and then they find out that their computer's not up to it, then they go and need to spend another $3000 to $5000 or something like that on a more beefy computer as well. |
09:32 | So, again, something to just be aware of. |
09:35 | I kind of touched on these other scanners as we talked, but let's just quickly run through them. |
09:40 | So, we've got the Range 2, that comes in about $200 more than the Moose. |
09:44 | It's infrared, works on all the operating systems, the accuracy quoted is a little bit less than the Moose , but again we'll see in the future that's not such a problem. |
09:57 | Has a massive working distance though, it's really designed for scanning large things. |
10:03 | I think that's probably why they use the term Range 2 as the model name. |
10:09 | The Otter, similar price point, very similar specs there to the Range and again designed for scanning quite large objects and basically the same thing again for the Einstar. |
10:29 | But the Einstar steps up a little bit in price to just under that $1000 price point. |
10:35 | Just quick disclaimer here, this is obviously relevant at the time where we actually got these scanners, I wrote down all these prices and then it's probably changed to now when we're actually filming this content and then maybe by the time you're watching it at some point, if this goes on our YouTube channel then it might be a little bit more expensive again or cheaper or I'm not sure, it all moves and new products are being added all the time, but we'll talk about that a little bit more as we progress. |
11:07 | So, we scanned basically for this kind of scan off that we're doing here, I scanned a few different objects or targets or whatever we want to call them. |
11:21 | So, the first one I did was the engine bay of our little AE86 or more accurately AE85 project. |
11:31 | So, I don't actually have the photo up here, but I'll show you a little bit more about that as we progress. |
11:39 | The engine bay was quite a light colour, but it had even lighting and it has a lot of features to track and why we'd want to scan an engine bay would be maybe to design things like brackets to hold other components, maybe we've got a scan of an engine in there as well with the engine mounts. |
12:00 | And we want to design engine mounts, maybe we want to design some plumbing or other just general components that would be in the engine bay. |
12:08 | We also scanned our SR20 billet block, so we've got a Mazworx Pro Street billet block engine in our workshop. |
12:17 | So, quite a shiny aluminium billet block, but it has a lot of good features to pick up on as well. |
12:25 | Why would we want to scan this? Maybe again we're going to mock it up in the engine bay scan, design some engine mount brackets and so on or just design bolt on parts for our engine as well. |
12:37 | The final thing I scanned was the rear arch on our CRX. |
12:42 | So, we have a K20 swapped CRX endurance car project that we're kind of working on when we get the chance. |
12:51 | And this is basically, the rear wheel arch over the wheel was included in the scan. |
12:58 | I'll show you these scans soon. |
13:01 | The actual panel itself is pretty simple and it's somewhat reflective with kind of shiny paint, but because it's a project at the moment, it's also got some primer and kind of body work going on as well as some plastics kind of side skirts on it. |
13:19 | Why would we want to scan something like this would be to design body work for example, in this case we scanned that so we can design a kind of rear over fender. |
13:29 | But we might also want to scan the whole exterior of the car to develop things like aero or even in some cases we can scan a vehicle, bring that into CFD and basically that's what they do for video games as well. |
13:43 | I've also scanned a lot of other things with these scanners, but those are the kind of recent ones so the ones that I'm going to focus on today. |
13:51 | So, what we'll do is I'll open up each one of these scanners, plug them into my computer, I'm going to do a quick scan of the engine block, I think that's half the engine block of a FA20 out of a GT86 behind me and while I'm doing that I'll just have a little bit of a discussion of the notes that I've taken from doing those scans with these here. |
14:17 | So, what we'll do is just start with the 3DMaker Pro Moose. |
14:25 | I'll bring that engine block over and dump it onto the turntable we've got here. |
14:33 | Yeah,, bear with me. |
14:43 | That's looking pretty good. |
14:45 | Ok, we'll jump under the overhead really quickly just so you can have a look at it. |
14:49 | So, this is the cheapest scanner we've got and as such it just comes in this box here. |
14:54 | And it's a pretty simple kit that you get with it so quite a small scanner, yeah it's pretty basic really. |
15:03 | We have a power source and then just our cable here as well. |
15:08 | So, what I'll do is just get this plugged in. |
15:11 | So, in this case not all our scanners actually need power sources, but this one does. |
15:20 | So, I have that, I'll just have to actually get the adapter to our New Zealand style ones. |
15:31 | Like that. |
15:36 | Plug that into a power point. |
15:42 | So, this is something that I just wanted to bring up is the amount of kind of cables and stuff that come with these scanners because there's a few differences here as we kind of work through these. |
15:54 | With some of the scanners actually not requiring many cables and so on and other ones really do and, sorry I'm just trying to find my adapter. |
16:14 | Oh yeah, there they are, so just a little USB A to C adapter so I can plug it into my Macbook. |
16:20 | Yeah, and it does make a big difference, the difference between the amount of cables that we're working with. |
16:27 | Cool so, we'll just open the scanning software here for this , which is this JM Studio software. |
16:35 | And get everything set up here. |
16:38 | So, I'll just put the block over here. |
16:47 | Alright, so once we're in here we're just going to click start scanning and that gets us set up to go. |
17:00 | Cool so we can see the preview on the screen and kind of this part of the engine block that I'm looking at and you can straight away see really how small that is and that's going to make a big difference when we get to the other scanners as well. |
17:16 | So, while I'm scanning this I will just kind of read through my notes of scanning those other scans and basically tell you how it went and then afterwards I'll open up some of those scans, so we can actually have a little look at them as well. |
17:30 | So, if I just click scan here you can see on the left side of the screen just showing me where I basically, the distance that I'm working with. |
17:41 | So, at the moment it's saying excellent, if I go out it's saying too far and if I move in it's just too close and they all kind of have rough scales like that. |
17:51 | So, we can just see the data we're collecting and how we kind of need to fill it in. |
17:57 | Alright, cool so basically when I was scanning the AE86 engine bay initially it appears to pick up a lot of data and kind of do well like it all looks like right now. |
18:14 | But then I basically ran into a few kind of errors creeping in and as I kind of work back and forward here scanning the different parts of this and then moving back to areas that I've scanned before, it's not, oh yeah you can see that on this, the far left, the top left corner of the green square at the moment, we're basically already getting a part where that hole is misaligned to where it was previously scanned and I saw a lot of errors like this creeping in with the engine bay where we, yeah basically it scans that hole in the wrong part and then if I move off it you can see that that scan data is already incorrect. |
18:54 | Again, if I move back over to this side, looks like yeah that middle hole there on the block is a little bit out as well. |
19:04 | So, it just kind of seems quite prone to those errors creeping in and then us ending up with basically problems in our scan where they're not fully accurate. |
19:15 | It does seem to capture data quite well in saying that, but this limited field of view that you're working with here makes it really kind of small and inefficient when it comes to scanning compared to the other ones that are more kind of designed for scanning larger things, they capture a wider range of kind of data as you're working around. |
19:40 | So, I'll just leave it there for now. |
19:44 | The other thing I want to note is there's actually no start-stop button on the scanner, not that I can see anyway. |
19:53 | So, everything needs to be done off the screen here. |
19:57 | And then something else I noticed, which was quite annoying is if I stop the scan like this, one it takes quite a long time for it to actually process this first initial process. |
20:10 | When I was scanning the engine bay what I captured, it took about 30 minutes to kind of process that original scan. |
20:21 | And then what I found after that is I can't just kind of pause and then restart the scan, I have to basically then take another scan and then merge them together later on compared to working with a pro level scanner or even these other ones here. |
20:35 | You can just kind of start and stop and be like oh okay I haven't captured that bit of data, I'm missing a chunk over here, I'll just jump back in and get that. |
20:43 | This makes it really kind of difficult to jump in and do that. |
20:49 | What I would say about scanning the engine bay, it was just completely inefficient, basically it would take too long. |
20:55 | You could scan little small areas of it where there was maybe some mounting holes to design a bracket or something like that and it might be okay, but to scan the entire engine bay I basically just gave up after a while because it was just going to take too long. |
21:12 | So, while this is processing still I'll just say move on to talking about the billet block. |
21:20 | So, it scanned okay on the kind of shiny aluminium billet block, but it actually, it didn't, there's a few kind of black parts on that block. |
21:33 | What I'm going to do while I'm talking is just kind of airdrop my photos of that to myself as I should have done this beforehand. |
21:42 | So, that's the engine bay, sorry about this, and that's the billet block. |
21:53 | Cool, I'll have those on my computer screen in just a moment to show you. |
21:57 | So, there's a few kind of black parts on the block, if I just open these up now. |
22:03 | So, like this bracket here for I think the dry sump pump, that wasn't picked up by this scanner at all and neither was this kind of AN fitting over here. |
22:13 | It did pick up the shiny aluminium block, no problems, but yeah it wouldn't pick up the black stuff and I would probably put that down to the fact that this is a blue laser scanner and not an infrared one just because that was the only difference between this and the other scanners and they picked up those black parts with no issues. |
22:32 | So, that's probably pointing in that direction. |
22:38 | So, again those errors were creeping in like we were seeing with this, probably more so with the billet block because it has a few less features. |
22:47 | So, basically as it's moving between it's just not tracking and keeping its position really well and the holes end up being misaligned as you move back over them. |
22:57 | Again, my notes were that that initial processing of the scan was really slow as you can see here, I'm probably just going to stop this soon because it just takes too long. |
23:08 | Yeah, and the tiny field of view just takes quite a long time to scan it. |
23:14 | So, when I moved onto the rear wheel arch of the CRX, which I actually don't have a photo here on me , but it was basically just a waste of time. |
23:25 | That field of view is far too small so when you're working on quite a plain body panel and it's moving around as you move from one spot to the next it basically just sees the same thing twice and it just makes this big error and it just doesn't work at all. |
23:39 | So, waste of time on that. |
23:41 | It was ok on the block as you just saw here, it's probably usable, you could work with it. |
23:47 | But yeah it's not ideal I would say. |
23:52 | This processing is moving along a little bit more now , but it's probably taking a bit long here. |
23:58 | I would just say on the rest of the software here it is easy enough to use. |
24:03 | The lack of being able to pause and restart is a bit of a problem to me. |
24:10 | If it is possible to do it then it's not very obvious or intuitive. |
24:15 | I've done lots of 3D scanning and if it's not immediately obvious then it's probably lacking. |
24:21 | In that case the editing tools and everything in the software as well aren't great. |
24:29 | It has basic stuff that you can work with, but again it definitely seems like it's on the cheaper, kind of more entry level and somewhat gimmicky side of things. |
24:40 | I am going to stop that there, this is just taking too long and we need to move on to our other one. |
24:45 | I'll just hit delete there and I'm going to close that down. |
24:52 | So, what we're going to do next, so just unplug that one and we will move on to our next scanner. |
25:04 | So, next up we have the Revopoint Range 2. |
25:11 | And again we have some wires and everything that we need to plug in here. |
25:16 | So, if I just move the block out of the way, I'll show you it under the overhead. |
25:21 | So, definitely a much larger unit. |
25:24 | Also in the kit here it comes with some other parts. |
25:29 | So, first of all when you step up to the next three they come in these cases , which is quite handy. |
25:35 | And then this one comes with this kind of little power bank handle and some other parts and also this here. |
25:42 | So, this is one of the key points, this is actually for holding your smartphone. |
25:47 | And not only will the Range 2 work with a Mac or a Windows computer, but it will also just be able to connect with Bluetooth or WiFi I think it is to your smartphone. |
26:01 | So, you can just scan from your smartphone, you don't need to be tethered to your laptop. |
26:09 | And that makes it just a little bit more simple to do so. |
26:13 | So, let me just check what I've got here and we'll get this plugged in and get started. |
26:20 | So, yeah, when I originally started working with this scanner, I just did the initial scan with my smartphone, did some editing on the smartphone, it's just an iPhone in the app and then I actually could export the mesh file and then sent that straight over to my computer just by airdrop. |
26:44 | So, that made the whole process quite easy and that would be really helpful if you needed to kind of go and scan in maybe more remote areas where you couldn't use a computer or something like that or if you're working in tighter spaces and you didn't want to have this cord tethered to your computer. |
27:05 | So, we're working in the RevoScan app here and I'll just go New Project, any name is fine for this. |
27:15 | So, initially we have a few more settings that we can kind of adjust here when working with this. |
27:22 | The scan settings all over on the right hand side, we'll just work with standard accuracy in this case, feature tracking is fine, that's already gone quite slow. |
27:36 | We're not going to need to use markers because this has a lot of features that we can work with. |
27:41 | The object type in this case is just general, it's not a dark object or body either. |
27:46 | We're not going to do any base removal or anything like that, we'll just keep it pretty simple. |
27:50 | We'll turn the exposure on to automatic there and you can already see that's just lightened up. |
27:57 | Just move this over here, move this into view a bit better and then we'll just get going. |
28:05 | So, one advantage of moving to this scanner straight away over the Moose is it doesn't need the external power source and it also has this start and stop or start and pause , button on the back that I can work with. |
28:23 | So, I can just hit that from here and we'll see already that it is starting to pick up that block pretty well and it's just adjusted the exposure there as it goes. |
28:36 | But you'll see, you'll notice from this that it's quite jumpy I would say. |
28:41 | So, you can see at the top there it's getting 13.4 frames per second. |
28:47 | That's just in the standard accuracy mode, I think it'll go up to 16 in the kind of high speed mode. |
28:54 | But this is kind of the experience that I got with it with all the other scans as well where, yeah it just seems quite kind of jumpy and laggy. |
29:04 | I'm not sure if that's my computer not being up to the specs, but I'm pretty sure it was up to their recommended specs. |
29:10 | But it just makes the scanning process a little bit unenjoyable I'd almost say, but inefficient as well. |
29:19 | And it seems like you have to move the scanner really slowly otherwise it's going to kind of find or make mistakes. |
29:26 | And you can already see some of those holes on that are quite misaligned and those errors are creeping in already. |
29:32 | And I basically haven't done anything, I'm staying in that excellent working range for it. |
29:38 | Yeah, and it's not doing the best job there. |
29:41 | You can see that the field of view is much bigger. |
29:45 | It's losing tracking and I'm not even moving it so there you go. |
29:50 | That's field of view is much larger. |
29:53 | Yeah, I'm just going to stop that before we all get hyper fit. |
29:57 | I'll pause that. |
29:59 | That field of view is much larger so you capture data a lot more quickly, which can make the scanning process a little bit more efficient. |
30:09 | Right other points here, so when I was scanning the AE86 engine bay , which I actually have a photo of here now. |
30:18 | So, it initially seems more promising than the Moose, but again even reaching 12 or 13 frames per second, it just seems very jumpy and it wasn't picking up that data very well. |
30:31 | When I was adjusting the exposure and so on, it picks up those errors as we were just seeing before. |
30:37 | It was basically just taking too long because I couldn't move slowly and quickly around the part. |
30:44 | And saying that the software, which we'll jump into here seems to have a lot more kind of features and a little bit more intuitive and easy to use compared to the JM studio that we're just using with the 3DMaker Pro Moose. |
30:59 | I had the same experience scanning the billet block. |
31:05 | It's slow and laggy like what we just saw here and it picks up errors all the time. |
31:11 | The processing speed was relatively quick though so if we just start at doing the point cloud fusion here. |
31:18 | We'll just leave that kind of resolution at one millimeter and we'll start this processing and as you can see it's moving through that so much faster than that the Moose was. |
31:31 | Which is just strange to me because the scanning speed seems really slow and jumpy, but then the software can process the scan pretty quickly so I'm not really sure what that's all about. |
31:42 | When I moved over to scanning the rear arch of the CRX, there was basically no chance of doing it without the tracking dots on it. |
31:51 | When I put the tracking dots actually on it, so the little positioning targets, it did work, but it wasn't great. |
31:59 | It's still just jumpy and it makes it hard to kind of move around a large area. |
32:04 | But again the processing speed is relatively fast so we can see that that actually cleared up a few of those errors as it processed there on the side of the block. |
32:13 | We've got some other tools here where we can remove kind of isolated areas, smooth the point cloud and so on and then we can just do the meshing here as well. |
32:24 | We should turn the quality down a little bit to keep things going quick and you can see there it's just smashed that mesh out, albeit the resolution is pretty bad. |
32:35 | If I jump back to fused and go mesh and turn the quality right up, we'll see if that makes it a little bit better. |
32:43 | You can see again the processing is relatively quick, but the scanning just doesn't seem to be great and efficient. |
32:50 | Before we move on to the next one, yeah so that made the resolution a bit better. |
32:55 | It's still not great though. |
32:57 | Again, when I was doing the scanning in this case I was just working under standard accuracy so maybe turning that up to high accuracy, which I actually scanned the billet block with, not this one. |
33:11 | I think the resolution was a little bit better in that case. |
33:14 | Again I'll open up those scans soon and we can have a look at them all. |
33:18 | So, I'll just, while I'm changing over these, make the note that if you have any questions you want to ask on these or anything kind of relevant to today's discussion, I'll do my best to answer at the end of the webinar. |
33:34 | Next, up we have the Creality CR-Scan Otter. |
33:44 | Again, it comes in this case, it has the calibration board and so on there, some stickers, positioning targets and we also have the unit in here. |
33:56 | So, something I wanted to note about this, if we grab that Revopoint back again, just looking at these two, you'll see the different amount of cameras or lenses on the end. |
34:12 | So, here we have the projector in the middle and then we have the receiving kind of cameras and then we have the color texture camera here as well. |
34:23 | And you'll notice that on the Creality we actually have two lots of the kind of receiving cameras. |
34:29 | Basically, what that means is we can use, I think it's the ones that are, I'm not sure if it's the ones that are closer together or further apart, but we can basically change the range that the scanner has in the working area that it's using, if we're working on a small part or a large part. |
34:49 | So, it's basically just changing that kind of field of view and it just makes it more efficient for working with a larger part or working with a smaller part. |
35:00 | Makes it a little bit more adjustable to whatever you're working on I guess. |
35:06 | The actual feel of this part, the scanner over this one here, this feels a lot more kind of plasticky and light and this kind of feels like it actually has a metal kind of casing to it and just feels a little bit more solid and better as well. |
35:22 | Not that that matters to everyone, but in some cases it is a good thing if you're spending a bit of money to feel like you're getting a quality product. |
35:32 | So, we'll just put that back there. |
35:38 | And in this case, we'll just close that software. |
35:45 | We just don't need an external power source on this one either, we just have one cable that goes between our scanner and then our USB port on our computer. |
36:01 | So, I'll get that plugged in. |
36:03 | On the back of the scanner we have this kind of light around the outside, the button, which is just shown green at the moment, which gives us some indication I think of how close or far we're working from the part. |
36:16 | And we have the play , button as well as some plus and minus things for working with the exposure and so on. |
36:22 | The Revopoint range actually had a very similar setup, but probably not quite as nice as this and no kind of light indication around the outside as well. |
36:33 | So, open up Creality Scan, it's the software we're working with, and bring the block back into place. |
36:49 | All right, we'll go new project, test. |
36:54 | Okay, so this initially asks us to kind of set up the configuration of the project based on whatever we're scanning, which is basically how we do it with our PL software as well. |
37:07 | The object, just a normal object, we're not scanning someone's face or body. |
37:11 | The size of this I'd say would be medium in this case, seems about right with those dimensions. |
37:17 | We're going to track off features being the geometry in this case, engine blocks really geometry rich, it has a lot of kind of bosses and braces and things like that, which are really good for scanning. |
37:31 | We don't need to scan off the texture or the markers in this case. |
37:34 | We'll just go fast because we're working in a live webinar, we want things to move along quickly and we don't need to exclude the flat base in this case and then we'll just click scan. |
37:45 | Cool. |
37:46 | So, here we go, pointed at it, we've got a preview and we can just hit that button, it gives us a little beep and straight away we can see we've got some kind of errors where it's not working and I did come across this in pretty much every scan I did. |
38:06 | So, let me just see, move closer it's saying, optimal range is a bit closer than I thought. |
38:12 | That seems a bit better. |
38:14 | So, I've just got to keep an eye on that point along the side there. |
38:21 | Cool. |
38:22 | Now, we're going pretty well scanning the part. |
38:26 | I've just got to stay a little bit closer and that's something that I want to talk about as we kind of go as well. |
38:32 | So, doing a lot better here compared to the other ones. |
38:35 | You can see I can move a lot more kind of smoothly and it makes the whole process a lot more efficient and enjoyable I'd say as well. |
38:46 | You're not constantly watching it kind of jump back and forward. |
38:50 | So, that looks really good. |
38:52 | As we work around I'll just make some comments on the parts that we scan. |
38:57 | So, for the AE86 engine bay, the working range, I actually set that to work with a large object, makes a huge difference. |
39:11 | So, working with that other set of cameras it has, I'm going to show you that in a moment actually if I can, just to kind of show how big a difference that makes. |
39:22 | It'll basically capture this whole block all in one kind of thing. |
39:26 | But, what I did notice about it is that the resolution on that larger scan seems to be lacking. |
39:33 | So, probably scanning kind of with this closer up smaller setting at the moment is giving us better resolution. |
39:40 | Whereas when we jump to that larger scan, even if we turn the resolution up when we go to process the data, I found it gave us quite kind of poor resolution kind of look in the results, where if you looked at the holes and stuff, the edges weren't very crisp and so on. |
39:59 | It really looks rounded over like it looks like low resolution. |
40:07 | One moment, we just got a little technical thing. |
40:16 | Cool, all good, should be fixed. |
40:20 | So, I'll just stop that there as we go and I'll just start this processing so we can just go complete scan and let that do its thing. |
40:33 | Cool, so that's already just brought us into this next workspace and from here we can go either one click process or we can do it all kind of manually and change the settings. |
40:45 | We'll just do a one click process and keep things pretty simple. |
40:48 | And while that's doing that, I'll just run through what I kind of found with the other things. |
40:53 | So, with the billet block, working on this kind of medium size setting actually didn't work really well for the billet block. |
41:01 | It doesn't have quite as many features as this block we're working with here and it kind of seemed to lose its tracking a little bit as the field of view just wasn't really big enough. |
41:12 | The large object scanning thing, we'll show this again in a moment, when you have it looking at the larger field of view, it seems to capture the data really efficiently, but it seems to lack that resolution. |
41:26 | Again, we'll jump into that a bit more in a moment. |
41:30 | The processing, as you'll see here, it's not as fast as the Revopoint. |
41:36 | It's quite slow kind of comparatively, but it did scan the black parts on that billet block pretty well. |
41:46 | And then on the CRX rear arch, I was working with the large scan setting and that works really well. |
41:53 | Still seems to lack resolution on that and the processing is just not very fast. |
41:59 | So, rather than waiting for this, I'm just going to cancel out of that. |
42:07 | And hopefully that'll do that for me. |
42:10 | Yeah,, I'll close that current process. |
42:13 | I'll jump into here. |
42:17 | While I have these open here, so this is actually the SR86 block. |
42:22 | So, this was scanned on kind of the large resolution, the large setting, large object setting. |
42:29 | And if we zoom in here, we can see just around the bolt holes and stuff. |
42:32 | It just looks like it's lacking resolution there. |
42:36 | Things aren't very crisp and so on. |
42:39 | Failure of a scan from our Creality unit using that large scanning area on this block. |
42:46 | I'm sure again, if we just clear that and did it again, I'll actually avoid doing that, but we'll just cancel out of this. |
42:58 | Complete scan. |
43:01 | It's not letting me now. |
43:03 | Ok, interesting. |
43:04 | So, if you don't scan anything, you can't just jump back to the home screen by the looks of things. |
43:10 | Yeah, all right. |
43:11 | Well, we'll leave it at that and we'll quit out of that and move on. |
43:14 | Again, when I was using this and working on the CRX rear wheel arch, it actually scanned it completely fine with that large object kind of area. |
43:25 | But when you're scanning on that, it seems to really lack resolution. |
43:29 | That's probably my main point about this, but it captures data and works pretty well. |
43:34 | Ok, just connect that and we'll move on to our fourth and final scanner. |
43:41 | Just making a little bit of a mess behind me here. |
43:45 | So, next up we have the Einstar. |
43:51 | So, I'll just move this out of the way. |
43:55 | Again, the Einstar comes in this nice case and the Einstar also kind of comes in this silicon or whatever it is cover just to kind of protect it as well. |
44:08 | Probably one of the downsides of the Einstar is all of these cables that you have to plug into everything. |
44:16 | So, it needs a power source and it's got this kind of solid power source here, which is a little bit tricky to deal with. |
44:26 | And then it's also got two other cables that you need to work with. |
44:30 | So, we'll get all of that plugged in and then we'll get started. |
44:45 | Yeah, the other thing, along with the kind of requirement for all of these cables and the external power, is it puts quite a bit of load on the computer. |
44:55 | So, if we run into some difficulties again, that'll be why. |
45:00 | And we'll be back with you guys really shortly. |
45:03 | So, what do we have here? This one goes into here, into the laptop, and then this goes into the bottom of the scanner. |
45:17 | All right, now we're up and running and I'll just open up Exstar, which is the scanning software for this. |
45:30 | Ok, so the Einstar is probably the scanner that we get asked the most questions about. |
45:35 | It seems to be really the pick of the industry when it comes to scanners in this price point. |
45:41 | And a lot of people have it and seem to be getting some really good results. |
45:45 | So, when we start a new project here, it's just, again, letting us set that up based on what we're scanning. |
45:52 | So, medium and large object in this case. |
45:55 | Again, we'll just work with tracking features and we'll leave the resolution. |
46:01 | I will bring that down to one millimeter and we don't need to do a texture scan in this case. |
46:08 | We don't need texture for for a part like this. |
46:13 | And we'll open that up. |
46:17 | So, bring this over again. |
46:20 | Cool. So, fairly simple here. |
46:27 | We have some scan settings down the side here if we want to kind of make some adjustments. |
46:34 | And then we can just start a preview from the , buttons in the back. |
46:39 | Again, if we jump under the overhead, it's got some lights on here to showing us kind of indicating things like the working range that we're in if we're too close or too far. |
46:48 | So, I'll just start the scan. |
46:50 | So, this is just a preview. |
46:52 | We can see that it can see everything pretty good. |
46:57 | So, we'll just click go and start that scanning and we can see straight away it's picking it up pretty good, nice and smoothly. |
47:09 | A bit of tracking loss there. It's going to pick up my hand as I kind of rotate this around it as something that we could edit out and post-processing. |
47:20 | And yeah, just like that really. |
47:23 | I've basically scanned the whole block. |
47:32 | Get it from a few different angles. |
47:40 | Make sure we've got all the data we need and then just hit pause. |
47:46 | And yeah, from there we've scanned the whole thing pretty quickly and then we can generate the point cloud from there and insufficient memory. |
48:00 | So, I will try to run this. |
48:01 | We might run into some issues. |
48:03 | No, it's not going to let me. |
48:06 | So, yeah, just lacking the kind of computer memory I think in this case to be able to do this while doing the live webinar. |
48:14 | But we do have some other processing, sorry, editing tools down here. |
48:20 | So, we can basically just make kind of edits to the mesh pretty quickly. |
48:25 | Remove any data we don't want and so on. |
48:29 | And then you move on through here. |
48:31 | It is going to do it this time. |
48:33 | I just had to delete a tiny bit of the mesh. |
48:36 | So, for scanning the engine bay, it's instantly like as you saw a better experience and probably the other scanners. |
48:48 | The working range is really large and it captures a lot of area. We can start and stop. |
48:53 | But one of the annoying things that I found is when you hit preview to originally kind of initially view the part, you have to start the scan to be able to stop it again. |
49:05 | You can't hit preview and then just exit out of it. |
49:08 | So, that was a little bit kind of frustrating. |
49:11 | The software is pretty intuitive. |
49:14 | We just generated the point clouds there and then we can do the mesh model here as well and just leave this all as the basic settings. |
49:23 | And then it will process as well. |
49:25 | The processing goes pretty quick. |
49:28 | For the billet block or just scanning the engine block, I found it's not quite as good as scanning something large like the engine bay itself. |
49:38 | It's definitely designed for scanning larger areas and it does that really well. |
49:43 | Whereas something like our peel does a much better job at this. |
49:46 | And this actually does maybe a better job than the peel at scanning really large areas. |
49:51 | Like if you wanted to scan, I scanned the inside of Ben's Sprinter van with this and it actually did a lot better job than the peel just because it's got a much bigger field of view, which helps with the tracking and so on. |
50:03 | It took a little bit of adjusting to get the exposure right when I was doing the scanning of the billet block. |
50:10 | But it's still relatively smooth and nice and easy for the CRX rear arch. |
50:17 | There was no need to use the markers at all. |
50:22 | It just scanned it. |
50:22 | It was fine. |
50:23 | It has such a big field of view. |
50:25 | It can see enough to kind of get its position and it process really quick and easy as well. |
50:30 | So, I could edit this more and everything, but that's basically a quick scan of the engine block and a matter of seconds, really. |
50:38 | And then we could just save the scan here as an STL file or so on it and go from there and use that. |
50:46 | So, pretty simple. It just does the job and does what it's supposed to do. |
50:52 | What I'm going to do is just see if I can jump out of this. |
51:04 | No, it's not going to let me open file. No. |
51:10 | Ok, I'll just unplug it and close the software and I'll see if I can open some of those files that we were actually working with or discussing. |
51:22 | Now, to give you a little bit more kind of idea of what those scans ended up looking like. |
51:33 | So, we'll start in this case with the Einstein and then just work backwards. |
51:38 | So, I can project group. Bear with me a second. |
51:43 | Block. So, this is a scan of the billet block. |
51:52 | We can see there's definitely more kind of noise in there than this one here, and that's probably just a result of it being kind of shiny. |
52:00 | But that's a scan that we took of the billet block and we'll show you how that could have been used in just a moment or do a little bit of an analysis, at least of the accuracy of the measurements. |
52:14 | If I can go open project, jump back. |
52:20 | CRX rear arch. |
52:26 | Ok, it's not going to let me do that. |
52:33 | So, we'll delete that, close that project and then we should just be able to do that now. |
52:40 | No, it's not going to let me do it like that. Project group, open project, rear arch. |
52:48 | OK, here we go. |
52:50 | So, this is the rear arch of the CRX that we've been talking about this whole time, but I haven't been able to show you. |
52:56 | So, it actually had the tracking targets on it, but you can choose whether you're going to reference them or not. |
53:02 | It is going to use them to some extent because they are kind of they do become geometry features in this case, slight little bumps in it. |
53:10 | But that scanned that all pretty well in that case, and then I'll just open one more project group, see if we've got it here. A86 bay. |
53:20 | Give you a bit of an idea about what that scan looked like as well. |
53:25 | Then we'll jump back into the other ones. |
53:29 | So, I actually scanned this one using the color texture and yet again, picked up the whole thing. |
53:35 | No issues really quickly. |
53:37 | And it's all kind of pretty accurate. |
53:40 | If we zoom in here in this case, it's just a point cloud there. |
53:44 | I haven't actually meshed that yet, but we can see it's all there and it kind of matches the colors of the real thing. |
53:51 | Pretty accurately, I'd say. |
53:55 | Cool. |
53:55 | What I'll do is I'll just show you one other one with the Creality. |
54:03 | Because that was kind of what I would call the second best anyway, and there's probably not too much point looking at the scans from the range and the Moose, so we'll just keep to these and then like I said, I'll share the scans for those other well with all of them on the forum, if you want to go and have a look at them. |
54:28 | So. I actually scanned the rear arch of the CRX with the color turned on with the Creality Scan Otter. |
54:36 | And we can see that that captured that all pretty well as well. |
54:40 | And then if I jump back to home close the current project. |
54:44 | It can open that SR20 block here, which we actually saw before that's looking all pretty good. |
54:51 | And that was actually the best scan of the SR20 block even better than the peel and then the AE86 bay. |
54:58 | Sorry, even better than the not better than the peel better than the Einstar. |
55:03 | And then we've got the AE86 bay again did a pretty good job of that. |
55:08 | So, yeah, that's a very usable scan that we could drop a scan of a engine or something into and design some engine mounts off these points here. |
55:18 | Cool, so we'll just close that and I want to jump on to probably the final point that I'm going to kind of talk about. |
55:28 | Measurements, okay, cool. |
55:33 | Bear with me for one sec. |
55:39 | Yeah,. |
55:55 | All right. Well, those are downloading. |
55:57 | I'll just kind of introduce what I did. |
55:59 | So, basically I used a intermediate software or it's a reverse engineering software called Geomagic Design X. |
56:07 | Some of you might be familiar with it. |
56:10 | It's an extremely expensive software. |
56:12 | It's about $20,000. |
56:15 | I think for a perpetual life perpetual license for the full kind of version of it. |
56:21 | Obviously, you don't need to use that. |
56:23 | There are some lighter options as well. |
56:25 | To be honest, I was just working on the free trial of it just to kind of see if it would work for our application. |
56:32 | And I'll just show you what I did with that. |
56:36 | So, I've got a little it's not going to work. |
56:41 | I'll show you this here. So, this is inside the Geomagic software and this is basically a scan that I took of the block with the Peel in this case. |
56:53 | So, when we're not looking at today, that's our professional level scanner that we mostly use at HPA. |
56:59 | So, we use this auto segmentation tool here and that basically splits the model up into all these different colors that you can see here and kind of recognizes different regions of the model. |
57:10 | After we did that, then I use the solid primitive tool here and then was able to fit these cylinders to the inside of the block. |
57:23 | The actual cylinders, the scans of the cylinders from the block. |
57:28 | And then after I'd fit those to the scan data, I then use the measurement tools down the bottom, which aren't actually shown on this image and was able to take some measurements here. |
57:39 | And this is basically a way that I could extract information from the scan data, take measurements of it, compare that to the real part and then be able to basically get an idea of how the accuracy was for the scans. |
57:53 | So, we'll just jump back and we'll have a look at the Moose first. |
58:00 | So, this is the moose. Actually didn't get a good enough scan of the whole block to be able to get all the data. |
58:06 | But we can see these measurements here, the 43.36, 44.06, 42.6. |
58:15 | That's quite a big range, I know, they're moving around quite a lot. |
58:19 | But those are the radius measurements of those cylinders. |
58:24 | So, if we double those, then we'll end up with the cylinder bore, which we know on a machined billet block like that, even with the sleeves, that's very accurate. |
58:35 | So, actually got those, Brad and Brandon measured those for me and they came out at 89 millimetres, bang on the dot, measured with typical bore measuring tools. |
58:48 | So, in this case we can kind of see that the accuracy is really, there's about 2 millimetres of variation in the accuracy here when we compare it to the 89 millimetre bore. |
59:01 | We could get better results if we spent a lot of time scanning the block, but we'd have to spend about an hour or so just taking the scan, I'd say. |
59:11 | This was probably in the 20 minutes or so that I dedicated to this and it just really didn't give the kind of best results. |
59:18 | We also have the bore spacing shown on here. |
59:23 | So, the bore spacing of the SR20 is 97 millimetres and we can see again we got 97.8 almost here and 95.7 or so here. |
59:34 | So, there's just quite a lot of variation there. |
59:37 | And if we just jump back into the original spreadsheet that I had here, you'll see that the accuracy of the 3DMaker Pro Moose is quoted at 0.03 millimetres. |
59:48 | And it's clearly not that and that's just a point that I wanted to make on these scanners. |
59:54 | They're tested in kind of controlled laboratory environments and what we actually get when we're working with them just in our workshop might be something very different. |
01:00:04 | And obviously, there's a lot of factors that come into this and a lot of that comes down to the user as well and how much time you're going to spend making sure you get it right. |
01:00:12 | But if we're working on real projects with timelines and things like that, this is all stuff that we need to consider. |
01:00:19 | And as we go through these, it'll show you the difference between different scanners anyway I guess. |
01:00:25 | So, let's jump on to the next one here. We'll have a look at the range next. |
01:00:30 | So, in this case we'll look at the bore spacing first. |
01:00:34 | We've got 97, pretty much flat so that one's pretty good, half a mil under here and a bit more than half a mil over. |
01:00:42 | This would end up, this back cylinder measured the bore really accurately if we're looking at a 89 millimetre bore. |
01:00:53 | This one's pretty close. |
01:00:55 | This is about a mil or so under I guess. |
01:00:59 | And this one's pretty close too. |
01:01:01 | So, in the case of the range, the results were actually pretty accurate considering if you actually look at the scan, the scan's horrible. |
01:01:10 | It just didn't pick up much of it all. |
01:01:12 | But what it did pick up on was pretty accurate I'd say. |
01:01:15 | And it's all within a millimetre or so. |
01:01:18 | So, in the 3D scanning space, a millimetre accuracy for a scanner that you're paying $800 or so for. |
01:01:27 | It's not horrible, but it's not great either. |
01:01:30 | So, yeah, we'll move on to the next one quickly, keep things moving. |
01:01:37 | If we look at the CR Scan Otter. |
01:01:39 | So, we have a much better scan of the part here, all broken down into the different regions by Geomagic. |
01:01:50 | And if we just look at these measurements here, 44.6, 44.4, .7, .5. |
01:01:57 | So, I'd say those bore measurements are all within half a millimetre or so, , which is getting much better. |
01:02:04 | And then the spacing here, again, those are all within 0.3 or so millimetres on the bore spacing. |
01:02:11 | So, the accuracy in that case of the Otter is probably a step up from the Range. |
01:02:18 | And I just say that a lot of that comes down to the fact that the range captured not much data at all where the Otter got a really good scan. |
01:02:28 | That was the Moose. |
01:02:29 | So, this was the peel. |
01:02:32 | Yeah, ok. |
01:02:33 | So, we'll move on to the next one here being the Einstar. |
01:02:37 | Again, captured a really good scan. |
01:02:41 | If we look at the bore spacing, 96.8 or 97.1 to 2-ish and 97.3 or so. |
01:02:51 | So, the bore spacing, pretty good. |
01:02:53 | It actually undersized the actual bore diameters by quite a bit. |
01:02:59 | You can see here they're all about 43, high 43s. |
01:03:02 | So, that's pretty consistently undersizing the bores in that case. |
01:03:07 | It actually wasn't as accurate on the Einstar as the Creality unit in that case. |
01:03:14 | And I'm not sure that could come down to a lot of factors. |
01:03:17 | Basically, the Einstar is really good at scanning larger areas, but maybe not so good at scanning kind of smaller parts and really good accuracy. |
01:03:28 | It could just come down to the lighting or the surface texture. |
01:03:31 | There could have been some shadows on it and how Geomagic processed the scan as well. |
01:03:36 | If you scanned it again, I'm sure you'd get slightly different results. |
01:03:39 | But in this case, it does seem like the Creality unit actually got slightly more accurate results on that there. |
01:03:46 | So, it's pretty interesting. |
01:03:49 | And again, I'll just jump back to the Peel scan here. |
01:03:52 | So, this is with our Peel 3. |
01:03:54 | And just make a note of this to kind of show the difference between a professional level scanner and a more entry level scanner here. |
01:04:04 | So, we've got 44.5 there, so that's 89 millimeters, basically 44.4, 44.4, 44.4 almost again. |
01:04:15 | So, really close. |
01:04:17 | That would be within 0.2 millimeters accuracy on the diameter. |
01:04:23 | And then this is almost bang on 97, same with that and same with that. |
01:04:28 | So, the bore spacing, again, super accurate. |
01:04:31 | And I actually did this about 10 minutes before I came over here for this webinar. |
01:04:36 | And it was really easy to scan and process and so on. |
01:04:39 | So, it's just accurate results a lot quicker. |
01:04:42 | But you're paying 10 times the price for the scanner. |
01:04:45 | So, that's what you'd expect as well. |
01:04:47 | But for any of you just wondering if it was worth that step up or if there's any kind of difference there, hopefully that kind of goes some way anyway to show you that there's a significant difference there. |
01:05:00 | But probably someone looking to buy a $10,000 scanner isn't looking at buying a $1,000 scanner and vice versa. |
01:05:07 | Cool. |
01:05:08 | So, I just want to really wrap up with a bit of conclusion and summarize the key points from this. |
01:05:14 | So, we'll start off just by talking about the 3DMaker Pro Moose here. |
01:05:22 | I'll move this out of the way so we can look at it under the overhead. |
01:05:26 | So, basically in the end I probably wouldn't recommend this to someone looking at working on automotive or motorsport projects. |
01:05:34 | If you're on a very tight budget and this is all you can afford, then sure you can absolutely make it work for certain things. |
01:05:43 | But you're going to be spending a little bit more time working on it. |
01:05:47 | Like a bit more time scanning and kind of processing the data to try to get good results as well. |
01:05:56 | I would say it's clearly a cheaper product when you have one of these in your hands and even the kit that it comes with and the software as well is all limited. |
01:06:06 | You can make it work, but if you can stretch a little bit further for some of these other scanners I think that would probably be money more well spent. |
01:06:15 | So, we'll move on next to talk about the Range. |
01:06:23 | So, Revopoint Range 2. |
01:06:27 | Again I wouldn't really recommend it. |
01:06:29 | The scanning kind of experience seemed to be very jumpy and like it wasn't getting good results. |
01:06:36 | It was really hard to scan, but it seemed like the software was pretty good and it processed pretty well as well. |
01:06:45 | It seems like they maybe just have some hardware development or something like that to work on. |
01:06:50 | It might be good if you're really patient and spend a lot of time kind of getting those exposure settings and so on right. |
01:06:57 | But the experiences that I've had with it, it just hasn't been able to do the job that I've been asking it to. |
01:07:03 | The kind of key benefit that I liked for this if you can find that certain environment it will work in is that you can just connect it to your phone. |
01:07:12 | So, if you find something it will scan you can scan it with your phone do that processing just airdrop it to your computer and that's quite a cool feature and something I think we'll see a bit more of with these scanners is having their own screens in the back. |
01:07:28 | Which a lot of scanners have already, but I think that'll be more popular just so you don't have to be kind of tethered to a computer or laptop. |
01:07:37 | So, with the range yeah a bit of work to do there , but maybe as a step up from the moose I would say. |
01:07:45 | We'll jump on to the Creality CR-Scan Otter. |
01:07:50 | I would say this is really good for scanning large objects. |
01:08:00 | It does have quite a bit of versatility or flexibility with the different range of cameras that it has or receivers. |
01:08:07 | It feels like a pretty good product the resolution on the large setting wasn't very good I didn't think the software I found to be pretty good. |
01:08:17 | But yeah, that resolution on the large setting just seemed to be lacking I'm sure you can work around that. |
01:08:24 | I would say possibly the Creality Scan Raptor is maybe a little bit more suited to our use if we're scanning more kind of detailed mechanical parts like this, but I haven't had the chance to use one just yet. |
01:08:38 | And the accuracy of this compared to the other ones when we measured it in Geomagic was the best in this case for this one here for the bore cylinder of the bore of the cylinders basically the spacing was a little bit better on the Einstar. |
01:08:57 | So, that brings us to the Einstar here, which is probably kind of the crowd favorite or what I would recommend the most out of these scanners. |
01:09:09 | It just does seems to do a really good job of whatever you're scanning in whatever environment and it's very easy to use and it scans efficiently as well. |
01:09:19 | The software is also probably the best and I think what this probably comes down to is Shining 3D the maker of the Einstar also produces a lot of kind of higher level professional grade scanners as well whereas some of these other companies aren't really producing the really high level professional scanners that something like Shining 3D or Peel or Creaform so on are doing. |
01:09:47 | So, I think that kind of you get that kind of trickle down effect into a scanner like this where the company behind it maybe is knows a little bit more about what they're doing, but in saying that it is the most expensive of the group and it's also you have the most cables and stuff to be able to use it and then finally as the most processing load on the computer as well. |
01:10:14 | So, that's all something to consider. |
01:10:16 | All right so we've got all of that covered. |
01:10:18 | I'll just jump into my computer and see if there's any questions that I can hopefully answer for you guys. |
01:10:26 | Oh. Bear with me for one sec. |
01:10:35 | Right before we get to the questions I just wanted to quickly say that the software for these scanners is changing all the time there's always updates and there's many influencing factors to these, so just be aware that your results if you did this test might be somewhat different to what I've got. |
01:10:55 | But I have tested a few of them in different environments and I hope that kind of gives an overall bit of insight into comparing these scanners. Cool. One moment. |
01:11:12 | All right questions. |
01:11:13 | Jerry B. "It is above the 1000 limit for the show, but have you gentlemen used the Raptor X yet.". |
01:11:23 | No I haven't used the Raptor X yet. |
01:11:26 | So, I've used our Peel units I've used these four and I've used some Artec units before as well, but that is about it for me. |
01:11:33 | So, yeah I'd love to use the Raptor X, but maybe that's something that we look into next as we kind of sell off some of these other scanners or just move on to some new ones. |
01:11:45 | Seems like the Raptor X could be like I said a little bit more suited to the mechanical design stuff that we're doing with this rather than the Creality, that Otter. |
01:11:55 | Maybe the Otter is better for like scanning engine bays or something like that, but it is quite a bit more expensive for the Raptor X. |
01:12:02 | I think it's around the $3000 price mark. |
01:12:06 | Jerry B. "I've recently used the Einstar for dashboard modelling. |
01:12:11 | The STL has been a nightmare for mesh conversion into a surface and Solidworks. |
01:12:18 | Any upcoming seminars on mesh modelling of non watertight mesh to surface construction.". |
01:12:23 | So, we mostly work in fusion, but I have worked a lot in the past with solid works with mesh files. I would say that Fusion is probably a little bit better at working with mesh files compared to Solidworks. |
01:12:38 | I don't have any plans on upcoming webinars on that topic specifically, but we do cover it a little bit in our 3D scanning course , which I mentioned at the start of this. |
01:12:50 | In that case we are working in Fusion, but some of the stuff there will hopefully be transferable over to Solidworks as most CAD stuff is. |
01:12:59 | If you know how to do it in one software you can probably find a way to do it in another software as well. |
01:13:05 | The surface modelling stuff from a non watertight mesh like what you are talking about, so scan of a surface basically and then trying to reverse engineer it can be quite tricky. |
01:13:16 | It's probably one of the hardest kind of areas that I've worked with 3D scans in as well. |
01:13:22 | But yeah, I would say keep an eye out for that 3D scanning course and the surface modelling work in that. |
01:13:29 | It is limited in that course, we don't dive into it too deep, but it might give you a little bit, a few ideas of maybe how you could do that. |
01:13:39 | Alright, Jake Loth or JK Loth 81, "Will you be doing webinars on how to make the scans usable for reverse engineering or designing off of? If so will any of them be in Solidworks?". |
01:13:54 | So, I probably answered a little bit of this in the previous question. |
01:13:59 | Again, we mostly are working in Fusion and I find it a lot better than solid works for working with mesh files. |
01:14:05 | So, I could do some of them in Solidworks, but again I think it's more kind of usable to do it in Fusion in that case. |
01:14:17 | There will definitely be webinars coming out showing how to do that and it's also covered a lot in that course, the 3D scanning course as well. |
01:14:27 | And some of that stuff in the 3D scanning course is not focused around Fusion at all. |
01:14:33 | We do use it as our primary CAD software in that, but we're also using the 3D scanning software and some reverse engineering software packages in that scanning course as well. |
01:14:44 | So, it's not all just Fusion vs Solidworks in that case. |
01:14:47 | So, yeah, again I definitely recommend checking out that scanning course, but we will look into doing some of that in webinars in the future. |
01:14:57 | Yeah, we'll do some of that probably with the Peel scanner coming up soon enough. |
01:15:04 | Alright, that's all that we have for questions, so hopefully that's given you some insight into more budget friendly 3D scanners and some of you have mentioned some scanners like the Raptor X and so on. |
01:15:17 | If there's anything else that you'd like us to have a better look into let us know and we'll try to line that up for the future as well as some of those webinar topics as well. |
01:15:26 | So, again, thanks for joining us and we'll see you next week. |
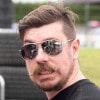