227 | Improving oil supply
Summary
Lubrication related failures are one of the leading causes of engine failures, particularly in engines that are making more power and revving higher than the stock rpm limit. In this webinar we’ll cover some subtle changes that we can make during the engine building process that can pay big dividends with improving the oil supply and return through the engine.
00:00 | - Hey guys it's Andre from High Performance Academy, welcome along to another one of our webinars. |
00:05 | Now today we're going to be covering an engine building topic. |
00:07 | We're going to be talking about some of the changes that you can make to improve the oil flow through your engine. |
00:14 | Now I think this is something that's often overlooked, people think that when it comes to building a performance engine you're kind of stuck with the basic components that you're dealing with and there's no potential to make any improvements or get any performance gains. |
00:28 | The oil system I think is one of those areas that a lot of enthusiasts overlook as well until it gets to a situation where it's causing you problems with engine reliability and bearing damage. |
00:41 | At that point, it gets really expensive really quickly so it's a good idea to spend some time at the beginning of your engine building project, assessing the particular engine you're dealing with, doing a little bit of research into finding out whether there are known flaws or faults in the existing components and then formulating a plan to deal with some of those. |
01:00 | These can be really really cheap, some of them don't even cost you anything more than a little bit of time when you've got the bare components sitting on the workbench. |
01:08 | However when the engine's all assembled and it's sitting in the car and you've got a problem, all of a sudden it becomes much more expensive to deal with. |
01:17 | So as usual with this webinar we will be having questions and answers at the end so if you've got any questions that you'd like me to answer, please add those into the comments, the chat and we'll get to those shortly. |
01:30 | Alright so first of all, what are we specifically going to be talking about? We're going to break this down into areas but basically what we're looking at is an analysis of the existing oiling system in its entirety, we're going to be looking at where the potential areas for improvement are, where the potential weaknesses are that we need to address and then we're going to talk about some of the techniques that we can use to address those problems. |
01:54 | I will just briefly mention here that we do have a couple of other webinars in our archive that kind of feed into this quite nicely. |
02:03 | So we've got in particular a webinar that covers dry sump lubrication systems and we've got another one, I think off the top of my head, it's called creating the ultimate wet sump system. |
02:14 | So check out both of those as well because those kind of cover both ends of the spectrum in terms of cost, obviously a wet sump, relatively cost effective, dry sump there's a fair outlay in terms of dollar value you're going to need to spend in order to get a dry sump system onto your car. |
02:32 | And of course both of those will have a big impact on the entire oiling system. |
02:36 | So those two webinars go really nicely with today's one, check those out in our archive. |
02:42 | So essentially we've got four areas that we want to address here. |
02:47 | The first of these is oil supply. |
02:50 | So what we're talking about here is the components that are going to help us get the oil from the sump and then pump it around the engine. |
02:58 | And what we're talking about here is not just the likes of the pump itself but as you'll find out, there are some improvements we can make to the likes of the oil gallery design. |
03:09 | Maybe some light modifications in the oil galleries there that can really help reduce the losses of oil pressure through the system as it flows. |
03:18 | From there we also need to talk about oiling cooling. |
03:21 | So this is a little bit left field for today's webinar but it is an area that I know a lot of enthusiasts, particularly those who are maybe just getting involved in track days, really tend to overlook. |
03:33 | The reason for this is that in stock form, very few cars have a way of easily monitoring our oil temperature. |
03:40 | The oil temperature can have a big impact on the ability of the oil to do its job, particularly if it gets too hot you find that the oil tends to become thinner, it doesn't offer as much protection to the engine bearings and components and as a result, if your oil is getting too hot, you can easily end up with excessive, severe damage I should say, to your engine components. |
04:02 | The other aspect we're going to look at here, the third aspect is oil return. |
04:07 | So again an area that a lot of people just simply overlook. |
04:10 | Once the oil has been pumped through the galleries, through the bearings up into the cylinder head and in particular up into the cylinder head is a big issue, you've got to get that oil back down into the sump because if the oil is getting pumped out of the sump and around the engine faster than it can return, obviously it doesn't take a rocket scientist to figure out that in no time at wide open throttle and high RPM, you're going to essentially pump the sump dry and you're going to end up with oil starvation and cavitation so another key aspect we need to consider. |
04:40 | And the last topic that we're going to be dealing with today and again one that's really easy to overlook is that just because your bearings are supplied in a packet for your particular engine, that doesn't necessarily mean that there aren't some modifications that you can make to those bearings that can end up improving the flow of oil to the bearings. |
05:01 | Again giving your crankshaft and your conrods a better chance of a long and healthy life. |
05:07 | So with that out of the way, let's start by talking about our oil supply, the first of those topics. |
05:14 | And really this starts with getting the oil into the pump. |
05:18 | So this is really where our wet sump, if you're staying that way, comes into effect, making sure that there's always going to be a constant supply of oil at the pickup. |
05:28 | Now one of the key aspects that is so easy to ignore here is that oil is essentially pretty lazy, it doesn't like changing direction. |
05:39 | So what we want to do is analyse the path of flow for our oil through the oil galleries, through the oil pump, through all our engine components and what you're inevitably going to find in a lot of situations is that there's going to be some 90 degree corners and some sharp edges that the oil needs to go through. |
05:56 | And it doesn't really like doing that. |
05:59 | So what this tends to do is have a knock on effect where it restricts slightly our oil flow, each of the individual restrictions may be quite minor but when you've got a lot of them, they add up. |
06:10 | You can end up having that affect the pressure in the oil system that's actually making it to the key components such as your bearings. |
06:18 | Now because I am reasonably familiar with the 4G63 engine, I thought I'd use that as one of our examples so let's just jump across to my laptop screen for a moment. |
06:31 | And a quick Google search really didn't give me exactly what I was looking for but I'm going to be able to explain it well enough. |
06:38 | So this particular image here shows the front of the 4G63 block and what we've got here on the front of it, you can see we've got a couple of oil galleries basically cast into the engine block. |
06:52 | So this is where our front cover assembly which includes the oil pump, bolts on and basically it pumps oil through those hollows that are cast into the engine block. |
07:03 | Now there's two aspects to that. |
07:06 | First of all, I think I've got another picture here which is really really horrible, I don't know why I couldn't find anything that was higher resolution or bigger but basically again just shows those same two galleries, I think I'll head back to our DSPORT picture because it is a better idea of what's happening. |
07:24 | So the first aspect of this is that inside the oil galleries that you've got here, the part that you can see that is black, that is an as cast finish on the engine block. |
07:35 | So if you've seen any cast iron engine blocks you're going to know that that's a relatively rough surface finish. |
07:41 | So the oil again doesn't like flowing across that rough surface finish and there can be some improvements in oil flow for a really modest amount of time input there just using a air die grinder and a carbide burr to just smooth down that surface. |
07:57 | Now you don't need to go to the trouble of polishing it, that's not really necessary, all we're trying to do is smooth down that surface finish and get rid of the irregular surface, the irregular as cast surface. |
08:09 | The other issue here though, again if we just jump back to our photo, again I'm sorry we can't quite see it in detail there but you can probably get the idea that essentially at the point that I've just circled, the oil has to go through a 90 degree turn and it has to go down one of the oil galleries. |
08:24 | Now again, oil doesn't like doing this, it doesn't like going through that 90 degree turn so as a matter of course on all of the race engines that we built as well as the street engines we built just a few minutes there with a die grinder and a small burr on the end of it, you can just essentially radius that turn just making it easier for the oil to turn down that gallery and that again is just going to help make sure that you're getting as much oil flow to the gallery as you possibly can. |
08:51 | I think if we just have a look at this photo here again this is a billet alloy engine block for the 4G63 and it incorporates the same sort of thing and I can't quite tell from that image whether they've actually gone to the trouble of doing this on the CNC mill, I kind of hope they have because obviously for them it would be essentially no trouble to add that little radius. |
09:15 | So that's our first point there, just being a little bit sensible, analysing the flow of oil through the engine components and seeing if there's any potential to make some small improvements there. |
09:24 | Now the other one that I'm just going to show you here, this is from our Subaru FA20 engine and we'll just try and get this all lined up nicely under our overhead shot here. |
09:35 | It is a little bit filthy but this is the front cover and this is where our oil pump assembly, our oil pump gears get located in here, I've actually, as you can see, I've got a little bit of engine assembly lube in there, looks like I've dummy assembled this and packed it. |
09:51 | So what we've got here is the flow of oil through this front cover. |
09:55 | Once the oil has been picked up and gone through the pump, it gets forced out through in this direction here. |
10:02 | It has to go through a pretty convoluted set of passages here. |
10:05 | In particular it comes out here, we've got a couple of sharp edges that you won't be able to see inside of there, comes down, goes out through our oil filter housing which sits on top of the front cover there. |
10:17 | Once it's been filtered it returns and goes back down through this oil gallery and then it gets spread out where it goes to the various components. |
10:25 | Now there's a couple of issues there, I'll see if I can just get in here with our iPhone camera for a little bit of a detailed view. |
10:34 | Just bear with me and we'll see if we can, yep we can. |
10:38 | So while these aren't the worst, it's about the best example I had easily available. |
10:43 | What we've got in here is quite a sharp edge and I'm sorry it is quite dark in there so this probably is a little bit tricky to see. |
10:52 | We've got a sharp edge in there that restricts flow. |
10:54 | Likewise you can actually see the sharp edge right there does exactly the same thing. |
10:59 | So this is essentially what I was talking about here. |
11:01 | Down here, you can actually see amongst the dirt that I've actually got in there with a die grinder and I've already relieved the sharp edges that were present in there just again to help that flow. |
11:14 | So that's the sort of things we're looking at. |
11:16 | With this FA20 front cover though, things actually get a little bit more involved. |
11:21 | While I haven't got them here, once you go to assemble this, there are some flat plates that get bolted in location on this side of the front cover as well as we've got the same on the other side. |
11:34 | Now by the workshop manual, there is no sealant applied to these and I thought this was a little bit unusual, particularly given that these engines are renowned for relatively low oil pressure problems. |
11:46 | With our own car, on the factory rated oil which is a 0W20, out on the racetrack we're seeing oil pressure getting no higher than about 50, maybe 55 psi when it's hot which is a little bit alarming particularly for a performance engine. |
12:02 | So one small change that we can make to get a bit of an improvement there is to apply a small, very thin bead of a sealant such as three bond around this because what we're going to get no matter how tightly you do up these screws that hold these plates in place, you're inevitably going to get leakage between the machined parts. |
12:21 | Basically it's going to internally leak. |
12:24 | Now that's not necessarily a problem, you're not going to end up with a puddle of oil on the floor. |
12:28 | Obviously the Subaru engineers were happy with the outcome there and felt that that was adequate but for our purposes, particularly again in an engine that is known for low oil pressure, this can be problematic. |
12:40 | So just sealing up those two plates can go a long way towards giving you a bit of an improvement there. |
12:50 | Now the next aspect that sort of goes hand in hand with that though as well is the oil pump itself. |
12:57 | So in some instances you're going to find that particular engines are known to have oil pump gears that have a strength weakness. |
13:07 | A lot of the gears are made from a sintered material which essentially is very prone for failing, fracturing and our course when your oil pump gears fall to pieces you're going to end up with an instantaneous loss in oil pressure. |
13:21 | A good example of one of these particular cars that has this issue, engines I should say that has this issue is the Nissan RB26. |
13:31 | The oil pump gears in stock form, they will fail if you run the engine past around about 8000 RPM. |
13:41 | So there are options there to replace the gears with billet gears that are essentially the same design and stronger, then there are also aftermarket oil pumps which use wider gears which then offer the ability to pump a higher oil capacity around the engine. |
13:59 | So that's our oil supply there, that's going to get the oil out to the bearings, out to the components where we need the oil to be reliably. |
14:11 | The next aspect I kind of touched on briefly is our oil cooling. |
14:15 | So this really is a pretty self explanatory topic. |
14:18 | What we want to do here is make sure that first of all you've actually got an idea of what your oil temperature is. |
14:25 | Monitor that oil temperature, it's reasonably easy to do, there are a range of remote oil filter housings or sandwich plates that go between your stock engine block and oil filter assembly that give you the ability to easily add in temperature and pressure sensors so you really want to monitor that so you know exactly what's going on. |
14:45 | The old story here, if you don't have data, all you've got is an opinion. |
14:49 | So you really want to know where your oil temperature is because otherwise you might find that you potentially could be wasting money needlessly upgrading something that doesn't need to be upgraded so you want to monitor that. |
15:01 | And this a double edged sword particularly for daily driven cars that are track raced as well because it can be just as bad to run your oil temperature too cold as it is to run it too hot. |
15:13 | Oil temperature needs to operate in a certain range for it to be able to burn off the impurities and other nasties that inevitably end up into the oil just as an aspect of running it so for example you're going to get some contamination of the oil with fuel just as one component that's going to get in there that we don't really want in our oil. |
15:34 | So if you're running the oil too cold it's not going to get to a temperature where it can basically get rid of those nasties so yeah you want to sort of keep a good range with the oil temperature you're running and generally I like to see the oil sitting between about sort of 90°C and maybe 115-120°C. |
15:54 | If i'm getting much over about 130, that's a little too hot in my opinion. |
15:58 | Although some oils will handle that better than others. |
16:01 | And for those of you who are running a daily driven car that you do want to compete in, this is where using a thermostatic oil cooler bypass is in my opinion a pretty good move. |
16:13 | Essentially this is a thermostat for your oil. |
16:15 | When it's closed the oil bypasses the oil cooler. |
16:18 | As it comes up to temperature that thermostat will open and allow the oil to flow through the oil cooler. |
16:26 | Next topic is oil return and this is really easy to ignore because we think once we've got the oil to the parts where it needs to go, we don't need to worry about it anymore and that's not exactly the case so again as I mentioned briefly there, if we can't get the oil back out of the likes of the cylinder head, then that's going to be problematic because we're going to end up draining the sump. |
16:50 | So one of the common ones, again without trying to beat on the RB26 too much, one of the common modifications there with the RB26, if we jump across to my laptop screen, is to fit an external oil drain to the back of the cylinder head. |
17:06 | So that bolts onto the back of the cylinder head and allows the oil to drain that's gathered up in the cylinder head, particularly under acceleration it's obviously going to end up at the back of the head. |
17:16 | This can end up being drained back into the sump or depending, if you're running a dry sump system, you can run a scavenge stage directly off the cylinder head. |
17:25 | So that's going to help evacuate that oil back out of the head. |
17:29 | Now one of the early cars that I was involved with that had a lot of problems with oil gathering in the head was the old Toyota 4AGE 16 valve. |
17:39 | So particularly this was an issue in rear wheel drive form. |
17:43 | So I've got a rocker cover here that we'll just have a quick look at. |
17:47 | Excuse the current condition of this but these engines are getting a little bit long in the tooth now So this is the right hand side rocker cover, I can't really say driver's side and passenger side because obviously a lot of you are from the U.S. where you drive on the wrong side of the car. |
18:03 | What we can see though is we've got this breather in the rocker cover and this is facing to the right hand side of the car in a north/south longitudinal installation. |
18:14 | So what we found with these engines, particularly if they were seeing sustained high RPM, is they would pump a lot of oil up into the cylinder head. |
18:21 | Which on its own wasn't a huge issue but in stock form this particular breather here went through to the intake manifold. |
18:29 | It was a PCV valve so under high sustained RPM, wide open throttle, it wasn't open, it wasn't feeding oil into the inlet manifold. |
18:38 | But when the driver was off throttle, particularly when the car was going around left hand corners, what would happen is the oil would end up flowing into the intake manifold and the car turned into a smoke machine. |
18:50 | So there's a couple of issues at play there, one is the oil drain back out of the cylinder head, the other is obviously just a really poorly thought out design with that system. |
19:00 | Probably would have worked fine on a street car but not under the sort of lateral G forces that we see in race applications. |
19:07 | So that's sort of what we're looking at there and there's a couple of aspects, so we've got the oil drain, the external oil drain from the cylinder head, the other thing that's really important to just give some consideration to is the actual oil drain back through the top of the engine block so haven't got a really good example for this but let's just have a quick look over with the iPhone here. |
19:29 | So this is the top of an FA20 engine block and we've got the oil galleries that go back into the engine block, back into the crankcase and some engines are better than others as with most aspects of their design. |
19:42 | And in some engines we're going to find that those oil galleries that flow back from the cylinder head into the crankcase are quite restrictive. |
19:52 | So again a little bit of manipulation there, a little bit of modification, smoothing them out, removing sharp edges. |
19:59 | Sometimes grinding material out in a more significant way can really help get that oil back into the crankcase and the sump quicker. |
20:10 | Now another aspect with this and again I'm really struggling here to find high quality photos today on the internet, it's not my day but again we'll jump across to my laptop screen here. |
20:21 | So this is another component that is again commonplace with the Nissan RB engines which is the oil restrictor that goes in the block. |
20:28 | So not a lot of context around this but basically we've got an oil gallery that flows up from the engine block to supply oil into the cylinder head. |
20:35 | And in stock form there is a small restrictor in the gallery however particularly in engines that are running under sustained high RPM operation, that allows too much oil flow up into the cylinder head and this can just exasperate that problem of draining the sump and then obviously the oil drains have to support more oil flow. |
20:58 | So it's common to end up fitting a smaller diameter restrictor, this particular image I think is from Tomei but basically anyone can supply these restrictors for the RB engines. |
21:07 | Goes down to, I think off the top of my head from 2mm to 1.5mm so restricting the oil flow up into the cylinder head meaning you've got more of that oil down in the sump. |
21:19 | It also means that you're going to end up with higher oil pressure at the bearings which is where we need them. |
21:25 | Now a lot of people might be thinking well that's all well and good but don't we also need oil flow to the cylinder head? And yes absolutely we do. |
21:32 | But in particular with a solid lifter bucket and shim design like the Nissan RB, we don't need as much oil as we're going to be getting under sustained high RPM operation. |
21:45 | So that goes hand in hand with the rest of our modifications in terms of making sure that all of that oil can get back down into the sump really easily. |
21:55 | Alright we've got one more aspect to talk about, so this is a good point to mention that if you do have any questions, now's a great time to ask them and we'll get into those shortly. |
22:05 | The last topic is our engine bearings and as I mentioned, this is something that most people take out of the pack, take for granted and they install and as long as the bearing clearance is where it needs to be, job done, they don't think about it any further. |
22:18 | However, that's not to say that there aren't some modifications that we can end up making here that can improve things. |
22:26 | Now I'm going to talk about some of the issues we struck with the early Mitsubishi 4G63 engines. |
22:32 | This wasn't as well known with the Evo 1-3 engines but particularly for those of you in the U.S., the DSM 4G63, the Eagle Talon et cetera, were well known for a engine failure mode called crank walk. |
22:48 | And essentially what happens there is that the thrust bearing eats its way into the thrust surface of the crankshaft and over a period of time we end up with excessive thrust movement of the crankshaft backwards and forwards in the engine block and that's generally a pretty nasty and expensive mode of engine failure. |
23:06 | So because our original race program was consisting of the Evo 1-3 blocks which for all intents and purposes were very similar in the thrust bearing design to the six bolt Talon Eclipse motors, we had to develop our own fixes for that. |
23:22 | So I want to, I don't have a 4G63 thrust bearing here to show you which is a bit of a shame but I'm going to do my best here with one out of a FA20 so let's just go to our overhead shot here. |
23:38 | So this is essentially what the 4G63 thrust bearing arrangement looked like. |
23:43 | This is the centre main so it's a one piece bearing setup where we've got the main bearing and the thrust bearings all in one. |
23:50 | So the first issue we had with the 4G63s and it's not really well represented here, we can see we've got oiling holes through the bearing so these need to align with the oil gallery machined into the engine block, so that's how the oil gets from the gallery out into the bearing and obviously through into the bearing surface to protect the bearing and the crankshaft journal. |
24:12 | Now probably this bearing here that I've got is a better example of this. |
24:15 | So this looks a little bit more similar to the 4G63 bearings where we've got this slot that is machined by the bearing manufacturer into the bearing material. |
24:25 | So the problem, the first problem we struck with the 4G63 is that the location of that slot actually didn't align perfectly with the hole for the oil gallery. |
24:38 | So it was actually purposefully restricting the oil flow out into the bearing. |
24:42 | So that was the first modification we ended up making. |
24:46 | In the early days we were modifying these bearings by hand just using a die grinder, obviously being incredibly careful. |
24:54 | In the end because we were doing so many of these, we had a local machinist who was set up on a mill to make these modifications a little bit more consistently and a little bit more relaibly for us. |
25:03 | So it's just a case of extending that slot. |
25:05 | So again if we look at our bearing here, we'd just extend the slot out so that it fully exposes that oil gallery and allows full flow out onto the bearing surface. |
25:16 | Another one that I'll just talk about here that we've just recently struck, this is covered in our practical engine building course for our Nissan SR20 VE race engine, there are a couple of generations of the SR20 DE, DET block. |
25:30 | Particularly there is a variant that went into the Nissan GTiR, so that's the N14 Pulsar. |
25:37 | And there are some subtle but important differences in the N14 version of the SR20 DET, particularly around the main bearings. |
25:45 | They have more lubrication holes. |
25:47 | So it is possible to retrofit the N14 main bearings into a conventional rear wheel drive SR20 DET but it does require some machining modifications to the engine block by your engine machinist so it's not something that you can easily fit in your home workshop and needs to be thought through. |
26:05 | So again just getting more oil flow to that bearing. |
26:08 | Now the other aspect though that went hand in hand with getting more oil flow to that centre main bearing was actually getting more flow to the thrust surface. |
26:15 | So again if we can jump to the overhead shot here. |
26:19 | So this is the thrust face, so this is what the crankshaft runs against. |
26:25 | And we've obviously got one side that is loaded, it's loaded when we put our foot on the clutch and that's why these thrust bearing failures were exasperated by cars that were fitted with heavy duty clutch and flywheels assmeblies, there's a lot more pressure involved. |
26:40 | So we decided that we weren't getting enough oil flow down onto the thrust surface of the bearing. |
26:46 | So what we did and again don't have the modification specifically done but I've drawn out what we did here with a sharpie marker. |
26:54 | What we got our machinist to do was just mil a very small, about 1.5-2mm slot down through the surface of the thrust bearing and we basically made these T shaped grooves. |
27:07 | And what it just allowed was more oil flow to actually get down onto the thrust surface of the bearing and then get between the bearing surface and the crankshaft. |
27:17 | And just that subtle little modification there, we went from having an occasional thrust bearing problem, probably one out of maybe 10 or 15 engines, to essentially I think once we did that modification we didn't see another single failure. |
27:33 | So it's just a understanding of what's going on, an understanding of the implications of the oil path through the engine and then looking at what you can actually improve that may help you alleviate the problems that you're seeing. |
27:48 | Now again not every engine is of course the same. |
27:52 | You can't apply what I've talked about here to every engine and think that you're going to get results and the first port of call really comes down to doing a little bit of research into your own particular engine, finding out where others have had problems. |
28:06 | Don't go reinventing the wheel. |
28:07 | Particularly if you're dealing with a popular engine for modification and I'll bring the RB back in again because it is a very popular Japanese engine. |
28:16 | There's a wealth of knowledge on any Skyline or RB forums about the extensive number of problems these engines have with their oiling system and just as an extensive list of solutions to combating those problems. |
28:31 | So that's the first place to spend time because it's not going to cost you any money. |
28:34 | Once you've got an idea of where the problems are and what the solutions are then you can start applying them. |
28:39 | And again, yes some of them will cost you money, a lot of them it's just going to be a little bit of time with a die grinder and for some relatively subtle modifications you can get quite significant improvements. |
28:50 | Alright we'll have a look and see what we've got in the way of questions now. |
29:04 | Toothless has asked, what's the best way to upgrade the oil system on a 5.7 litre LS1 gen three as I want extra flow of oil to have an oil cooler. |
29:13 | OK that's actually a good question. |
29:15 | Just out of shot at the moment I am just piecing together an LS1 stroker engine that is going to be in a worked example for our practical engine building course. |
29:25 | Now with this, I did do a bit of research into the range of options available for aftermarket oil pumps, it's pretty extensive as you can imagine with the popularity of those particular engines. |
29:36 | So what I'd say is it's going to depend a little bit on your application and it's going to depend on your budget. |
29:42 | I know from previous experience with the LS3 race motors that we were involved with a number of years ago, if you keep the factory oil pump and you fit an external oil cooler, you are going to end up with a reduction in oil pressure, probably no big surprise there. |
30:00 | But most of the LS specialists will be able to supply a high flow pump. |
30:05 | If budget is not an issue though I seriously would consider, if you're getting out on the racetrack, considering a dry sump system. |
30:14 | Some of these are pretty cost effective now because again with the LS platform being so popular, they're made in numbers that the economies of scale bring those costs right down. |
30:25 | It might seem like overkill and an unnecessary expense but it can actually end up looking pretty cost effective if it saves you an engine. |
30:39 | Dru has asked, have you heard of drag engines with no oil filters and adding graphite powder to the oil? Pros and cons of doing that outside of messy oil? I have never run anything without an oil filter and I'd be pretty hesitant to do so. |
30:56 | Yeah not a technique that I can really comment on, not something I've been involved with sorry. |
31:02 | BA_67 has asked, any oiling issues with the GM Gen 3 or Gen 4 blocks aside from the pickup tube o-ring leaking air, Moroso makes a fix for that, and cleaning out the drain edges on the factory heads. |
31:16 | Look again it sort of, in the same vain as my reply to Toothless there, it really depends what you're trying to achieve. |
31:24 | For a lightly modified street engine, there's absolutely no problems, these engines are very very reliable and fairly well proven. |
31:30 | As I've just done with our LS1 stroker engine, I've gone to the trouble of some light clean up of some of the casting dags and the sharp edges as I've sort of talked through today but beyond that I see no need to make any serious modifications there. |
31:49 | Jack has asked, what do you think about putting a little bead as small as possible of sealer between the oil pump body and the cover? Do you think a little added layer may create more clearance and then the gain may be lost because of more rotor to cover clearance? Yeah I'd be a little bit hesitant to do that. |
32:05 | Now I know that I talked about this essentially with our FA20 front cover but that clearance, as you've kind of alluded to there, the clearance between the gears in the oil pump body and the backing plate and of course the other part of the oil housing, are absolutely critical to the pump's ability to work efficiently. |
32:21 | So if you increase that clearance you see a really sharp drop off on the oil pressure, so sort of pretty much exactly as you've guessed there, you're likely to find that any gains you get in terms of holding more oil in are probably going to be lost in terms of the added clearance so that is why you'll basically find that it's very uncommon for OE manufacturers to call for a sealant between the oil pump housing and the backing plate. |
32:50 | Matt has asked, is it still practical or useful to paint the valley and/or the cylinder heads to aid oil returning back to the sump? This is an old hot rodding technique and I have never personally used it. |
33:04 | So there are special paints available that are designed for this purpose that basically shed oil and the idea here is that they help the oil return quicker to the sump. |
33:16 | Personally I don't know if the added effort is worth it, in other words I'm not sure if the juice here is worth the squeeze. |
33:24 | And I've always been a little bit hesitant to do so because I don't want to risk paint flaking off inside of the engine. |
33:32 | I think that's going to do more harm than good. |
33:35 | It isn't a bad idea to, as I've sort of alluded to there, on the oil drains, clean up the rough surfaces and casting dag to help the oil drain back. |
33:45 | I just don't know if I'd personally bother going to the trouble of painting it. |
33:49 | Or actually I do know, 'cause I haven't done it so that probably speaks volumes there. |
33:54 | If you are going to be cleaning up those components as well, don't chase your tail trying to get a mirror finish. |
34:00 | It can be quite a rabbit hole that you dive down there, you start just trying to smooth off the rough dags or casting flash and you end up finding that eight hours later, you can see yourself on the inside of your cast iron engine block, not necessary, a lot of wasted time for no real benefit there. |
34:19 | If you're going to be concentrating on doing that, just look for the low hanging fruit, just get the worst of those rough surfaces and just smooth those out lightly. |
34:28 | Jack has asked, is there any benefit to any oil additives? I've always been of the opinion if a chemical was that good, it would already be in the oil. |
34:35 | Yeah Jack look I don't get too deep into the chemistry of oil, that's certainly not my specialty, there are a lot of sites that cover some of those additives. |
34:47 | I think I'm probably with you in that I have shied away from oil additives, thinking the same thing, if you're spending a huge amount of money, I run really good quality full synthetic oils. |
34:58 | If you're spending the money on a good quality oil, chances are that the manufacturer of the oil probably knows more than I do about what additives should be in there and I sort of see the opportunity to make things worse not better. |
35:10 | Probably the only one I will mention that we did use regularly in my old shop was an additive which was absolutely magic in quieting down noisy hydraulic lifters in the 4G63 engines although the real fix for that is probably to fit a new set of hydraulic lifters, of course not all customers wanted to spend the money on that. |
35:34 | Madmax007 has asked, can we replace the spring on the oil pump relief valve with a higher tension, thereby improving the oil pressure? Yes you can do that, it really does depend on where that relief valve is set. |
35:47 | So I think in the engines that I've dealt with, the only time, I've done that one time which was on a Mitsubishi Evo 4 block which is probably the orphan of the 4G63 family and is known for having probably the worst oil control problems of all of those engines. |
36:06 | The oil relief valve is obviously designed to do a specific job and release oil at a specific pressure so we don't end up with a situation where the oil pressure is dangerously high. |
36:17 | Oil pressure is our friend but of course it's not a case of if some is good, more is better. |
36:23 | You want to control that maximum oil pressure, otherwise you can end up with problems like actually having your oil filters fail so I'd be very hesitant to do that. |
36:31 | You'd want to start by monitoring your oil pressure, find out what you've actually got there and then make very small changes. |
36:39 | Rather than swapping to a stiffer spring, I would probably more suggest that you actually add a shim between the spring and the relief valve. |
36:49 | That way, if you shim that by maybe 1, 1.5mm at a time, you can step up and sort of start to see the effect of that change and what it's doing to your oil pressure. |
37:00 | My rough rule of thumb there for oil pressure is I like to see around about 10 psi of oil pressure per thousand RPM so if we've got an engine that's running to 6700 RPM, ultimately I'd like to see somewhere around about 60-70 psi peak at normal operating temperature. |
37:20 | Joneskyle88 has asked, is oil pressure or oil volume more important? Well the two kind of go hand in hand, in order to get pressure, you need to have volume. |
37:35 | And I think this is something that's really often misunderstood. |
37:37 | So the easiest way I'd liken it to is a fuel system, actually I think this is a better visual. |
37:42 | So if we've got a pump that's providing one litre of fuel flow per minute and we've got our injectors also providing one litre of fuel flow per minute, we've got no excess of fuel flowing into that fuel system so basically we can't build pressure. |
38:01 | In order for us to end up with 45 psi or whatever pressure we want in that fuel rail, we need to have a slight excess, in other words the fuel pump needs to be able to provide more fuel flow than the injectors are using and essentially this is the same situation we get with our oil pump. |
38:20 | Our oil pump, in order to create pressure has to pump a volume of oil. |
38:24 | So if we increase the volume of oil that's being pumped, all other things being equal, we're going to end up seeing our oil pressure rise, of course our relief valve is there to deal with that so the two can't be considered independently of the other. |
38:43 | Barry has asked, what's your views on running an under driven oil pump sprocket gear to prevent cavitation at high RPM? Yeah this is something we actually did on some of our 4G63s. |
38:54 | It was a hell of a lot of work given the way the oil pump is driven on the 4G63, until we went dry sump and the reason for this is we were running these engines to 10500, maybe 11000 RPM at times. |
39:07 | So it wasn't, it was just a precaution more than anything. |
39:12 | I think you'd probably really want to know that you have a serious issue that needs to be dealt with before you worried about slowing down the oil pump. |
39:20 | The flipside of that coin as well is if you slow down the oil pump, you may be in a situation where you can struggle to get oil pressure at idle. |
39:27 | So often this will require you to pump up the idle speed quite considerably in order to keep everything safe at idle. |
39:39 | Jack has asked, what do you look for in an oil filter in order to have an idea of its quality? The bypass valve, the filter quantity or something else special? Yeah that's a tricky question to answer there Jack, I think the reality of this is that oil filters, there's a lot of marketing hype involved in them. |
39:58 | I certainly couldn't sort of say for one particular filter that the specific features compared to another filter that looks similar, one better than the other. |
40:09 | My main aim really here is to use a high quality filter. |
40:14 | Often the best solution there is actually to use the original equipment manufacturer's filters, they generally are made to a higher quality than a lot of the aftermarket filters. |
40:25 | In the aftermarket, particularly on our racecars where we're using a large diameter oil filter that's purposefully designed for racing use, with a remote oil filter housing, we've gone with FRAM. |
40:38 | For no other reason than I've kind of been using FRAM through my entire automotive life and I have had good results from the FRAM filters. |
40:46 | And you tend to become a little bit superstitious, in other words if you've got a product that is working, then I tend to stick with it and I think a lot of engine builders are the same. |
40:57 | Alright that's taken us to the end of our questions there, thanks for all of those questions. |
41:01 | As usual if you do have any more, please ask them in the forum and I'll be happy to answer them there. |
41:06 | Thanks for joining us and I look forward to seeing you next time. |
41:10 | Now for those who are watching today on our YouTube channel, this is just some insight into what we put on every week for our HPA gold members. |
41:16 | Now gold members are able to review these webinars in our archive at any time at their leisure and we've currently go over 220 hours of existing content covering topics on engine building, engine tuning and wiring. |
41:30 | There's an absolute gold mine of information in there and one of the fastest ways to expand your knowledge on a wide range of topics. |
41:37 | As a gold member you also get access to our member's only forum which is the best place to get answers to your specific engine building, tuning and wiring questions. |
41:46 | You can purchase gold membership for $19 USD a month however if you purchase any of our courses you will get three months of free gold membership. |
41:55 | So you can check all of our courses out at hpacademy.com/courses Thanks for watching, hopefully we'll see you online again soon, cheers. |
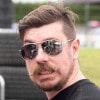